ENR's 2023 Top 400 Contractors: Uncertainty Looms Over Market
May 24, 2023
ENR's 2023 Top 400 Contractors: Uncertainty Looms Over Market
May 24, 2023Sundt Construction is working on Phase 1 of the Willamette Water Supply Program in Oregon. Scope of work includes a $400-million water treatment plant.
Photo Courtesy of Sundt Construction
As economic uncertainty swirls around the Capitol Hill debt limit negotiations, some ENR Top 400 contractors are worried about reaching the limit of their ability to keep projects profitable. Through years of pandemic-induced cost volatility and workforce shortages, firms have kept their revenue and backlogs strong by strategies that include value engineering.
But can they also value engineer economic confidence?
With the Federal Reserve looking to fight inflation and cool the economy by raising interest rates, economists seem to overwhelmingly agree that an economic slowdown is on the horizon. But ENR Top 400-listed general contractors say there is uncertainty looming over how the construction industry should prepare for when such a slowdown will hit and what business sectors will be most affected.
Related Links:
ENR 2023 Top 400 Contractor Rankings
2023 Top 400 Contractors | Full PDF
(Subscription Required)
America's First Two Utiilty Scale Offshore Wind Projects Ramp Up Construction
Construction industry markets are not reacting to economic developments all in the same way, explains John Cannito, president and CEO of PENTA Building Group, ranked No. 128. “Some market segments are flush with optimism and are looking to capitalize on pent-up consumer demand. Others are more cautious, with concern about a potential recession,” he says, explaining that the “two extremes” are driving owners to make decisions based on a false sense of security in experiences that do not transcend all markets.
In effect, some owners are “delaying projects that should be going forward in soft markets” and others have “unrealistic budget expectations in strong markets,” says Cannito. Managing project expectations, “advising clients responsibly and making sound business plan decisions will be important to succeeding in 2023,” he says.
Uncertainty Coming to a Head
Managing cost volatility continues to be a top priority for firms, says Rycon Construction Inc. CEO John Sabatos, as owners weigh whether to pause projects or cancel them altogether, “which will in turn cause a slowdown in construction starts,” he explains.
“Normal historical cost increases from year to year have been manageable with good value engineering processes,” Sabatos says, but “higher increases will not be able to be recovered by simply making designs more efficient.” Delays have caused the “necessity to perform work on an overtime basis which has increased the costs and negatively impacted bottom lines,” he adds.
Ranked No. 1 for the third consecutive year is Turner Corp., with more than $16.25 billion in reported revenue. Bechtel is ranked No. 2. Although many Top 400 listed firms have consecutively reported increased revenue and record backlogs since the start of the COVID-19 pandemic, firms sense a change of pace is inevitable as owners grow weary over volatile project costs. While workforce shortages, cost inflation and supply chain delays continue, there is also uncertainty among firms about how resources can further be reconfigured to provide solutions.
Steven H. Sommer, Lendlease executive general manager and president of East Coast construction, says the No. 53-ranked company has seen lead times nearly double for materials. “And we continue to experience significant shifts in pricing,” he says.
With business interests in development and construction, the company has a “360-degree view of challenges and the costs and delays they present,” he says.
Lendlease says it is also better equipped to offer solutions by meeting with owners and design teams early on for key decision-making. According to Sommer, the strategy has helped push owners and the design team “to make decisions quickly so that components and materials can be pre-purchased and secured months ahead of installation.”
In addition to supply chain issues impacting the ability of projects to move forward, Sommer says uncertainty over economic conditions also add to project risks. “While we have a robust pipeline of future work in addition to a number of projects underway in various stages, that economic uncertainty will certainly be a major factor in new projects moving forward;” he says.
As firms manage cost volatility, managing fatigue among employees and subcontractors has become equally important, says McShane Cos. CEO Molly McShane. “It’s been a long two-to-three years working through labor shortages and supply chain issues, and people are getting worn out,” she says. “In the past, so much construction was being put in place that some general contractors could be selective about which projects they pursued. With deals [now] being scarcer, the competition among general contractors is stronger.”
