Exclusive Interview With Owner: Panama Canal Project Won't Be Held Hostage By Contractor Shutdown
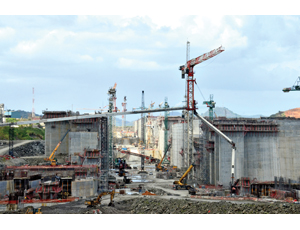
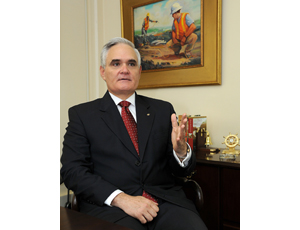
For the past six weeks the Panama Canal Authority (ACP) has been negotiating a reported $1.6 billion in cost overruns with the contractor building the locks for the waterway's Third Lane Expansion. On Feb. 5, the contractor consortium, Grupo Unidos Por el Canal (GUPC), stopped work on the project, citing a breakdown in negotiations that threatens the original mid-2015 completion date of the $5.2 billion project. GUPC consists of Spanish construction firm Sacyr Vallehermoso S.A., Italy’s Impregilo S.p.A., Jan De Nul n.v. of The Netherlands and Panama's Constructora Urbana S.A.
ACP Administrator Jorge Luis Quijano, an industrial engineer who has headed the expansion since it began, spoke at length to ENR about the project status and its current options. He reiterated the intention to complete the project by its planned finishing date next year “with or without the assistance of the contractor.”
ENR: What is the current status of the project?
Quijano: We are at a stage right now where [contractors] have stopped work. They say they have not stopped work, but there is no work happening at all. On Feb. 5, there was maybe 1% of work being done by a few subcontractors, but a day later, work is completely at a standstill. [GUPC is] saying they haven't formally notified us that they have stopped work. For me, that has really zero value since it is a de facto work stoppage. We know for a fact they have told workers to go home. They have told subcontractors to stop work. We even have subcontractors ask us if they are going to be paid or not.
We have left a little window of opportunity for continuing to exchange views with the contractor to see if an amicable resolution is possible. However, the more time that passes, the less likely that is to happen. We sent [the contractor group] a four-page letter on Feb. 5 asking them to substantiate their actions because, to us, this is a hostile act and it needs to be resolved immediately. They have already wasted enough time. They began slowing down in November and they continued to keep slowing it down until now they've brought it to a total halt yesterday.
ENR: Is this action sufficient grounds to break the contract and move forward without GUPC?
Quijano: The contract is very clear that if work is stopped or significantly reduced—or any part of the work is substantially reduced—that is sufficient grounds to take them off of the job. We feel very strongly about their actions, and if they decide not to settle this and not return to work, they leave us very little option but to default them.
We are looking at the next few days that will be critical in our decisionmaking process. As time passes, we have less and less of a chance to have a negotiated solution. We are not closing the door but they are leaving us with very little room to maneuver. But we are not going to be held hostage for their work stoppage; we are going to take action. I'd say we are coming to the end of the road and we not talking about weeks to get this taken care of, let's put it that way.
ENR: How long has this situation been developing?
Quijano: This is not the first time we have been at this juncture with the contractor. This is the first time [GUPC has] taken a hostile position by stopping the work but in December 2012, [the contractor] was having similar cash flow issues. They came to us and requested relief by asking for a moratorium on paying back their lines of credit. They wanted some relief so they could last until the return on some of the claims they had made for cost overruns. We agreed and they did not pay back any of their lines of credit in 2013. They took the whole year and didn't win a single claim they put in to the dispute arbitration board.
They had whole year of non-repayment, which amounts to about $300 million to us, to continue work and have the time to substantiate the claims they felt they could win. The moratorium ended in December 2013 and they have to start repaying—and they have to do so very quickly at the rate of about $39 million a month.
According to the contract, they have to continue to work while these claims are being evaluated. This is costing them more than what they expected and what they want to do is make us pay for all the expenses. This is not a cost-plus project.
What we have put on the table is a further deferral of the repayment program, extending the moratorium significantly so they can continue the work. But even with that, they still have not agreed to continue the work. They did not accept that offer and, instead, asked for a moratorium to 2020.
ENR: Several times you have mentioned a 'Plan B' to complete the job without GUPC; what does that entail?
Quijano: Plan A is to continue working with the contractor and finish the job according to the contract. Plan B is to go ahead with the work without this contractor. We don't see any other alternative. It is either one or the other. Some have suggested that we don't have the construction know-how to handle it, but we're not going to construct it.
What remains to be done? About 30% of the work. What remains to be done in concrete? About 20%. All the designs for the project have been completed. Those designs are ours. The amount of work that remains is backfill and about 900,000 cubic meters of concrete (out of the 4.4 million cubic meters total). Outside of that, it is only the electro-mechanical work. And all of the electro-mechanical work was going to be done with sub-contractors. Even GUPC had planned to do that.
Our Plan B is very simple; work with all the subcontractors who were [already] going to perform the electro-mechanical work. We need a small general contractor on the Pacific side. We need a small general contractor on the Atlantic side. These will be needed to continue to provide the general services and construction management activities. But it is not the same size of a project we had in 2009. Taking this job from here onward is not the same as starting from scratch.
ENR: Fabricating new gates for the locks would take longer than a year. What arrangements are there to procure the gates that have already been made?
Quijano: The new locks have 16 gates in total. We already have four gates here along with all the electromechanical elements for them. Four gates have been completed in Italy, and are awaiting transportation. Another four gates are going to be ready in a month's time. And the last four gates will be ready by June at the very latest.
We don't expect Cimolai [the subcontractor in Italy] to give us the gates they have already fabricated for free. Unlike GUPC, Cimolai has done an outstanding job by continuing to work. [The firm is] very professional and we have a very good relationship with [it]. I feel we will continue our working relationship with [Cimolai].
There is very little use for these gates other than in the new locks. They cannot be sold for any other project, and if they are scrapped, it will bring in maybe one-tenth of what they are actually worth.
If the [GUPC] plan is to hold onto those gates and force us to look elsewhere to fabricate [new ones] from scratch, that to me is extortion. And it affects far more than just the Panama Canal. The canal is not being done just for Panama, it is being built for the world. The United States is the number one user. China is number two, and Latin America is the third biggest user. There is a lot of international interest to see this project is completed.
ENR: GUPC won the locks job with a bid of $3.12 billion, more than $1 billion under the next lowest bid submitted by the consortium of Bechtel and Taisei Mitsubishi. Is there reason to believe this was underbid?
Quijano: At the time we fully analyzed this and we fully believed the amount bid was an adequate amount. We had hired consultants who drew up a range of what the bids were expected to be. And we set an estimated range of $3.1 billion and $3.6 billion, which would depend on how each bidder saw the risk.
Many people compare GUPC's bid to Bechtel's bid but forget this was a design-build project; you bid on the basis of your design and the amount of risk you feel comfortable taking. But GUPC is now asking for $1.6 billion, which is far more than the difference in those two bids.
ENR: There were concerns when ACP chose to join both sets of locks into a single contract due to the size and complexity of the job. Was that a factor in the issues you are facing now?
Quijano: Because it was design-build we thought it was much better to have both [sets of locks] done by one general contractor than by two. The design had to be the same for both and by having one contractor do it, you could actually cut down on the time.
We felt [GUPC] could handle it if [it] had done the work with diligence from the very beginning, but, I regret to say, [the contractors] did not. We started to notice that about a year into the program. We started to get the impression they would not be able to complete the job in the allocated time we had allotted.