ENR California’s Specialty Firm of the Year
Creativity Reaches New Heights at KHS&S
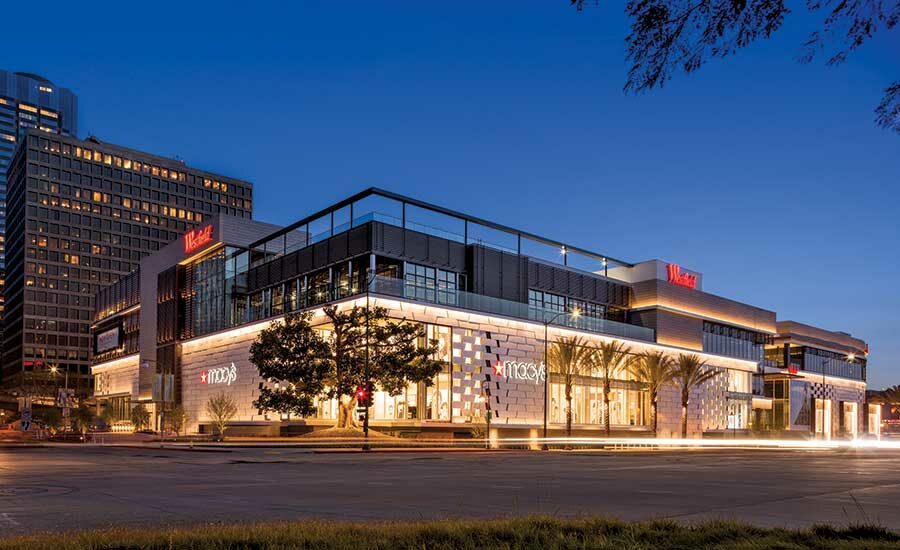
KHS&S met the demands of a fast-track retail project with many design changes in the $1-billion Westfield Century City Mall in Los Angeles.
PHOTO COURTESY OF KHS&S

On the Claremont McKenna College project, the ceiling plane rose and fell over a large area, with elevation changes up to 6 ft.
PHOTO COURTESY OF KHS&S

KHS&S completed all exteriors at Silicon Valley data center CoreSite SV7 in Santa Clara, Calif.
PHOTO COURTESY OF KHS&S

Master craftspeople used paint, plaster and finishing techniques to create intricate ‘aged’ building facades inspired by Harry Potter movies and books.
PHOTO COURTESY OF KHS&S




From a wizard’s fantastical world to a giant, ring-shaped corporate campus, specialty contractor KHS&S brings creativity and innovation to its most complicated assignments.
Led by its employee-owned West Coast division, the Tampa, Fla.-based company is the second-largest wall and ceiling contractor in the U.S., with a majority of its revenue coming from work performed in California. Its West Coast revenue has grown in the past two years by more than 40% and shows no signs of slowing down.
“Business is strong and fun again, especially in California.”
– Dave Suder, President and CEO, KHS&S
“Business is strong and fun again, especially in California,” says Dave Suder, KHS&S president and CEO. “The markets are in a higher demand than we have seen for years.”
The company, which has 650 employees in California, keeps a strong presence in the state, with offices in Anaheim, Concord and San Diego. Its West Coast crews are currently working on 25 major projects and have completed approximately $150 million in work this year. This accounts for about 65% of the company’s West Coast business. Casinos and theme parks are hot markets for KHS&S, which specializes in unique interiors and exteriors, water features and themed environments. “We could not be more excited for the momentum of these markets to showcase our specialty contractor skill set,” Suder says.
Nowhere is this skill more on display than on the Wizarding World of Harry Potter attraction at Universal Studios Hollywood, which was completed last year. KHS&S’ master craftspeople helped build the castle and village from Harry Potter movies and books and created intricate “aged” facades using paint, plaster and an exterior insulation and finish system. They installed more than 30,000 elements consisting of real and faux wood, fiber-reinforced plastic, glass fiber-reinforced concrete, millwork and windows.
“This was a pretty specialized project,” says Chris Ritter, lead project manager for PCL Construction, which served as general contractor. “Not many companies around can perform this type of work on such a large scope.”
The Harry Potter attraction in Hollywood was the third one built, with earlier Harry Potter attractions in Japan and Orlando, Fla. The repetition allowed owners to zero in on improvements for the newest version, such as more realistic stonework, Ritter says.
In previous versions, the village portion’s exterior stonework was “kind of very rectangle square” while the owners preferred more organic and random shapes, Ritter says. To achieve the effect, KHS&S workers created mock-ups and then hand carved tens of thousands of stones out of stucco.
The company’s latest ambitious assignment is a bit more modern. KHS&S is working on the $5-billion Apple Campus Project 2, which opened to employees in April and is currently wrapping up construction. Larger than the Pentagon, the Foster + Partners-designed campus covers 176 acres and can house up to 13,000 employees in one central, four-story, ring-shaped building of approximately 2.8 million sq ft. The building is clad entirely in the world’s largest panels of curved glass.
Another signature project is the $1-billion Westfield Century City Mall in Los Angeles, which was completed this fall. Working on an estimated $45-million contract, KHS&S performed exterior framing and insulation, sheathing, waterproofing, theming and exterior finish on the two-level, 1.3-million-sq-ft outdoor shopping mall.
KHS&S’ team met the demands of a fast-track retail project with many design changes, says Darren Johnson, vice president of construction for Westfield, the project’s owner and builder. “Their senior management team was very involved in the project and always available to address our concerns as the client.”
Johnson says KHS&S showed its strength when quality control and fabrication issues arose with several sole-source suppliers of facade materials specified by the designers.
“While many contractors will often take a back-row seat to resolving second-tier vendor issues, especially with respect to sole-source materials, KHS&S stepped up and took a front-row seat to work through the issues with these vendors and suppliers,” Johnson says.
Construction of the Westfield mall benefited from the firm’s Lean building culture, Suder adds. Faced with a limited staging area, tight deadlines and complex exterior theming and framing assemblies, the KHS&S team “scheduled, coordinated and showcased many of the company’s latest Lean innovations—all while a portion of the mall remained open to shoppers with construction fully underway,” he says.
KHS&S uses digital models and building information modeling to plan and design work. “BIM has been a critical part of our business for some time,” says Ronan Frias, director of construction design. “With the complexity of wall coordination, BIM is essential during the planning and design phases.” Frias says the company leverages BIM to identify prefabrication opportunities.
Frias says BIM helps the firm incorporate 3D models of manufactured architectural elements as well. “The BIM process assists us in the dimensional control of these manufactured pieces,” he says. “Because the elements are manufactured to precise measurements, coordination and integration of them is crucial.”