At XL Construction, CEO Richard Walker echoes McShane’s concerns about staying competitive “as certain markets continue to slow down and additional general contractors move into markets that remain stronger,” he explains. The firm is back on the list and ranked No. 141 this year after not filing a survey since 2017.
For Farmington, Conn.-based KBE Building Corp., ranked No. 333, staffing is the company’s top challenge, says executive vice president Jim Culkin.
“Finding qualified people right now is something the entire industry is really struggling with,” he says. “We are all still dealing with the COVID hangover of supply change issues. The question is, how do you navigate these waters when you’re faced with these kinds of shortages?”
Ramin Cherafat, CEO of McCownGordon Construction, anticipates that 2023 will be a “very strong year,” tempered by industry challenges coming to a head throughout the year and further putting a strain on resources for firms.
“All economic data points are indicating that maintaining this level of activity may be challenging going forward,” he says.
Opus Design Build LLC President and CEO Tom Becker says that “businesses can deal with good times and tougher times, but uncertainty is especially challenging because it’s difficult to be fully committed to your strategy.” He explains, “I don’t think we are alone in this. I’ve talked to many leaders in the industry who are in a similar situation,” adding, “It’s going to be a very interesting year.”
Balancing Bottom Lines
Last year, total Top 400 revenue rose 16.2% from 2021 to $488.98 billion. Revenue rose only 4% between 2018 and 2021. Part of the recent growth is attributable to the inclusion of MasTec on this year’s list. The Coral Gables, Fla.-based firm, which contributed $11.6 billion to the total, opted to file as a general contractor after its acquisition of IEA, ranked No. 42 on last year’s Top 400. But even with MasTec’s contribution removed, total revenue would still be up 13.4%, the largest year-over-year increase in revenue since 2006-07.
After speaking with industry partners, Wharton-Smith Construction Group President and CEO Tim Smith says he found that work is moving, but completion schedules are being pushed further out, delaying revenue as a result. “It is improving some, and our backlogs are bigger than ever,” says Smith, “but we look forward to being able to build and bill on a regular schedule again.”
For Top 400 firms, profit margins have mostly stayed strong, but have not increased in step with gains in gross revenue, with 96.7% of reporting firms indicating they made a domestic profit in 2022, virtually identical to last year’s survey results. The median profit margin is down slightly, to 3.2% from 3.8% last year.
STO Building Group has been focused on efficiently managing resources so that “our clients don’t feel the negative staffing effects of the project date sliding out to the right,” says Executive Chairman James Donaghy. “Profitability and cashflow are the lifeblood of every contractor, and this market presents challenges which can disrupt the critical path when resources—for the CM or subcontractors—are not available as planned.”
Similar to Lendlease, Urban Atelier Group President and CEO Andy D’Amico says the company has been able to increase certainty by bringing owners and trade partners earlier into the process. It comes down to greater communication, he says. “In these circumstances, it’s vital to prioritize effective communication and collaboration with the owner, architect, engineers and subcontractors to keep parties engaged and aligned with the project goals.”
In many cases, collaboration can save money, says Steve Ennis, president and CEO of ASRC industrial—especially when “everything is more expensive,” he stresses.
“Whether it is fuel, parts, or materials, not only do consumables cost more, but logistically they take longer to get to the job site,” says Ennis. When prices are fixed, such conditions make it extremely difficult to know what the right price is when job schedules are moving, he adds. “We are also seeing a lot of clients who want to expand their payment terms, says Ennis. "A pay cycle that used to be 60 days going to 90-day or 120-day terms starts to make a huge effect on our bottom line, since we’re basically getting into financing for that change in receipt.”
New contracts for Top 400 firms total $557.1 billion, up 30.9% from last year. The median new contract total is also up, rising 20.4%. As with total revenue however, the biggest players have made the biggest gains. The top 10 firms account for $140.3 billion of that backlog, about a quarter of the total. Last year the top 10 collectively reported $80.2 billion in new contracts, or a little under 19% of the total.
