Tomorrow's Equipment Operators

It can be hard to find operators to work solar power installations in remote locations, prompting some contractors to explore autonomous earthmoving equipment.
Photo courtesy Built Robotics
With a tight labor market and construction still booming in many regions of the country, one category of worker that has felt stretched thin has been equipment operators. Generational retirements and a reshuffling of the general workforce known colloquially as the “Great Resignation” has many contractors eager to fill positions, and others are looking at unconventional training regimens and emerging automation solutions to help meet their schedules and budgets.
But while construction goes through its boom and bust cycles, many contractors are using the current situation to examine how the role of the equipment operator is changing as new technologies upend traditional construction processes.
By the numbers, labor costs are up and skilled workers are scarce. In 2021, average base salary raises for construction staff jumped to 4.2%, from an average of 3.6% in 2020, according to data from compensation consultant Personnel Administration Services. 62% of contractors reported high levels of difficulty finding skilled workers to the U.S. Chamber of Commerce in the fourth quarter of 2021. And there’s no sign of demand for equipment operators dropping off any time soon. The U.S. Dept. of Labor’s Bureau of Labor Statistics estimates there was a total of just over 457,000 construction equipment operator jobs in 2020, and that figure is expected to climb past 482,000 by 2030.
There are leading indicators for how many operators are coming up, and the number of people pursuing the required certifications to run equipment like cranes offers a barometer of the current labor market. “The guys who run the big rigs, those are definitely retiring,” says Thom Sicklesteel, CEO of CCO, formerly the NCCCO, or National Commission for the Certification of Crane Operators.
CCO administers tests for OSHA-required certifications of operators of cranes and other equipment. In 2018, OSHA began requiring all crane operators to be certified. That led to an upswing in people seeking certification through bodies such as CCO, and demand has been steady ever since, says Sicklesteel.
“We see about 400 [crane] operators a month leave the industry through retirement,” say Sicklesteel. “But we’re seeing about 1,000 operators joining the industry on a per-month basis.” Most of the newer operators are starting out on smaller equipment, slowly building up the skills to run the big tower and luffing jib cranes. “The average age of operators is declining, and that’s a good trend.” Sicklesteel adds that CCO has also seen a surprising rise in operators picking up multiple certifications for different types of cranes, perhaps reflecting a desire to keep their options open when looking for work in a favorable market.

Virtual reality-based training modules for equipment such as aerial lifts allow operators to test skills in dangerous settings like entrapment scenarios.
Image courtesy Serious Labs
Virtual Training Takes Hold
Sometimes the issue isn’t a shortage of workers looking to become equipment operators so much as the throughput of getting them all trained up. Edmonton, Alberta-based Serious Labs has offered virtual reality training for mobile elevated work platforms (MEWPs) for several years. Some of the most common pieces of equipment found on jobsites, boom lifts and scissor lifts are deceptively easy to run, and inexperienced operators can find themselves in highly unsafe conditions after only a few small errors.
“What we are seeing in the industry often is training on MEWPs happens very quickly—get them in and get them out,” says Wade Carson, senior director of product at Serious Labs. Rather than get workers up to speed running a lift in a quick session tooling around a parking lot, for instance, Serious Labs has developed virtual reality-based training simulations that place headset-wearing operators in various scenarios that they may encounter on a construction jobsite.
“You can get a good sense of [an operator’s] capabilities before they even set foot on a site”
Wade Carson, Senior Director of Product, Serious Labs
The VR system puts users on a simulated work platform, with the same physical controls they would find in a typical boom or scissor lift. In addition to requiring them to perform tasks correctly, the VR headset also captures where the user is looking, and logs reaction times. “[Our system] identifies poor behavior—a lack of situational awareness or a lack of efficient movement,” says Carson. “It provides trainers with that knowledge so they can focus their efforts on filling in the gaps rather than a ‘shotgun blast’ approach to training.” The company has seen a steady uptick in demand for its training in recent years, and Carson says 44% of its customers are trade unions.
Serious Labs has advanced its VR to the point where this past June one of its scenarios was approved as ANSI- and ISO-compliant. Operators who pass a custom VR assessment scenario with at least an 80% proficiency now can meet MEWP 3b ANSI A92.24 and ISO 18878:13 specified boom lift competencies. These operators can be rated as competent without having to set foot in an actual boom lift.
“Our ANSI training scenario is very telling in terms of how capable an individual is,” says Carson. Putting users in a simulated version of dangerous situations provokes different reactions than real-life practice. “You will never see a training facility where a new operator is operating a MEWP below a surface or in a confined or entrapment space,” he points out. “This tells us if they are spatially aware, if they know the limitations of the equipment. You can get good sense of their capabilities before they even set foot on a site.”
