Final Pontoons Nearly in Place for Floating Bridge in Seattle
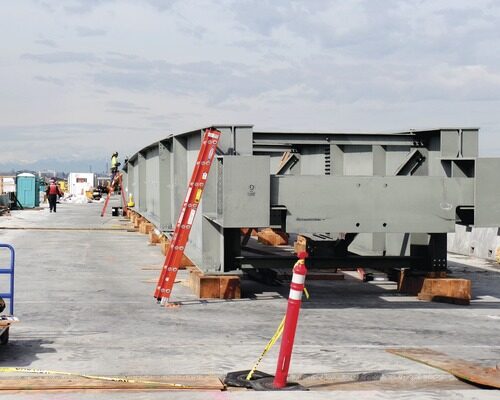
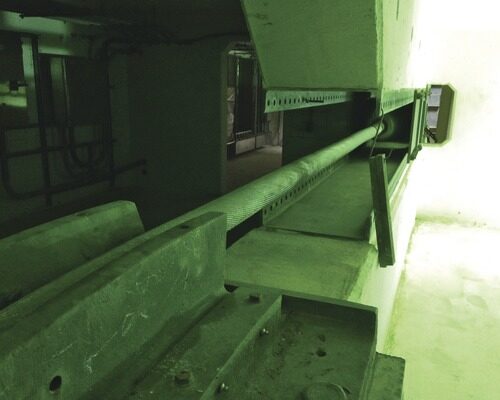
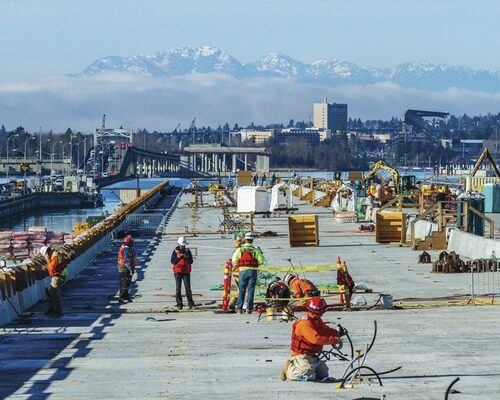



The 58 cables for the new bridge feature 3-1/8-in.-dia strands that run to three different types of anchors. Along with the gravity anchors, crews use drilled shaft anchors where the ground is hard, but not deep, and fluke anchors in the really soft soil buried in the lake. All anchors are intended to remain in the lake forever, designed to give maintenance crews the ability to change cables via a pin-connection release point.
Lake Washington's topography requires cable anchors to secure a floating bridge. The water is 200 ft deep atop another soup-like 200 ft of soft silt and lake sediment. To build a non-floating bridge would require massive caissons, a series of costly towers and huge approaches that would extend inland for miles, a prohibitively expensive scenario that would be out of character with the largely residential area.
Bridging the bridge
The last big push for the pontoons that sit 6 ft above the water level comes with the joining of pontoons B, C and D, the westernmost section, near the current bridge and then swinging the assemblage into place. By joining the three pontoons at once instead of each after the other, WSDOT was able to keep boating lanes open longer. Geyer says building B, C and D—1,080 ft long altogether—was like doing a bridge in itself.
Work on the bridge started with the W cross-pontoon on the east side. Then the contractor assembled staging areas and worked "right down the line, letting all activities line up linearly."
"It allowed everything to flow in progress across the lake," Geyer says. "To avoid an island scenario, we rafted pontoons on the north side of the bridge."
The vast majority of the bridge contains 776 precast deck panels match cast at 6,500 psi in Kenmore and floated to the bridge. The B, C, D raft, as it is called, rises toward the west approach, requiring the use of cross beams, columns, precast concrete girders and bridge decking. In all, the bridge contains 772 columns and 331 girders.
Working on water created some difficult logistics. For example, longitudinal joints require 80 high-strength bolts each 20 ft long and 3 and ½ in. in diameter to fit together. "Nobody thought we would be able to line those things up," Becher says. "We are lining them up at different angle points. Then we take those bolts and tension up to 750 kips, 80 times." At 1,760 bolts, there is a lot of "opportunity for success or failure at each joint," especially with the bridge bobbing up like a cork. Crews had trouble with only four, even getting those to work in the end.
Greg Meadows, floating bridge and landings deputy construction manager, says wind loading adds a new on-lake element for building a bridge. "You are a creating a big sail and how do you deal with that during construction?" he asks. Based on sea state and winds, new criteria added to the construction phase. The added complexities of surveying a moving structure when everything is built to a 16th of an inch requires new thinking—vertical over plumb—and specialized surveying tools.
Geyer says the surveying system was a key logistical hurdle to overcome, as were the scheduling challenges associated with moving equipment around a lake. "Every day you are getting curveballs," he says. "You just have to stay on your toes."