Backlogs are strong for some, but higher interest rates are still spooking private developers, adding to industry instability, says Scott Blaine, president of Goodfellow Bros. With a potential pause on private work due to the economy, Blaine wonders when projects funded by federal infrastructure spending will kick into high gear.
“We are still waiting for the increase in shovel-ready public works projects promised by the Infrastructure Investment and Jobs Act and the Inflation Reduction Act,” says Blaine. “This would certainly help create jobs and stability within the AEC industry.”
In Barton Malow’s view, the availability of projects isn’t what ultimately affects bottom lines. “The projects are still all out there regardless of various economic indicators,” says Chuck Binkowski, COO and executive vice president. “The biggest impact to our bottom line comes back to labor availability.”
He adds, “There hasn’t been the natural progression in talent replacement that we see in other industries. The veterans have left or are leaving and there isn’t enough coming in to replace them.”
Alternative Scheduling Paths
Limited labor resources have encouraged some Top 400 firms to seek leaner scheduling methods that can accommodate smaller teams, facilitate collaboration and streamline work plans.
ANDRES Construction Services uses digital pull planning to complement the critical path method, says vice president of operations Stephen Miller.
“Our teams will pull plan to validate project milestones and complete weekly work plans that measure the complete/incomplete work from the previous work period, confirm the activities for the upcoming work period and plan the work in the following three-to -six week look-ahead period,” he explains. Through digital pull-planning tools, the team is then able to “quickly sort and summarize information for any work day or work area or trade.” The result is “clarity and consensus in the plan of what must be achieved each day to realize the project schedule,” says Miller.
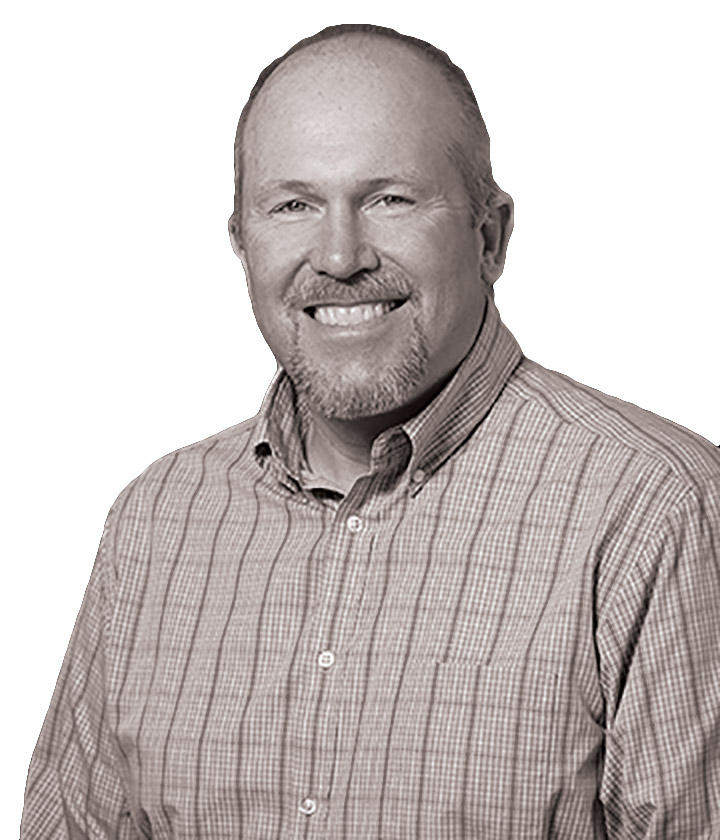
“We are still waiting for the increase in shovel-ready public works projects promised by the IIJA and the 2022 Inflation Reduction Act.”
Scott Blaine, President, Goodfellow Bros.
With the collaborative-focused last planner method, Hoar Construction President Turner Burton says the scheduling system improves accuracy and efficiency.
