Commentary
Three Industries That Are Helping Drive Construction Companies Forward
Firms working in the energy sector can learn from other projects

Onsite inspections could be replaced by virtual remote inspections.
Photo courtesy of Fluor.
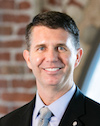
It’s an exciting time to be a contractor in the North American energy industry. With the amount of shale feedstock, global clients are green lighting new projects. The number of petrochemical projects under consideration in the U.S. Gulf Coast is a prime example.
This doesn’t mean, however, that clients aren’t still extremely disciplined in their capital spending. Fears of unforeseen cost overruns and schedule delays that have hampered previous projects create uncertainty with new investments. With this uncertainty comes more pressure to deliver execution solutions that provide project delivery certainty.
There is, however, a silver lining to this pressure. It gives the industry an opportunity to implement innovative, cost-effective ideas clients have been asking for. We as an industry must embrace this challenge. Companies can develop their own unique solutions, leveraging proven approaches from other industries that have faced similar challenges in the past.
Here are three industries that offer examples for engineering and construction companies in the energy sector:
Manufacturing. Over the past two decades, productivity in manufacturing has nearly doubled, while construction productivity has remained flat according to McKinsey & Company. One manufacturing best practice often linked to construction is creating manufacturing’s controlled environment through modularization.
While significant modularization can provide execution delivery certainty, those modularization opportunities may not be feasible for some projects due to location or other constraints. It is still possible, however, to create a controlled, assembly-style environment and obtain the safety and productivity benefits.
Facilities at or near jobsites can specialize in assembling materials into fully developed modules or pre-assembled units that can be transferred to their final destination onsite. This approach opens up more work fronts at or near project sites, improves productivity by moving work to a controlled environment and improves safety by reducing the amount of work at height.
Military. While the industry continues to recruit and train more skilled craft workers, a shortage of highly skilled, “master” craft workers remains in the U.S., especially in the Gulf Coast where there are a large number of energy projects being planned. This can create challenges resulting in low craft productivity and schedule delays.
Just as the military has its own elite units, such as the Navy SEALs, construction companies can create their own elite units to take on the critical scopes of a project.
In one example, Fluor’s elite team consists of a 70-person group of specialty welders and pipefitters that are proactively deployed to construction sites to provide their services.
Automotive. Automotive repair shops and insurance companies are now diagnosing car issues and claims virtually through phones. The construction industry can take a similar approach by bringing people virtually to jobsites and suppliers.
Through remote visual inspections, companies can virtually perform material and equipment inspections, testing and surveillance. These inspections can support a range of events, from performing an inspection at a supplier’s shop to troubleshooting an issue on a refinery revamp.
Through this secure virtual presence, the right execution resources can instantly access the site in real-time, improving quality and schedule deliver and reducing travel costs.
These are just a few examples where we can take proven best practices from other industries and use them to improve capital project delivery. With this type of collaborative, open mindset, the future is bright for our industry.
Jason Kraynek is vice president, business development and strategy for Fluor’s Energy & Chemicals work in the Americas. For more information on Fluor, visit www.Fluor.com.