Powerplants
Viewpoint: Modernizing Protective Relays: How One Utility Made the Switch
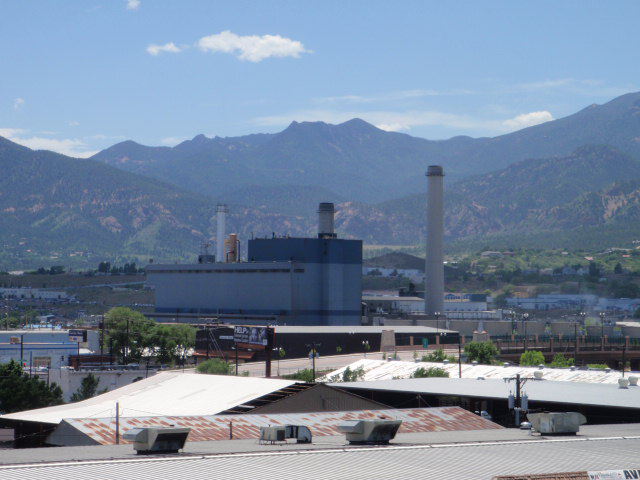
A May 2014 fire at the Martin Drake Power Plant damaged all three coal-fired units, disabling the entire 254 MW facility.
Photo courtesy of Colorado Springs Utilities
A May 2014 fire knocked out the Martin Drake Power Plant of Colorado Springs Utilities (CSU). The fire damaged all three coal-fired units, quickly disabling the entire 254 MW facility. The plant provided a third of the utility’s production, and to avoid power shortages and higher rates associated with buying power on the open market or by building a greenfield plant, CSU decided to repair the three units as quickly as possible.
The nerve center of the plant’s electrical system, the relay room, was severely damaged. This room contained the relays responsible for protecting critical plant equipment, including the main generators. The existing relays used older electromechanical technology, so the restoration presented an opportunity to modernize the system with microprocessor-based numerical devices, bringing benefits of the digital age into the power plant.
It’s a question many owners with older relays ponder on a continuous basis. The replacements would require engineering and redocumenting the plant’s systems. The staff would have to be trained on the new technology.
Although the relays and associated switch gear represented only about 10% of the project cost, there was a business analysis involved. Old relays are not being manufactured today, so used or older equipment would need to be found. Also, insurance coverage would pay for a restoration to the original condition, but not for new equipment.
CSU had planned to install new relays and had enough of the new ones to restart Unit 6, but they were eight years old and had to be sent back to the manufacturer for retesting. After considering the alternatives, the utility chose safety, improved plant control and efficiency and lower maintenance over a small additional cost and went with the new relays.
For CSU, speed was of the essence, as added time would result in higher costs. Relays aren’t bolted on, however. It would take careful engineering and documentation to realize their benefits.
Numerical Relays
Numerical relays are digital devices with microprocessors that give them many more capabilities than electromechanical relays. These include:
- Protection. Numerical relays offer protection previously cumbersome or not available with electromechanical relays. When configured properly, they can detect problems more sensitively, which can limit the size and severity of power outages.
- Self-diagnostics. Modern relays can perform self-tests to alert personnel of potential problems. This simplifies maintenance efforts and reduces costs. Instead of requiring a week of testing every three years, numerical relays may take only three days, every six years.
- Flexibility. Features such as multiple setting groups and programmable control logic facilitate functionality previously difficult or impossible with electromechanical relays.
- System visibility. A wealth of information is now accessible. Operators can view real-time system data, use data over time to detect trends and patterns and use oscillography captured during an event to aid troubleshooting. Plus, more sophisticated alarming schemes are possible.
- Simplicity. Many different elements protect the power system. Previously, each element necessitates its own electromechanical relay. This could result in a dozen or more relays required to protect just one generator. Now, many functions can be put in one relay which dramatically cuts down on the wiring and panel space required. This can result in fewer points of failure and reduced cost.
- Network and automation. The ability to network relays opens a world of possibilities, from access to system-wide information to self-healing capability. This said, some utilities make the decision to leave the protective relays stand-alone or “isolated from communication” to avoid cyber security concerns.
