Unexpected Bay Bridge Crack Slightly Delays Reopening
An unexpected crack found in a section of the Oakland-San Francisco Bay Bridge delayed the planned Sept. 8 reopening only by about 90 minutes, rather than a full day, thanks to fast delivery from a fabricator and non-stop work by the contractor. Although the $140-million removal of a 3,200-ton double-deck section went as planned, California Dept. of Transportation inspection crews then reported a crack in an eyebar—a 2-in.-thick, chainlike steel piece—located on another section of the east span.
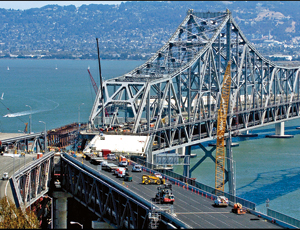
Over the Labor Day weekend, general contractor C.C. Myers, Rancho Cordova, Calif., cut out a 300-ft-long section of double-deck steel truss and rolled it out on special tracks—a feat quite similar to that done on a section connecting to Yueba Buena Island two years ago. Crews then rolled in a new 3,600-ton section that will serve as a detour until the new $6.3-billion Bay Bridge is completed. But as Caltrans engineers began inspecting the results, they found the crack. They determined that a steel brace would have to be manufactured to surround the cracked eyebar and be attached to another, lower pair of eyebars in order to redistribute tension load, says Caltrans spokesman Bart Ney.
By Saturday afternoon, Caltrans assembled C.C. Myers, San Francisco-based T.Y. Lin International, which is handling engineering and design of a new self-anchored suspension span, and other steel and hardware manufacturers to come up with a fix.
Carl Douglas, president of Coolidge, Ariz.-based Stinger Welding Co., a fabricator of expansion joints for bridges, says he got a call from project manager Bob Coupe of C.C. Myers on Saturday afternoon asking if Stinger could immediately provide saddle braces for the damaged eyebar. Douglas was on a fishing trip in a remote location in Wyoming. He says he was lucky to have brought his mobile phone on that afternoon outing.
“We have worked with Caltrans before, most recently on the I-580 MacArthur Maze collapse repair project in 2007, so they knew we could deliver at the last minute,” says Douglas. “I called some employees and got them to contact others. And within 30 minutes, we had a crew on their way to the plant.”
By Sunday morning, Stinger had cut and welded 15,000-lb and 17,000-lb saddle braces. They were placed on pallets and hauled to Sky Harbor International in Phoenix for a charter flight to Oakland Airport. Once the parts arrived at the airport, they were transferred onto a truck and hauled, with a police escort, to the bridge site, says Ney.
By that time, Caltrans had assembled a 10-man crew, which had started taking dimensions of the eyebars and making templates. Engineers found that spacers were needed in order to slip a rod past the eyebar adjacent to the cracked one. That prompted an initial decision to delay the bridge reopening to Wednesday.
But engineers then contacted the joint venture of American Bridge Inc., Coroapolis, Pa., and Fluor Enterprises, Aliso Viejo, Calif., which is building the new SAS span, to find out if it had the spacers at its fabrication plant. They did.
Ney says the work then proceeded in an “iron-man shift” of 70 straight hours. The new braces were installed and inspected, and the bridge reopened Tuesday morning. No cost estimate for the repair was available at ENR press time.