Digging Deeper | Transportation
Bridge Fix Bolsters Lifeline as Sandy Repairs Conclude
Metropolitan Transportation Agency’s $49-million subway link and communications upgrade in Queens, N.Y., has benefited from a mild winter

The Sandy Repairs Rockaway Line Wrap-Up includes rare vibration monitoring methods that have only been performed a few other times throughout the country.
Photo courtesy of Navillus Contracting
A mild 2023 winter has helped work advance on a $49-million effort to repair a subway bridge and communications network that link the Rockaways section of Queens to the rest of New York City—a fitting contrast to the brutal Superstorm Sandy surges more than a decade ago that heavily damaged the Jamaica Bay crossing and transportation infrastructure across the entire region.
While the fixed North Channel Bridge and its track survived crushing waters from the epic 2012 storm, key parts of the structure’s support—including the fender system, piles, navigational lighting and cables—took direct hits that now require replacement or repair. In the mostly remote 5.8-mile section where New York City Transit’s A line crosses from Howard Beach Station to the Hammels Wye facility on Rockaway Peninsula, that kind of work primarily takes place on an undulating surface—the waterway itself.

An early morning Rockaways-bound subway train crosses the bridge as the team strives to minimize service disruption.
Photo courtesy of Navillus Contracting
“All the work is done from a barge with a [crawler] crane on it,” says Rashmi Shah, assistant vice president for infrastructure in the Sandy business unit at the Metropolitan Transportation Authority’s construction and development group. “It’s a huge effort. We’re replacing 350 piles.”
Staging almost exclusively from barges for demolition and installation has posed significant logistical challenges compared with land-based work, particularly on repairs to the fender system that protects the bridge concrete piers and support structure from marine vessel impact, says Kate Clancy, project manager at Navillus, general contractor on the effort. Demolition work began when the project broke ground last summer, she says, with the project slated for completion in July 2024, although it is likely to finish at year-end.
“We’ve already removed the existing fenders, timber round piles and pile clusters, timber walers and lighting,” she says.
Among the key tasks is coordination of traffic in the tight North Channel, moving out debris-filled barges while bringing in not only their unfilled backups but also other vessels flowing in with new materials, such as piles, machinery and equipment, Clancy says.
The team also has been installing the new fender system in stages, already having put in all 24-in. hollow piles and now focusing on eight larger dolphin piles this month, she says. The entire fender system will be replaced by June with new piles, walers and walkways.
The entire effort—with HDR as engineering consultant, Big Apple Group as vibration monitoring consultant and TDP Associates as electrical and communications subcontractor—is emblematic of the wider Sandy repair efforts, says Robert Laga, vice president and deputy business lead for infrastructure in MTA’s construction and development unit.
“We’re repairing a lot of the damage on this bridge,” he says. “While we’re not doing any track work, we are installing piles, monitoring the bridge structure as well as tracks, and trying to limit disruptions to the riding public.”
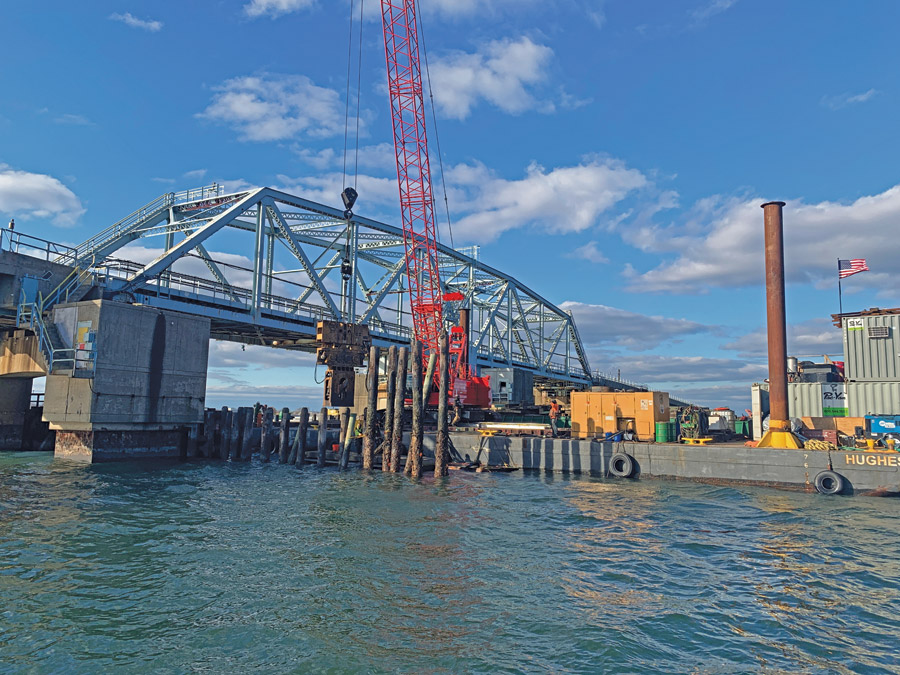
Crews remove timber piles from the bridge’s old fender system using a crawler crane operating from a barge.
Photo courtesy of Navillus Contracting
Massive Sandy Repairs
The North Channel Bridge project is part of the closing wave of Sandy repair jobs in MTA capital plans. “We’re pretty much wrapping up the Sandy program,” Laga says. “We’re close to 95%.”
He says the overall program—lumped into groups of street level openings, subway entrances, yards, underground facilities and above-grade fortification—has been sweeping. The tally of projects finished or set for completion includes repairs, flood protection and resilience-oriented “hardening” measures for four railyards, nine subway tubes and Staten Island’s St. George Terminal, as well as installation of thousands of mechanical gates that can keep street water from coastal flooding out of underground facilities.
“This has been a very successful effort by everybody involved,” Laga says. “We hope we never have to deploy these things, but if we need to they’re ready for use.”
Design work on repairs and hardening for two more rail storage yards and other individual repair and resilience projects is on deck for the closing stretch, with the last batch of a half dozen contracts set for bids this year, Shah says. Those include the Westchester yard in the Bronx and Corona yard in Queens, she says.
The Sandy repair program has also had a wider impact on how MTA manages its construction projects, with lessons learned from the storm damage—and ways to mitigate climate change fallout and extreme weather events—now built in, Laga says.
“We now incorporate design guidelines that we use on every job to make sure that any work going out has hardening measures embedded in it,” he says. “So for a new bus depot, where is it located, can there be a tidal surge and flooding events, what do we need to make it harder now?”

