The Lower Broadway entertainment district in Nashville hardly ever sleeps. It’s full of honky tonks, restaurants, bars and museums, and the entire area was added to the National Register of Historic Places in 1980, making changes to existing real estate nigh impossible.
That was the situation DPR Construction found itself in when it began work on Jon Bon Jovi’s (JBJ’s) Nashville, near the corner of Broadway and 4th Avenue, now the tallest live entertainment venue on the street. The simple honky tonk is rapidly becoming a thing of the past, with top Nashville stars adding their names to four- and five-story performance spaces with multiple balconies, stages that span at least two floors and electrical needs that tax the aging historic infrastructure.
Lainey Wilson, Luke Bryan, Miranda Lambert, Jason Aldean, Blake Shelton and only-a-little-bit-country Kid Rock all have music venues/bars in the entertainment district and Morgan Wallen will soon be joining them.

The first three levels of JBJ’s Nashville have open views of Broadway and the venue’s stage, allowing lifts to be used for work on those floors.
Photo by Bryan Adams/DPR Construction
“Livin' on a Prayer”
JBJ’s is owned by Big Plan Holdings, with Bon Jovi himself as a partner. The 0.16-acre site, a former parking lot, had problems from the start in April 2022 that were serious.
The DPR team had to nestle five stories and 37,000 sq ft of entertainment space into a narrow L-shaped structure between Losers Bar on 4th and Nudie’s Honky Tonk on Broadway, both historically protected buildings. A third protected building, the Merchants Building, stands on the corner of Broadway and Fourth in front of Loser’s. None of the buildings could be disturbed as business went on during construction. Most bars close at 3 a.m. on Lower Broadway, but they open up again by 10 a.m., and all kinds of entertainment happens on Broadway during the day, including the recording of the National Football League’s schedule announcements.
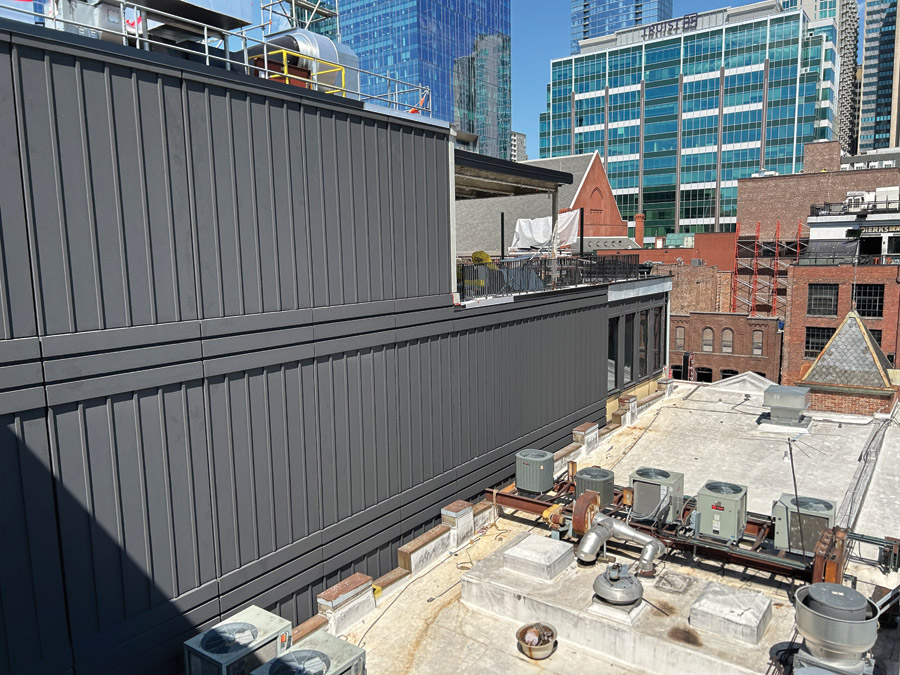
The Upbrella system allowed DPR to place all of its panels within the time period specified to keep the project on track. The self-perform team’s record was 16 panels in one day.
Photo by Bryan Adams/DPR Construction
The mass of foot and vehicular traffic made closing the streets and sidewalks a non-starter with the city. With no room for a tower crane, another solution would have to be found. DPR would need to construct the building directly against the public sidewalk on both 4th Avenue and Broadway and within inches of the historic buildings. Swinging of materials over the roofs or streets nearby was simply out of the question. With exception of a lane closure on 4th Avenue where DPR dumpsters and bathrooms were situated, laydown space did not exist.
