Energy Viewpoint
Streamlining Processes Ensures Safer Plant Designs
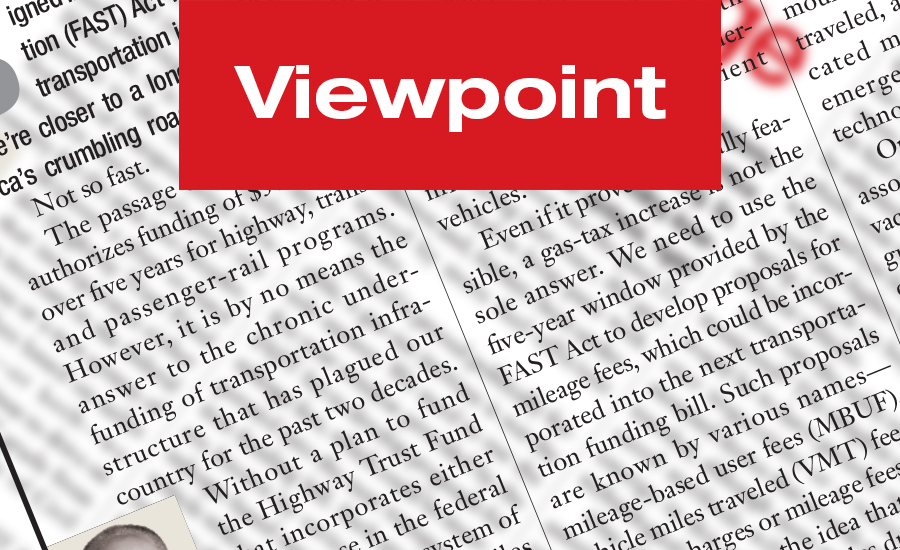
Schedule adherence during plant safety design is critical for the oil & gas, chemical and petrochemical industries. But an engineering, procurement and construction contractor can get in its own way if it clings to traditional, manual practices and internal, basic tools. Plant-design software must be integrated to improve workflows and anticipate and reduce bottlenecks while maintaining stringent safety standards. Advanced, integrated safety tools are essential to achieve that result.
An Integrated Solution Saves Time and Streamlines Processes
A manual workflow that requires laborious data transfer between tools is time-consuming and prone to introducing errors in the design. One global EPC organization recently reported it regularly uses more than 20,000 individual spreadsheets. An integrated solution helps to remove the time barriers and make more effective use of time.
Many companies have adopted advanced engineering software solutions to rigorously improve Front End Engineering Design (FEED) and perform revalidation studies to find capital savings and improve process safety and reliability. The best process-safety software tools offer multiple options to complete pressure-relief-analysis projects. Companies can use these tools to easily conduct safety studies, including pressure-safety valve sizing, depressurization, flare system design and rating and dynamic analysis for start-up, shutdown, emergencies and compressor surge with the option to use simulation data from integrated engineering application environments.
Integrating safety analysis solutions within engineering software suites lets users leverage the rigorous thermodynamic engine when completing pressure-relief analysis projects. They can quickly add and size relief valves early in the design process while incorporating industry standards, such as API 520, 521 and 2000, into calculations. Additionally, this pressure relief analysis can be continued to discharge those sized relief devices by automatically importing sized pressure safety valve results into flare analysis software to streamline pressure relief analysis. Leveraging dynamic models in analysis helps avoid the risk of overly conservative and potentially more expensive designs by offering a more rigorous look at the system.
Integrated software solutions improve relief load calculations for both FEED and revalidation projects. Ultimately, with the right process safety software tools, engineers gain enormous benefits, such as:
- Saving engineering time by up to 50%
- Reducing mistakes and manual transfer to ensure data accuracy
- An increased ability to integrate results into flare system models
- An increased scope of relief load calculations
- Avoiding unnecessary capital investment through under designs or overdesigns
- Avoiding the consequence of inaccurate pressure-safety-valve sizing
- Upholding quality safety standards
- The ability to model multiple scenarios
- Automated regulatory reports and documentation for compliance
- Tools that support engineering knowledge and ease of use
Minimizing Costs with Cutting-Edge Software
Cutting-edge software also can increase accuracy to save both time and money. BLOWDOWN software, for example, allows detailed analysis and protection of key process equipment to be performed quickly and effectively, including rigorous and rapid depressurization studies.
With the right tools, performing the most accurate minimum design metal temperature (MDMT) analysis saves costs while ensuring materials of construction used in the system will not fracture. To avoid unnecessary expense and preclude the risk of over-conservative specifications, organizations must determine the certainty of values. For a comprehensive end-to-end depressurization solution, robust blowdown simulation software enables oil and gas companies to help every process engineering project, ranging from newly built facilities to a revamp project on an existing process. It enables the design engineer to design or rate blowdown systems that ultimately assure proper safety and are economically feasible.
Better modeling of temperatures, pressures and maximum flow rates during the blowdown process will reduce overdesigns and save enormous engineering costs for engineers. Accurately depressurizing the system minimizes the risk of harm to the process equipment, product and personnel. It is also crucial to ensure that this analysis determines not only safe materials of construction, but also provides the correct orifice sizes that depressure systems in accordance with leading industry standards, such as API and NORSOK for fire cases.
Advanced simulation tools enable engineers to create concurrent designs with simulation, minimizing reworks, and allows the organization to reuse and refine safety analysis at each stage of the design life cycle. In addition, they have complete control to push assets to the limit to maximize throughput, troubleshoot efficiently with confidence and more accuracy while conducting safety analysis.
A robust blowdown analysis software was recently integrated with an advanced process-simulation tool that enables engineers to determine orifice sizes and pinpoint areas of low-temperature concern, providing less conservative MDMT values. In some cases, this can lead to three to four times cost savings resulting from less expensive materials of construction. This particular solution has been used in over 400 oil and gas and chemical projects to model depressurization. The software identifies specific locations in a system where temperatures can decline dramatically during depressurization. With these enhanced safety features, engineers can serve workflows and safety projects easily, as well as perform accurate safety analysis and leverage data from powerful simulators, all within a single integrated engineering simulation environment.
Managing Future Risks
As plant complexity continues to increase, organizations will need to adopt advanced integrated safety engineering software to identify and manage risk more effectively. With the right software in place, businesses will improve safety performance across their operations, increase accuracy to save both time and money and ultimately improve overall operational conditions.
Ron Beck is the energy industry marketing director, AspenTech.