“Part of our mission as a general contractor is to eliminate waste of all types—time, money, materials in the construction industry—so using lean construction processes is essential to accomplishing those goals,” he says.
Similarly, Primus Builders uses the critical path method as a starting point for the last planner method, says COO Erik Gunderson. The firm is ranked No. 340.
“It starts with a high-level master milestone CPM schedule that identifies major milestones and the general sequence of how the project will be executed,” explains Gunderson, which includes checklists on items such as relevant submittals, procurement, delivery, and installation dates.“Each trade is accountable to the team for their contributions. Meetings with all trade partners take place weekly to update the schedule according to current conditions and to keep the team on track,” he says.
At DPR Construction, CEO and leadership team member George Pfeffer says the critical path method continues to be the team go-to method for long-term scheduling. “However, as we shift to more medium- and short-term schedules, we regularly employ other methodologies such as last planner and Takt, which better support our detailed project planning needs,” he says. “All scheduling methods are only as good as the data you are putting into them, so we’ve been putting a lot of focus on data-driven planning,” which can better leverages quantities, planned/actual production rates and crew sizes to ensure that sequences are planned for what is achievable in the field, he explains.
For Swinerton, the traditional critical path method schedule is the “beating heart of every Swinerton project,” says CEO Eric Foster. “We leverage business intelligence tools to employ alternative scheduling technologies in order to support various consumers with simplified role-based data,” he explains. “Business intelligence reporting is essential to ensure all stakeholders receive targeted and actionable data applicable to their specific roles and responsibilities.”
Complementing its business intelligence reporting, Poettker Construction has taken to using drones to track job progress and percentage completes, says CEO Keith C. Poettker. “Ultimately we tie that information back to our CPM monthly updates,” he says.
Poettker shares that the firm is also excited to see how newer technology such as artificial intelligence will impact scheduling and productivity in the construction industry.
“While I don’t think the AEC industry will ever lose the human touch of doing business, I do think AI will streamline processes, tasks and communication efforts in the future,” he says.
Digging Into Data & Technology
Clancy & Theys uses technology to make data-driven decisions, explains President Baker Glasgow. “We are constantly evaluating our technology stack inclusive of hardware and software,” he says. “We have come to the conclusion that there is no software that solves all of our issues; it’s always going to be a suite of softwares.” However, the company is adamant that any technology adopted does not work in a vacuum.
“We do not believe in duplication or double entry, so how one software interacts with another is absolutely paramount to understand when procuring and implementing software,” says Glasgow. Ranked No. 131, Clancy & Theys is in the process of procuring HR software that incorporates learning management and recruiting systems. Glasgow shares that the company is also going all-in on cloud-based project management software.
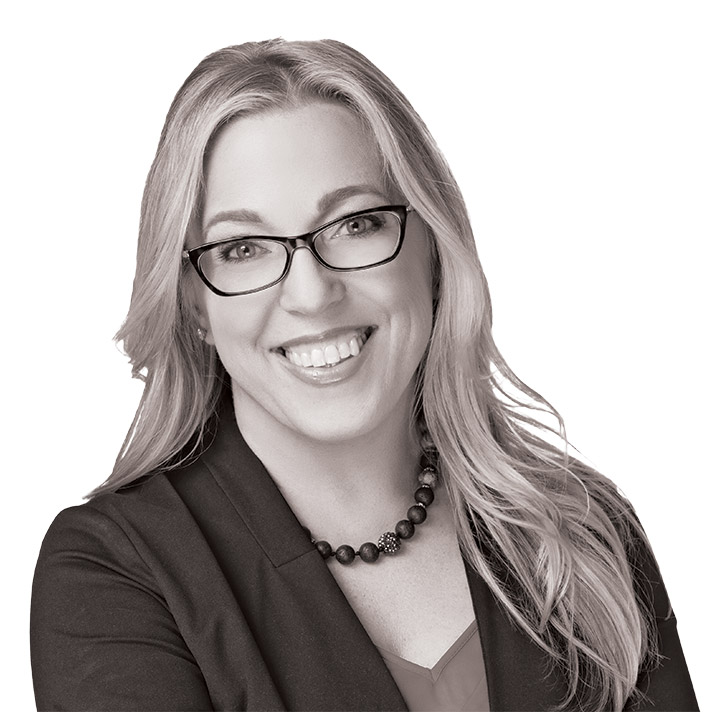
“It’s been a long two-tothree years working through labor shortages and supply chain issues, and people are getting worn out.”