To support five stories and 70 ft of height, DPR had to do an excavation and had hoped to find plenty of stable rock to support the venue. Exploratory surgery revealed a different story.
“[The panels] come within inches of those surrounding bars.”
—Brent Bunting, Nashville Business Unit Leader, DPR Construction
“It ended up being a lot more soil than rock, just a lot more soil than we anticipated,” says Samantha “Sam” Rowland, senior project engineer at DPR. “We had to use a soldier pile breaker system that covered, basically, the entire footprint of the building. We did not have any rights to cross over property underneath the buildings or up above, so we couldn’t use any soil nails or anything like that. So we had micropiles all around the perimeter. It was a very extensive excavation process.”
While geotechnical contractor Rembco worked on preparing the site, a process that took 10 months, DPR and its virtual construction team focused on its crane-less movement-of-materials challenge. Since JBJ’s, like most of the new generation of Nashville honky tonks, has an interior that makes the stage visible from the first three floors, lifts positioned on the ground floor could carry materials through the atrium. The bigger problem was placing the prefabricated panels that make up the building’s exterior skin. On the outside of the building, steel could be erected traditionally, but once the skeleton was up, space was at a premium.

The schedule called for rotating trade contractors to perform mechanical, plumbing and electrical work on a tight schedule, requiring all trades to take part in preconstruction BIM coordination.
An Uplifting System
“[The panels] come within inches of those surrounding bars,” says Brent Bunting, DPR’s Nashville business unit leader. “It was a lot of coordination, below grade, above grade, that we had to do with the neighbors.”
Rowland says the clearances from where the panels had to be placed next to neighboring walls varied; “between the buildings, it depends on where you’re at. Some places it’s 12 inches, some it’s three inches.”
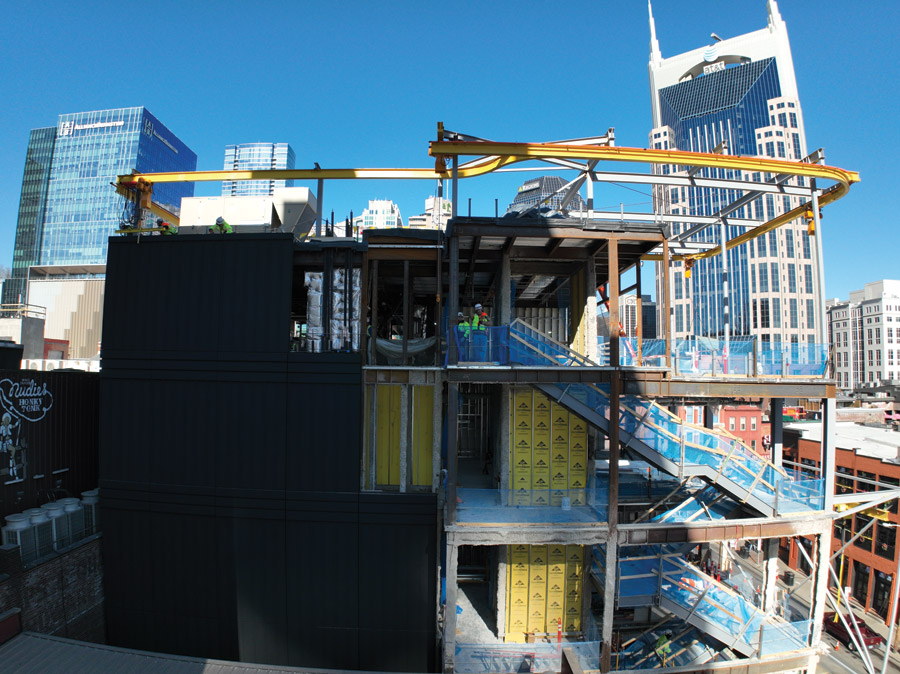
DPR’s BIM coordination created a proper sequence for moving each panel thanks to early BIM collaboration with Upbrella’s team, steel erector SMS and architect Centric.