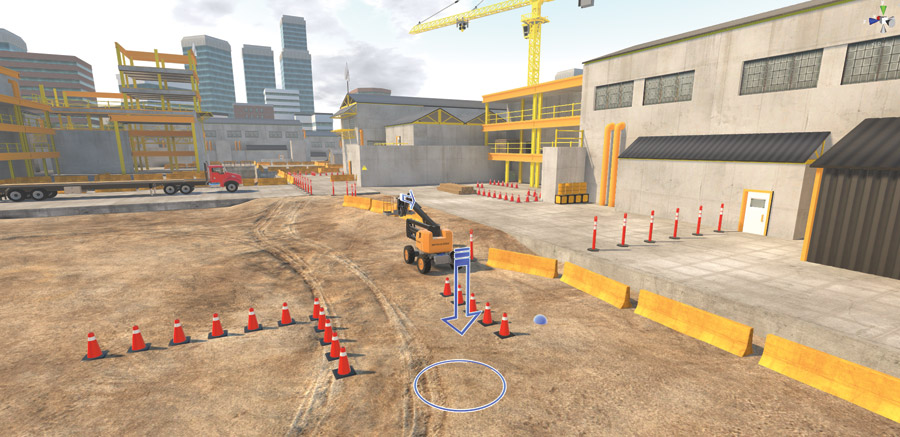
Serious Labs’ VR training for MEWPs recently achieved ANSI and ISO compliance, allowing users to demonstrate competency without having to operate a real boom lift.
Image courtesy Serious Labs
Integrating Automation
Contractors have sought to use robotics and automation to help control the sometimes chaotic construction process and to perform repetitive, tedious tasks that tie up skilled workers. But bringing in autonomous equipment and smarter tools into construction processes requires collaboration to be successful.
“We don’t refer to contractors as customers, we refer to them as partners, because this is very much a two-way street,” says Gaurav Kikani, vice president of strategy at Built Robotics. “We acknowledge, pretty humbly, that we don’t have all the answers, but what we can do is bring unique perspectives to the table and the ability to very quickly build useful technologies. But then we deploy and get a lot of feedback from our partners on how this technology can be improved to accelerate the industry into the future.”
Built’s autonomous system for large excavators works with a geofence and artificial intelligence-driven decision-making to create both safe operation and productive results. The system is fitted onto regular Caterpillar and Komatsu hydraulic excavators, turning the controls over to an onboard computer that is programmed to perform standardized and repetitive excavation tasks as loaded prior to operation. On solar projects, Built excavators were able to achieve 93% uptime at a productivity rate of 191 linear ft per hour, a 45% productivity increase over a single operator toiling alone for hours digging trenches. The robotic excavators are overseen by a human operator monitoring their progress from an onsite trailer.
Kikani is working with contractor Bechtel in its role as EPC on solar energy projects across the southern U.S. First deployed on a Bechtel site in 2021, the contractor and technology provider worked together to refine the performance for site conditions found in the South, such as optimizing excavator buckets to be able to handle the “Texas gumbo” clay soil.
“We’re working with robotics in ways to augment the personnel that we already have,” explains Keith Churchill, Bechtel’s chief innovation officer. “We want to leverage the expertise of whatever discipline or craft that robotics affects and provide ways for them to work better and faster,” he says. “[If we] take away the menial tasks that are repetitive and really don’t require a huge amount of expertise [we can] put our subject-matter experts where they’re most needed on the most challenging, technically demanding jobs.”
In many equipment categories, the road to automation starts with better situational awareness for human operators. “We’re probably about 10 to 15 years away from fully autonomous cranes,” says Asaf Yarkoni, business development manager at Israel-based crane tech firm UltraWis. “But with technology [right now] the operator doesn’t have to think all by themselves.”
“We want to leverage the expertise of whatever discipline or craft that robotics affects. ”
Keith Churchill, Chief Innovation Officer, Bechtel
UltraWis’ current product offering adds an array of sensors and cameras to a tower crane. In addition to IMUs and load cells, the sensor package includes LiDAR scanners that map out the jobsite as the crane swings around. This all provides additional views and situational awareness to the operator via a 23-in. touchscreen in the cab. The interface provides a real-time overlay of the operator’s view, identifying obstacles and advising on optimized lift cycles.
The next step for UltraWis is to bring the operator down to the ground, operating the crane from a trailer with a stitched-together immersive view of what is happening around their crane. Yarkoni says when this remote operation setup is combined with GPS tracking of construction materials and autonomous obstacle avoidance, the industry may need to stop thinking in terms of one operator per crane. “We can get to two cranes with one operator, or two cranes with only one signalperson. It’s a more systematic approach,” he says.
“The beauty of the remote operator concept is that not only are you operating the piece of equipment, you also understand the positioning behind it, you understand the ground control, you understand the setup of the equipment and, ultimately, you understand the productivity you’re getting throughout the day,” says Churchill. “So you don’t have to wonder if somebody thinks you’re being productive or not.”

Built’s Exosystem robotic upgrade, seen here on a Komatsu excavator, allows autonomous operation and completion of repetitive tasks such as trench digging.
