Midwest Best Projects
Best Project, Excellence in Safety, and Award of Merit, Manufacturing: Case Farms Automated Freezer Expansion

Photo by Greg Folkins
Case Farms Processing Plant
Winesburg, Ohio
EXCELLENCE IN SAFETY and Award of Merit, Manufacturing
Submitted By: Primus Builders Inc.
Owner: Case Farms
Lead Designer: Primus Design Service LLC; Primus Builders Inc.
Structural Engineer: Primus Design Services Inc.
Civil Engineer: Bohler
Working under a tight deadline, design-build-automate contractor Primus Builders significantly expanded operations at the Winesburg, Ohio, plant for poultry processor Case Farms and tallied a perfect safety record. The project was delivered in two simultaneous phases. Phase 1 included a new engine room, a 36,000-sq-ft chicken processing facility and processing utility areas. Phase 2 provided a 138,000-sq-ft cold storage warehouse, an automated carton freezing solution, a palletizing area, a wet cooler dock, a loading dock and supporting office.
“What sticks out to me is how we’re able to help them provide a better end product for their customers,” says Ryan Jennings, solutions project executive with Primus. “Instead of shipping off their product to another facility, they’re able to do the freezing and storage at their own facility to create better profits for themselves.”
Meeting schedule demands was imperative on the one-year project, which completed in May 2021. Case Farms had already grown the hatchery for the chickens that were to be processed at this facility, so the building had to be ready to receive them. In addition, the client requested that the processing area be ready four weeks ahead of the originally completion date.

Photos by Greg Folkins
The site was located on a former strip mine. Mine spoils were discovered during sitework, prompting crews to dig out the spoils and rehabilitate the ground to make it safe for construction.
The expansion required utilities that exceeded availability in the small town of Winesburg. For example, the facility requires 1.5 million gallons of water a day to operate. The existing water tower could provide only 200,000 gallons. To ensure enough water access, Primus built two wells and installed four pumps. It also built two 300-gallon tanks. Booster pumps were reengineered to provide adequate water pressure.
To meet its electricity needs, Primus worked with a power co-op to pull electricity from two substations before Winesburg was able to build a new substation dedicated to the building.
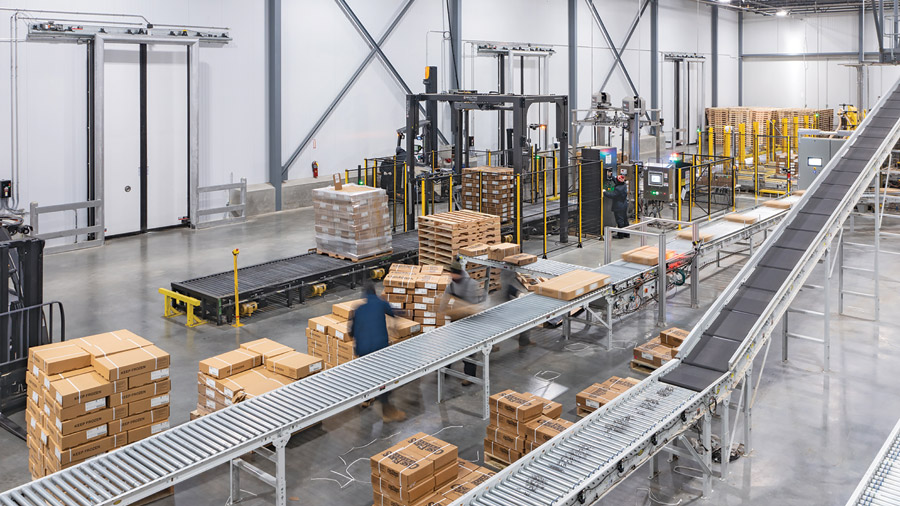
Photos by Greg Folkins
The project tallied a perfect safety record with no OSHA recordable incidents and no lost-time accidents over 213,982 worker-hours. Primus developed a site specific safety plan that reflected the area’s unique topography, weather, utilities, overhead clearance and traffic patterns. The project superintendent walked the site daily and instructed subcontractors on safety improvements. Safety stand-downs were organized when special safety conditions were introduced. For example, prior to ammonia being loaded into the facility, the site was shut down to allow for specific training for the event.
The team used building information modeling to create a visual representation of the site and helped personnel anticipate working conditions before construction began. During installation of the automation equipment, the team was able to identify pinch points and determine safety zones to protect workers and equipment.
Prior to performing work, all subcontractors were required to complete a project-specific safety course at the jobsite and furnish material safety data sheets. Primus also worked with a third-party consultant to provide safety audits of ongoing construction activities.