How DPR Construction Pushes Innovation and Industry Change
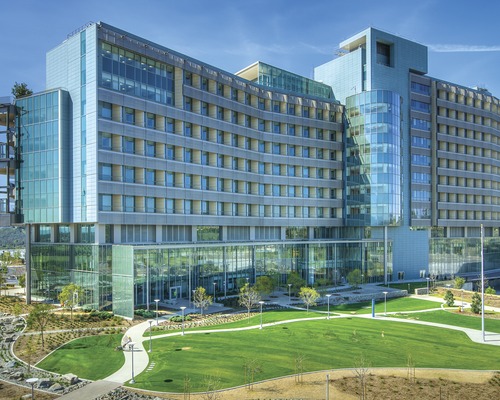

Lots of firms bandy the word "innovation" about but never actually introduce something new. One California-based general contractor, however, has hit the mark. What's more, DPR Construction, Redwood City, actually has an innovation program manager in charge of the effort.
The construction firm, which has 16 offices nationwide, has joined innovation and technology to create a defining movement: Its goal from inception is to rebuild the building industry.
Created in 1990 by three construction veterans—Doug Woods, Peter Nosler and Ron Davidowski, the DPRs of the firm's name—it has become a $2-billion business by utilizing its original core values of "integrity, enjoyment, uniqueness and ever forward." This fulfillment strategy was also honed at a meeting in 1992 with Jim Collins, a then up-and-coming management consultant and author of "Built to Last" and "Good to Great."
"Innovation has certainly been a part of DPR relative to how we set up our core values 20 years ago," says Eric Lamb, the company's executive vice president and one of its 11 original staff members. "Culturally, that is the kind of company we are."
Lamb adds that a lot of companies will have some "great ideas, but unless you have some people dedicated to the implementation part, there is no innovation."
Lamb says that seven years ago, the company started investing in a team built around building information modeling. He says that they set a goal to institutionalize BIM "in everything we do" by 2010. The technology team is led by Justin Schmidt, based in DPR's Washington, D.C., office with a staff that is now at 33, along with Atul Khanzode, director of construction technologies in Redwood City.
Lamb adds that in 2010, DPR set up the innovation group as part of its next mission. Headed by innovation program manager Jim Washburn, Newport Beach, Calif., the group of four people is tracking ideas across the company using a software tool called Spigit, which they use to vet ideas. Spigit, Pleasanton, Calif., is an idea management and social innovation software firm that serves mainly retail, health care, financial, technology, government, insurance, utilities and pharmaceutical companies.
Washburn says the goal of the group is to "speed up the rate of change" at DPR. He says they look at everything the firm does, especially best practices, and try to find new efficiencies. Washburn says the group recently found a way to speed up communication with California's notoriously complex Office of Statewide Health Planning and Development, which contractors have to deal with in every step on health care projects. Other efforts are aimed at developing strategies to work more effectively with owners and subcontractors, to find common ground with joint venture projects and to work more effectively with DPR's craft workers (carpenters and laborers, which number 1,400).
"Our goal is to find one thing to change on every job," Washburn says.
Lamb says a lot of Fortune 500 companies concentrate on innovation, but "you don't find a lot of construction companies doing it."
"A lot of innovation in this business comes from the owner saying, 'You will do this project this way,'" says Woods, whose official title is co-founder and president, though no DPR staffer has a title printed on their business cards.
"That results in a lot of companies getting into BIM or certain other aspects of technology," Woods says. "It's part of an ongoing process for us—constantly changing the way we do things, trying to get better at what we do and ultimately, hopefully, change the industry."
The other founders, Nosler and Davidowski, are board members but not active in day-to-day operations like Woods.
Manufacturing a Building
Woods says the firm now is looking at a future in which "building a building will be more of a manufacturing process."
"If you can build it on a computer, you can, in theory, build it in a factory and ship it in components, which is a faster, safer and cheaper way to do it," he says.
"We're not there, yet," he adds, but DPR is getting closer to doing prefabrication on a large scale.
Mike Ford, executive vice president, says that data center owners are looking at prefab assembly to drive down their costs. In recent years, DPR, which has concentrated mainly on health care, research laboratories, office complexes and high-tech factories, has dived head first into the data center segment, earning a partnership with Silicon Valley giant Facebook. DPR has built an energy-efficient data center in Prineville, Ore., for Facebook and is currently building a $121-million data center for the company in Lulea, Sweden and another in Forest City, N.C.
The four-year economic downturn has done little to slow DPR's growth. Revenue grew 23% from 2010 to 2011, and Woods says that "believing we're on the right track, being a highly disciplined business, will get us through any period of difficulty."
Michele Leiva, chief financial officer, says the firm did have some regions "feeling more economic pain" than others. Phoenix's revenues dipped in 2009, she says, but last year the firm invested in building a new net-zero-energy office complex to help keep employees focused.
As Woods puts it: "This is a tough business, and you need to be passionate and love what you're doing—the 'enjoyment' part of the core values. If you do, you'll thrive well here."
Furthering the reach of BIM in every aspect of a project, including visualization and clash detection, is another of DPR's primary aims, according to Lamb.
"Bringing more of what we're going to build into the process of design increases predictability, reduces the risk and adds more value to the customer," he says.
BIM is also contributing to DPR's goal of being a self-performing builder. Lamb says the firm is one of the largest drywall contractors in the U.S. (No. 9 nationally in volume, he says).
"We're employing BIM to increase our efficiency and our ability to do prefabrication in the trades that we self-perform," he says. "On about 10 projects so far, we are doing prefab concrete formwork, prefab metal drywall and metal stud drywall, and framing tables done off site and then moving it on site."
Lamb says DPR is also pushing hyper-visualization, which "really tries to marry BIM models with reality."
Augmented reality on jobsite iPads enables DPR staff to take a picture of rough-end plumbing and electrical sections, for example, and match it up to the model, doing clash detection in real time, he says.
This level of sophistication will also be valuable in predicting how buildings will perform down the line. Lamb says that DPR has one project now where the owner is requiring a five-year performance guarantee, which is being done regularly in Europe.
When they're not focused on construction innovation, DPR staffers, who work in an open-concept office in the Redwood City headquarters (no private offices, not even for Woods, Leiva or Lamb), are active in community outreach via the DPR Foundation. It was created in 2008 to help kids facing socio-economic challenges to reach their full potential.
Currently, the DPR Foundation supports 12 charities across the country with both financial and volunteer contributions. In 2011, the foundation contributed $590,000 to various organizations.
Recent charity work includes Turning Wheels for Kids, which provided 2,500 bikes to children last year, helping with Maryland Multicultural Youth Centers Riverdale chapter's six-week summer program and doing remodeling at the Roberts Family Development Center in Sacramento, Calif., which focuses on early childhood and family education.