The team works on installation of fiber-reinforced polymer piles near the bridge, which later will involve adding new walers as well.
Photo courtesy of Navillus Contracting
Mudbank Protection
Despite Sandy projects often focusing on replacement and repair, the work is far more complex than simple swap-outs, with frequent need for measures to bolster resilience, support existing structures and upgrade for design innovations or improved technology. The North Channel Bridge was a prime example, with the team upgrading the old fender system to minimize how newly installed piles would impact the mud bed and the existing structure.
“This has been a very successful effort by everybody involved. We hope we never have to deploy these things, but if we need to, they’re ready for use.”
—Robert Laga, Vice President and Deputy Business Lead for Infrastructure, MTA Construction and Development Unit
Navillus partnered with pile manufacturer Creative Composites Group in suggesting an alternate design, which HDR and MTA evaluated. It uses fewer, larger piles compared to the previous layout, with far less mudbank disturbance, Clancy says. The new design has 68 larger hollow fiber-reinforced polymer seawall piles instead of the previous 440 solid timber piles or pile clusters. That includes 60 FRP piles, each with a diameter of 24 in., replacing 434 13-in.-dia solid piles, along with four 36-in.-dia and four 48-in.-dia FRP dolphin piles that are standing in for eight previous 13-in.-dia solid pile clusters, she says.
“The difference in material is important,” says Priyank Patel, project manager at Navillus. “When you’re installing a solid pile, you need a heavier hammer and there’s more vibration. A hollow pile does not disturb the mud bed as much.”
The largest pile is 94 ft long and extends 73 ft into the ground, Patel says. Installing fewer piles also has benefitted the construction effort, given the uncertainty of working from barges on the water, he adds.

Crews operate a crawler crane from a work barge that has a vibratory hammer attachment to drive the 24-in. piles into the mud bed.
Photo courtesy of Navillus Contracting
Land and Sea
The project’s scope spans both the bridge and landside infrastructure for the subway, MTA’s Shah says.
“The bridge and cable and signal work—it’s all combined in one package,” she says. “From Hammels to Howard Beach is a long distance. It’s a big project.”
The work includes replacement of navigation and tide gauge lights, signal switch heaters, terminal test blocks and more than 70,000 linear ft of cable and conduit.
“With specifications provided, the degree of accuracy with traditional [technology] to monitor for displacements would not be possible.”
—Alex Sabetta, Northeast Regional Supervising Engineer, Big Apple Group
“When Sandy came, we had so much damage to all of these copper and fiber cables and the signal systems across the subway system because of the saltwater,” Shah says.
The train system communications equipment work is particularly significant, with installation of fiber optic and copper cable and conduit from the Howard Beach station to the Hammels Wye facility and to the Rockaway Park-Beach 116th Station on the peninsula, Clancy says. The cables run parallel to the tracks above ground but also cross them at seven locations, including four that require excavation for installing pipes and innerducts. A portion also involves marine cables underwater.
The cable installation work required extensive coordination with the MTA for access to the tracks, with much of the work taking place on scheduled service outage weekends, Patel says. The crews, led by electricians, used work trains and installed the cable through manholes and on communications poles.
The warm winter in the region has been a big help in the effort to date, Laga says. “Except for a couple, we’ve been able to work almost every weekend at the bay,” he says. “You make hay when the sun is out.”

The project is using innovative wireless movement monitoring technology to ensure that demolition and construction don’t damage the track or bridge structure.
Photo courtesy of the Big Apple Group
Advanced Monitoring
Another key element of the project has been the extensive effort to protect the existing bridge and ensure that demolition, fender system repairs, pile-driving and other work does not damage the structure. The vibration monitoring system that Big Apple Group is using on the project involves new technology only applied on a handful of other projects in the U.S.
The wireless remote condition monitoring technology from Senceive that the team is using tracks any rotation, deflection, displacement or deformation of tracks, piers or the bridge structure. It’s an improvement over traditional monitoring technology and surveying techniques, says Alex Sabetta, northeast regional supervising engineer at Big Apple Group.
“With the specifications provided … the degree of accuracy with traditional [automated node] systems to monitor for displacements would not be possible,” he says.
The consultant had Senceive help on the design of a localized network of sensors to monitor the structure, which Navillus, HDR and the MTA all reviewed and approved, Sabetta says.
The system uses two types of wireless nodes attached to track beds and piers on the bridge, all powered by long-life batteries and hooked up to two data relay stations, says Dan Miller, head of business development for the Americas at Senceive.
“If there is data that shows there is movement beyond the design criteria, work would be stopped and mitigation efforts would be performed,” he says.
The system uses the MTA’s own allowable movement thresholds, with measurements down to “sub-millimeters,” Miller says.
“Normally when you have trains running over a bridge, it’s going to be a bit stricter because you have to also align the allowable movement of cross-level or twist,” he says. “It’s providing the project a lot more data, which really helps the contractor and project team coordinate any potential construction activity impact on the structure—much more fine-tuned than it normally would be just getting one reading a day.”