Replacement Work
While these benefits make numerical relays seem like an obvious winner, if not done carefully, the replacements can create more problems than they solve. Drake was especially challenging because of the urgency of the restoration. Many steps needed to take place in a short amount of time. The team had to quickly perform field investigation to verify numerous engineering drawings, coordinate installation activities, commission, test and finally, train the staff.
New relays must integrate with the remaining systems, so collecting and organizing existing information is critical. The consulting engineer begins gathering information by listening to the plant operator. It is important to devise a plan that fits the user’s needs, rather than using a standard design. It is impossible to get a complete picture remotely, so the engineering team traveled to Drake.
When on site, the consultant had the opportunity to interview key plant personnel. They work in the plant every day and therefore provide information not available on any drawing. This boiler-house lore is a critical part of completing the documentation puzzle.
For effective operations, safety, maintenance and troubleshooting, the operators need complete and accurate documents that all fit together in the correct order. That starts with one-lines that lead to schematics, followed by wiring diagrams and panel layouts. If you start developing wiring diagrams before the protection philosophy has been agreed upon on the one-lines, you risk rework and errors down the road.
Once drawing development is well underway, the engineer configures the numerical relays for the specific application by developing relay settings. CSU could have done the settings with internal staff, as it did with a small 20 MW unit in another plant, but in this case, management used a consulting engineer.
One possible approach is to replicate the previous electromechanical settings; however, this rarely works in practice. First, you don’t know what was done in the past or if it was done correctly; second, settings don’t always transfer directly; and third, protection elements aren’t always one-for-one replacements. Therefore, the engineer developed a fresh set of calculations to document the approach and philosophies. Well-documented setting calculations are critical in establishing NERC compliance. Plus, if you ever have another event, under-documented protection designs can present insurance-coverage issues.
Close communication with the consulting engineer is critical, and the deliverable review process can be a major facilitator. When calculations and drawings are made available for client review, the ensuing dialogue can prevent many problems during construction and operation. Some consultants consider design calculations proprietary, but that approach is not conducive to efficient collaboration with the client.
Potential Pitfalls
Installing numerical relays can present not necessarily obvious problems. For example, electromechanical relays were set up to complement each other in their operating methodology. The design inherently provides a certain level of redundancy. However, the “everything in one box” numerical relay breaks the complementary relationship and requires a more redundant approach. The team mitigated this issue at Drake by using two redundant SEL-300G relays to protect each generator.
Additionally, some elements in an existing system may not have been functional and the act of making changes or testing the new system can produce unexpected results. Many times, these issues can be mitigated with careful commissioning practices.
Installation can be done in different ways. A shop can fabricate a preassembled panel, which can be interconnected with minimal effort in the field. Or you can build the whole thing in the field. Costs and speed of installation need to be considered when looking at the options.
When installation is complete, thorough testing and commissioning takes place. It can also be useful for the design team to participate in the commissioning process. This can help ensure the system is coming together as planned, but it can also provide engineers with valuable lessons and feedback. For example, participating in system tests can highlight areas where additional isolation points or redundant equipment are useful. In addition, it is imperative that documentation be updated to reflect as-installed conditions to facilitate future modifications.
Soliciting operator input to the design process is extremely important because operators live with the system after the design team leaves. Their preferences on items such as operator interfaces can be incorporated into the design so the new system resembles the critical aspects of the previous system. That said, the modernizing project will undoubtedly lead to some unfamiliar ways of doing things. In these cases, it’s essential that the staff be trained; you don’t just design a system and walk away.
CSU personnel, with support from the consultants, worked long nights and weekends to implement the replacements. The first Unit, 6, restarted nine weeks later and Unit 7 was operating in 16 weeks, bringing the plant up to 80% of capacity, ahead of schedule. Unit 5 was back in commission in 10 months after the fire, also ahead of schedule.
Joe Thornam is a senior electrical engineer with Stanley Consultants Inc. in Denver. Donald Loftis Jr. is principal engineer for Colorado Springs Utilities.