Photo courtesy Built Robotics
Lending a Helping Hand
Daniel Stone, director of business transformation at Southfield, Mich.-based contractor Barton Malow, recalls the reaction from workers when the contractor first brought Construction Robotics’ Material Unit Lift Enhancer to one of its sites. The MULE is a pneumatically driven armature originally designed to help build masonry walls by offering a less physically intensive way to pick up CMUs. Once on site, the two craftworkers set to be trained on using the MULE did not try to hide their initial skepticism.
“They literally rolled their eyes,” Stone says. “But by the end of the day one of them went off and did something else because he wasn’t needed. And the first guy who ended up doing all the work said he loved it and never wanted to work without one.”
The growth of the solar energy market and the need to rapidly build out vast solar farms is driving new approaches to equipment. Barton Malow has delivered several solar projects in the Midwest over the last few years, including DTE Energy’s LaPeer Solar Array, located north of Detroit. It’s in these kinds of projects it has found its use case for the MULE. “We are working with Construction Robotics to build a rig that is going to allow us to place solar panels held by the MULE using silicone suction cups,” Stone says.
A project like the LaPeer installation calls for over 180,000 individual solar panels, each weighing at least 70 lb. By using a lift-assist device like the MULE, Stone believes the contractor’s laborers will be able to install the panels faster and without the repetitive, labor-intensive manual lifting of the current method.
“If instead of having two people lift a 70-lb solar panel, if you can have one person lift it with no weight, you’ve saved somebody a day and you’ve also taken all of the wear and tear off the first person,” Stone says.
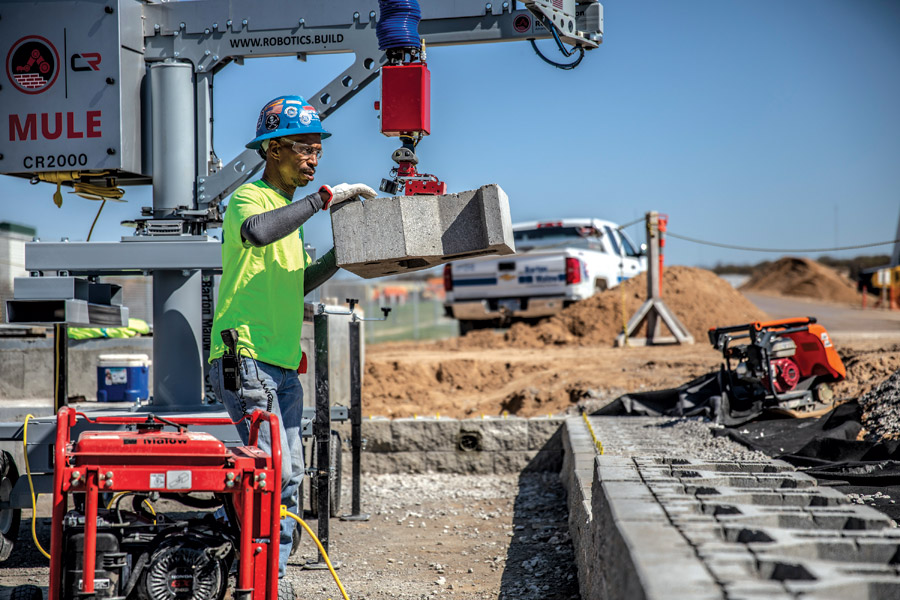
Barton Malow has used MULEs on more than a dozen projects to quickly place and build CME walls. The contractor is expanding its use into placement of solar panels on utility-scale projects.
Photo courtesy of Barton Malow
Barton Malow has used MULEs as well as Construction Robotics’ Semi-Automated Mason (SAM) bricklaying robot on projects throughout Illinois, Indiana, Michigan and Ohio. Both Stone and Bechtel’s Churchill stressed to ENR that they are looking for more than just how to fit automation into existing processes. They want to unlock the efficiencies of robotics to create better processes for both their workforces and clients. For SAMs and MULEs, Barton Malow has found a compelling use case for them in soldier piles and lagging in bricklaying work. They’ve produced perfectly straight walls with mortar running in a straight line every time, says Stone.
Stone and Churchill both tell ENR that they are also working with their suppliers to change how their materials are manufactured and delivered to their work sites to better accommodate their newly developed processes.
On masonry wall projects using MULEs, Barton Malow is asking for 32-in. block rather than the traditional 16-in., 38-lb block that has been the standard for CMUs. That standard originally came about simply because that’s how much one person can comfortably lift, Stone says. “We have a very likely project that’s going to go in Detroit to 32-in. block and those are 80 lb [each],” he says.
Contractors interviewed were all preparing for a future where skilled tradespeople will continue to retire at a steady clip, and the younger generation of workers might not keep up for a 1:1 replacement. Creating new jobs where skilled labor is more about managing semi-automated machines is a way to hedge against that potential shortfall.
“You are either going to have trouble finding the right people, or you’re going to pay a significant premium to find those people,” Churchill notes. “As we see costs of everything else in the industry are starting to grow, the cost of labor is going to continue to rise. It’s not just operators, but multiple crafts where it’s just becoming more and more difficult to find the right personnel with the right expertise.”