Photo by Bryan Adams/DPR Construction
DPR turned to the Upbrella system, a solution from Boucherville, Quebec, that uses a monorail and trolley setup that can be mounted to a building’s steel frame. Instead of swinging the heavy exterior panels over neighboring buildings, which would have required neighbor permission and permits, Upbrella deployed its monorail system with trolley cranes that carried the panels into place around the site and only the site. Upbrella has been used on five projects in Canada, one in Monaco and now at JBJ’s.
“Between the buildings, [clearance] depends on where you’re at. Some places it’s 12 inches, some it’s three inches.”
—Sam Rowland, Senior Project Engineer, DPR
Jacques Gauthier, Upbrella’s director of business development, met DPR’s Charlie Dunn in 2019 and introduced him to the system. Dunn, DPR’s project storyteller, recommended it to the Nashville team.
“My understanding is that they had something like six weeks to get the facade up,” Gauthier said. “We calculated all the radii so that they can move all those panels without ever encroaching 1 millimeter on neighbors.”
Upbrella also helped save space on the tight site by taking the panels directly from the trucks delivering them instead of needing to make space for a laydown yard before placement.
“It’s basically a structural steel system mounted to the roof, like you would for a window washing system,” Bunting explains. “It has a trolley line, all the way around the perimeter of the building, kind of like a gantry crane inside a warehouse. That trolley crane rides all the way around and goes to where you’re going to pick material up. At the ends of the L-shaped site, we would have delivery trucks show up, pick off the truck or just off the truck beside it on the ground, hoist the facade up and then trolley it around to, ultimately, where it gets installed.”
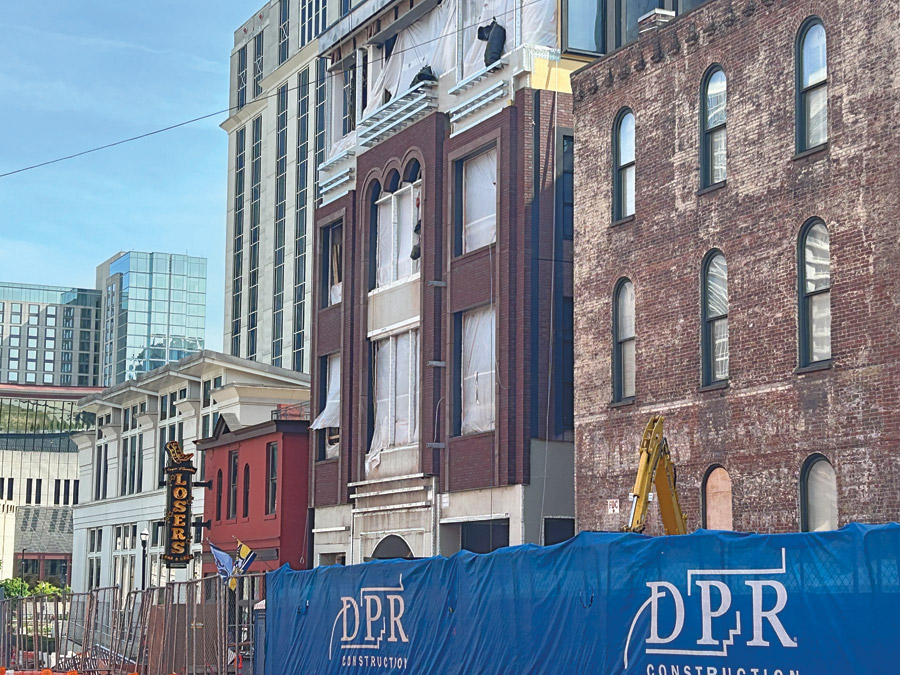
The side entrance of JBJ's had to be built between Losers and the Merchants Building, both historic buildings. The single lane closure on fourth was the only laydown space DPR had, barely enough for the contractor's dumpsters and bathrooms.
Photo by Bryan Adams/DPR Construction
Once at the placement location, the trolley crane lowered the panels into place and DPR’s self-perform team secured each panel to the floor deck from inside the building. It was the first time Upbrella was used in the U.S. Rowland and DPR’s VDC team used the project’s building information model to plan the “flights” of the panels around the building— through the necessary tight spaces and through to installation.
