Concrete Drill Jig Makes Work Less Painful
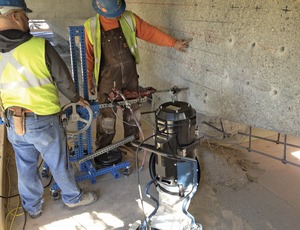
Having made overhead concrete drilling easier with an innovative, upside-down drill press, Dr. David Rempel and his University of California, San Francisco research team have turned their attention to the physical demands of drilling horizontally and at other angles.
Their efforts have yielded a new universal drilling jig that is designed for dowel and rod work and drilling large-diameter, ¾-in. to 1.5-in. holes for anchor placement in rock and concrete.
Rempel, who heads UCSF's ergonomics program, says the new jig addresses two interrelated construction issues.
"Some projects require anywhere from 10,000 to 40,000 holes using a 30- to 40-lb rock drill or a 30-lb hammer-drill," Rempel explains. "Not only do the vibrations and stress of holding the drill take a toll on the human body, the work itself becomes a real project bottleneck. We wanted to find a way to isolate workers from the weight and vibration load and make them more productive."
Designing the Jig
Using the overhead drill press as a starting point, Rempel and his team adapted the design to horizontal applications by increasing the jig's weight to a minimum of 50 lb. Along with providing a more solid connection to the ground, the heavier base can accommodate multiple drills that operate simultaneously with the bits spaced four to 14 in. apart.
Through trial and error, the team also crafted a spring-loaded saddle to direct the drill's energy to the tip of the tool, rather than back to the operator.
Introducing the spring loading also improved the bit's cutting speed and productivity, Rempel says, adding, "We also developed a system to quickly and easily change the drilling angle, providing full 180° capability."
The design also addresses the problem of dust. Because horizontal drilling generates more silica particulates than drilling at other angles, Rempel and his team experimented with various methods to capture dust. Working with drill manufacturer Hilti and Dust Control USA, the team developed a shroud-vacuum system that collects dust at the tip.
Research on the system's performance, published earlier this year in the Journal of Occupational and Environmental Hygiene, found that operator exposure to airborne silica was reduced by 94%, reaching a level well below the National Institute for Occupational Safety and Health's recommended exposure limit of 0.05 milligrams per cubic meter.
Real-World Drilling
Field tests with several Bay Area contractors at a variety of project locations have helped Rempel and his team fine-tune the design. As part of the renovation of the BART Transbay Tube, workers for Shimmick Construction Co. Inc., Oakland, Calif., used the drill jig to help anchor 4.5 miles of 6-in. conduit along curved concrete surfaces as much as 35° off vertical.
"We saved a lot of time because the drill jig is so easy and convenient to use," says Shimmick's electrical superintendent, Charles Colley. "The operators got good at changing bits out, moving the press to the right position and starting drilling."
Mark Kasel, safety director for RM Harris Co. Inc., Martinez, Calif., notes that the drill jig allows one operator to do the work of three or four, and it does so with more accuracy. "Rather than trying to come close to the right location, we can now be exact," Kasel says.
Rempel plans to add refinements based on contractor feedback, and he is looking for a manufacturing partner. The research team, funded by the Center for Construction Research and Training, will continue testing the jig with multiple drills and minimizing the setup requirements.
Kasel is already impressed with what the drill jig has to offer. "We were involved with some of the early tests when the drill vibrations broke the jigs," he explains. "It really showed just how much abuse the human body takes handling and operating these tools."