Every fall, during low-water time on the Mississippi River, a crew of about 300 men and women turns out to resume one of the longest-running and most important construction projects of the U.S. Army Corps of Engineers—the placement of articulated concrete mattresses along the levees to prevent scour and protect communities.
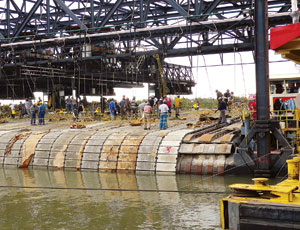
The Corps was given the armor-the-levees mission in 1885, although its armoring work predates that. Now, the “construction phase” is almost done, with about 1,000 miles of levee, from Cairo, Ill., to Head of Passes, at the mouth of the river, protected.
“We are the first arm of defense,” says Donald Rawson, chief of the channel stabilization section of the New Orleans District of the Corps. “If we get scouring, we immediately do something to attack that. We’ve always treated the Mississippi River and tributaries levees like cathedrals; sacred territories, because we have so much to lose if we do have a failure.”
Because most natural banks of the lower Mississippi are composed of alluvial deposits the banks erode more easily than the riverbed. Without revetment, the river would meander. However, there are also many areas that don’t require revetment and there are intentional gaps in the armoring to allow for spillage from deltas and water diversions. The revetment program satisfies the Corps’ missions of flood control, navigation and environmental stewardship, Rawson says.
Many techniques have been tried. Fish-pole cane and willow mats were used from 1878 to 1883. Evidence of those can still be seen on high-resolution surveys of the bottom of the river. Framed willow mats were tried beginning in 1888, fascine willow in 1893, monolithic concrete mattresses in 1914, lap-slab, or overlapping concrete slabs between 1926 and 1931, asphalt in 1932 and even roll-type concrete in 1944. The Corps settled on articulated concrete mats, or ACM in 1948. Rawson says it had been experimenting with them since 1915.
The basic mattress “square” covers 100 sq ft. It is 4 ft x 25 ft x 3 in. thick. Each square consists of 20 14-in. x by 4-ft concrete slabs spaced 1 in. apart and held together by stainless steel or copper-coated steel wire.
During placement, or “mat sinking” the squares are linked into a continuous, flexible mat up to 156 ft wide and extending as far as 700 ft into the river. “Mats are typically placed at the 20-year average of low water to 100 ft past where the bank flattens out,” Rawson says.
The joints allow for about 8% open surface area, which facilitates placement in swift, deep water and relieves hydrostatic pressure. Today’s ACMs are cast with a grooved surface, which provides habitat for algae, fish and crustaceans.
Every year, four Corps districts of the Mississippi Valley Division—St. Louis, Memphis, Vicksburg and New Orleans—share in the mat-sinking mission. Work begins in August and travels south to end in New Orleans around Thanksgiving.
At the heart of the process is the mat boat, or mat-sinking unit, whose 140-ft x 75-ft deck is fitted with 9,880 rollers for material handling. It was designed by the Corps for this operation, says Joel Brown, chief of the mat-sinking unit. “Originally, there were two units—one in Memphis and one in Vicksburg—but they were consolidated in 1994,” he says. It can place 135 squares a day.
The process begins when a mooring barge, set perpendicular to shore and held in place by cables from two spar barges, guides the mat sinking unit to the bank, parallel to shore. “We always work against the current,” says James Siffert, senior project engineer in the Corps’ Lafayette area office.
Supply barges raft up on the river side of the unit and four gantry cranes move 16-block sections of mat from them to the mat boat’s rollers. There, workers tie the sections together with hand or pneumatic tying tools until the mat covers the deck. At the same time they are also interwoven with steel cable fed from spools in the ship below. “This is a very mechanized process,” Siffert says. “It’s a true assembly line.”
When placement is ready to start, workers on the land side of the unit toss cables to workers on shore, who attach them to cables from anchor plates buried in the bank. “Each anchor holds 10,000 pounds per square inch,” Siffert says. The mat sinking unit has mechanical “fingers” which can extend up to 20 ft for extra reach if the water is too shallow to get close to shore. Placement starts as the unit begins to pull away and the anchored cables start dragging the mat into the water. The work pace grows furious as the crew on the supply side quickly ties on more squares to feed the mat rolling into the river off the other side.
When the last bit of the mat goes into the water, the crew continues to feed out cable until the mat is on the bottom. Then the cables are cut and the operation moves 130 ft upstream to begin again.
With so much of the river now reveted, the bulk of mat sinking now is maintenance, Rawson says. Construction in the New Orleans district is 95% complete. The mat-sinking mission there has dwindled from placement of 550,909 squares in 1974 to 80,232 squares in 2008—and 73% of that was for maintenance, Rawson says.
As the revetment mission winds down the Corps has reduced its mat-casting facilities from five to three. Production at St. Francisville and Delta, La., and Richardson’s Landing, just north of Memphis, Tenn., has slowed from year-round to a few months each year, Siffert says. The sinking operation, which used to go on around the clock, is now performed in 10-hour shifts on 12 consecutive-day work periods.
There also may be more of a future for the system. Since ACM has proved such a good product for Mississippi River bank stabilization, “We are looking at it for other uses, like coastal restoration,” Rawson says.