Competition Intensifies as Recession Deepens
Some economist have dubbed the current economic troubles “The Great Recession” to differentiate it from the Great Depression of the 1930s. While there are significant differences between the two economic calamities, there is one striking similarity: a sharp and prolonged decline in construction costs.
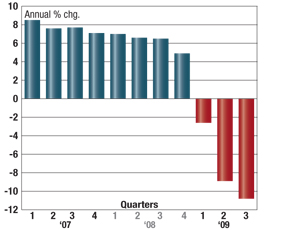


Materials prices for most products are down sharply from a year ago. However, the rate of decline is starting to slow, and some prices have rebounded from extremely low levels. In particular, stockpiling by China has given a bounce for copper, aluminum and other commodity prices, and lumber prices, after a five-year decline, appear to have finally bottomed out.
However, the damage has already been inflicted on most construction cost indexes. In September, ENR’s Building Cost Index fell 1.3% below 2008’s level after starting the year with an annual escalation rate of 5%. ENR’s Construction Cost Index this month was up just 0.3% for the year, following an annual gain of 3.3% as recently as last July.
While materials prices may be reaching the bottom of the market, fierce competition is continuing to drive costs even lower as contractors and suppliers cut margins in a desperate search for work. As a result, construction cost indexes that reflect the selling cost of construction are showing the most dramatic declines, including year-to-year decreases of 10.8% for the Turner building cost index, 5.9% for the Rider Levett Bucknall building cost index and 8.9% for PowerAdvocates index for a 550-MW combined-cycle powerplant.
“This is the largest drop in costs for a given year that we have seen in our index since the Great Depression of the 1930s,” says Karl Almstead, the Turner vice president responsible the company’s index. “Materials prices recently have been fairly level, and labor costs are pretty flat too. It is market conditions that are driving costs down.”
Falling costs come with its own set of problems, says Julian Anderson, principal with Rider Levett Bucknall. While the firm is carrying almost no cost escalation in its bids, it is factoring in a contingency for claims for change orders, which are on the rise because of unrealistic low bids, says Anderson.
“The last time I saw a really measurable and sustained decline in costs was 1976,” says Anderson. “This has been going on for nearly a whole year.” He believes competition could intensify even more as non-residential building contractors work off their backlog.
“Our company’s internal cost index indicates that construction costs have declined 2.9% since the beginning of the year, with certain markets approaching an 8% reduction,” says Greg Clark, vice president of estimating for Mortenson Construction, Minneapolis.
“Although we have been impacted by the continued increases in labor costs, these increases are far outweighed by the reductions in the cost of fabricated materials, substantial discounting of project margins and final bid numbers from subcontractors,” says Clark. He expects this trend to “continue for some time, at least until vendors and subcontractors are able to bring their work volumes back to a level that allows them to manage a more profitable business,” he adds.
Steel prices have declined on weakened demand in September, with prices for hot-rolled steel falling about 10% from a 10-month high in August of about $620 per ton, analysts say. Hot-rolled steel was down to $520 per ton, and rebar decreased to $502 per ton by mid-September. It was a correction that followed the summer’s 8% climb since June after prices bottomed out at $430.
But even with the latest price recoil dampening expectations of a recovery, capacity utilization remains at 60% across the industry, up from a low of 45% in the spring, according to Washington, D.C.-based Steel Manufacturers Association. “Utilization is still up, but whether it is sustainable or not we don’t know,” says Tom Danjczek, SMA president. “Still, it’s down from the 80% of capacity utilization of a year ago.”
Analysts say the summer spike was in part the result of government stimulus boosts in the U.S. and Asia, and the downward pressure on steel is being felt worldwide. Going forward, pricing “remains uncertain as the economy at this point appears to be in slow recovery mode,” says Keith Busse, CEO of Fort Wayne, Ind.-based structural-steel manufacturer Steel Dynamics Inc.