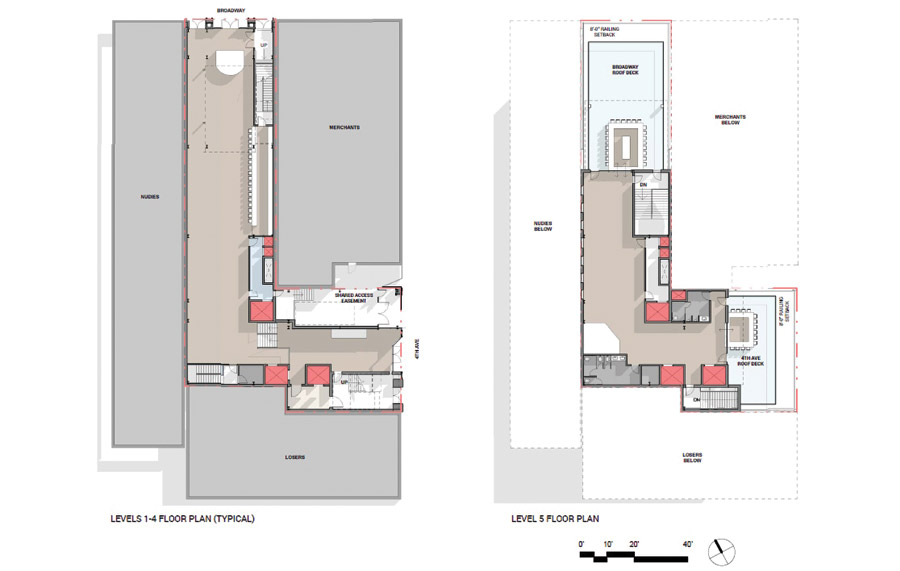
The L-shaped site that JBJ’s Nashville had to fit into was a former parking lot squeezed between three historic buildings.
“There was nowhere you could put a crane so that counterweights wouldn’t be swinging over [neighbors or the street] at some point. So Upbrella really was the only feasible option that we could find that allowed us to put the skin on,” Rowland says.
Rowland says that the Upbrella team DPR worked with engineered the whole system and modeled it for DPR so that it could be incorporated into the contractor’s BIM coordination.

Centric Architecture’s floor plans allowed for three floors of performance space, two bars and a rooftop that’s the highest on Broadway.
“They were very easy to work with, and they were able to contract with our steel erector. We didn't have to bring in another contractor. With the trolley cranes that we used on the monorail, we were able to train our own self-perform crews to run it,” she says.
The exterior panels were prefabricated by supplier Forge out of its facility in Atlanta, and when they arrived on site, DPR’s self-perform crews got into a good rhythm. The highest production day was 16 panels in one day, and DPR easily made its placement deadline. Southeast Miscellaneous Erectors and SteelFab Inc. are the steel erector and fabricator for the project.
DPR also worked with architect Centric before any panels were placed to sequence the panels properly for installation.
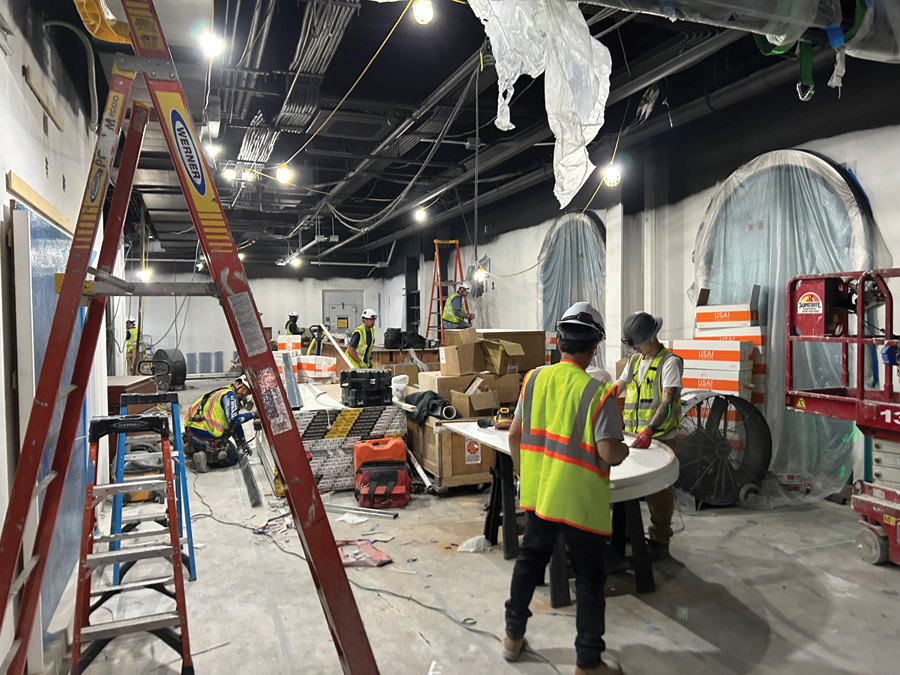
DPR, Volunteer Electric, ICON Mechanical and Merryman-Farr made the most of the limited space—around 8,000 sq ft per floor—within the footprint.
Photo by Jeff Yoders/ENR
It’s Electric!
“We calculated all the radii so that they can move all those panels without ever encroaching 1 millimeter on neighbors”
— Jacques Gauthier, Director of Business Development, Upbrella
For the three-level stage that Bon Jovi and other bands play on, BIM coordination was also important due to the electrical and mechanical needs of modern performance.
There’s an audio/visual rack below the second level of the stage, and all the cables run through the floor to the AV rack. The bottom tier of the stage houses the subwoofers and other large speakers, and that whole box is concrete, but the actual decks where band members stand is steel structure with slab-on-metal decks. All penetrations were coordinated through DPR’s BIM model.
Volunteer Electric did all of the electrical work, and two trades, Merryman-Farr and ICON Mechanical, placed all of the mechanical equipment in the 37,000-sq-ft space.
“We’ve got a lot of different groups rolling in here, and we were able to do that thanks to an extensive BIM coordination that took place over almost a year,” Rowland says.
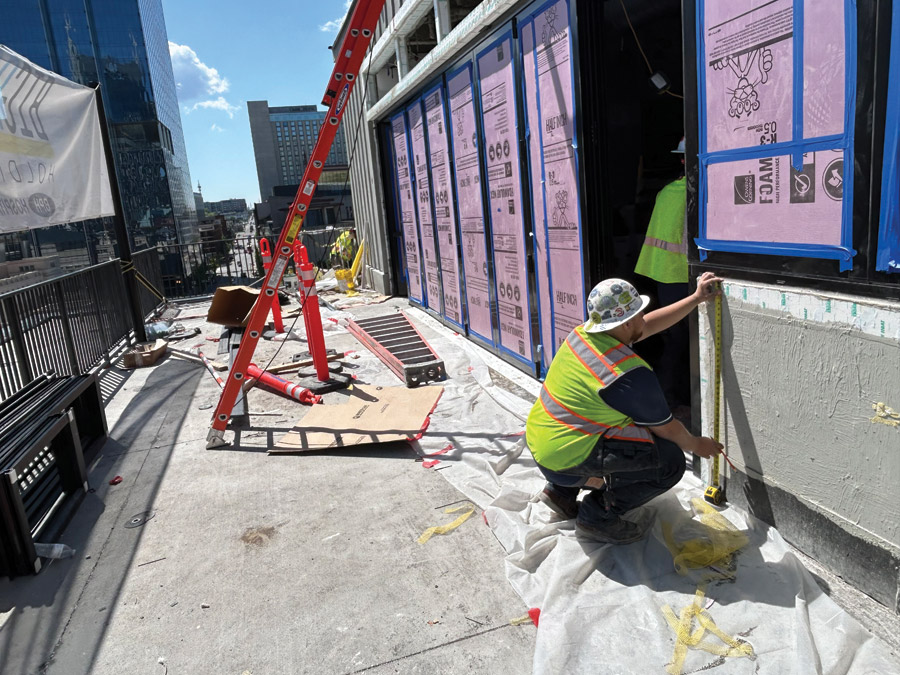
DPR and its mechanical subcontractors had to provide piping and electrical needs for a rooftop bar and performance venue near the balcony facing Fourth Avenue.
Photo by Jeff Yoders/ENR
As with any project in Lower Broadway, constant communication with the city was key to getting it done on time.
“We had to make sure we coordinated with the Department of Transportation, Metro Water and Metro Sewer, just keeping in constant communication with all of them and the neighbors so we weren’t blocking their doors,” Rowland says.
JBJ’s Nashville recently opened and hosted its first concert featuring a little band called Bon Jovi. n