Molly McShane, CEO, McShane Cos.
At McGough, the company is continuing to explore “better, more efficient ways to improve scheduling through analytics and monitoring tools,” says Nate Wood, executive vice president of regional operations. “We’ve implemented several programs including Deltek Acumen Fuse as well as 4D scheduling programs that improve planning and coordination on very large, complicated projects.”
For Boldt, one of the firm’s “biggest challenges” has been managing their personnel resources related to project staffing. “Knowing which personnel are available and when, so we can put the right people in the right place, at the right time,” is critical, says Rob Branyan, vice president of labor relations. He shares that over the past year, the company has incorporated a third-party workforce visibility platform into project planning and operations.
“This lets us track and forecast project needs and integrates into a lot of our existing platforms, so we can create long-term workforce strategies,” says Branyan. “Overall, this helps us keep our workforce engaged and our clients satisfied.”
In 2021, ANDRES Construction Services added a full-time data analyst to its team to focus on data collection, analysis and continued improvement across company operations. “Focused innovation and partnering with select construction tech developers has allowed [the firm] to add significant value for our clients, trade partners, and employee-owners,” says VP Miller.
At a jobsite level, a digital twin process functions in a similar way for Kraus-Anderson. The digital twin provides a dynamic, data-rich virtual replica of the built environment, “providing a visual common ground to support construction, closeout and asset management,” says COO and Executive Vice President Rich Jacobson.
Also at a job site level, DPR CEO Pfeffer says technology is “helping us keep people out of harm’s way like never before.” He adds, “We’re addressing some of the inherent safety risks on jobsites with a variety of solutions, from eliminating the use of taglines when lifting steel to robots that can drill ceiling penetrations without the poor ergonomics that workers in the trades experience.”
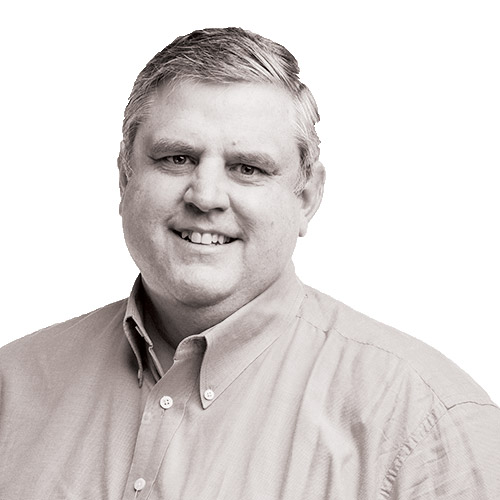
“All scheduling methods are only as good as the data you are putting into them. ”
George Pfeffer, CEO, DPR Construction
The safer the jobsite, the better for the skilled labor talent pool, and “the easier it will be to recruit and retain skilled craft workers,” says Pfeffer.
Ranked No. 21, Brasfield & Gorrie says the firm is also incorporating more robotic control technology, such as robotic layout and grade control.
“We hope to see our usage increase in the future. We also anticipate growth for AI-assisted tools for knowledge management and intelligent search across multiple platforms,” says chief strategy officer and chief information officer Chris Kramer.
Last year at Brasfield & Gorrie, a departmental-wide collaboration implemented digital dig boards on 41 jobsites.
“These allow project teams to see real-time information about utility lines, making our projects safer and more efficient,” says Kramer. “Workers can use their mobile devices to quickly identify the utility lines around them by scanning a QR code on job sites that use digital dig board.”
Melissa Faulkner, Skanska senior vice president and head of USA information technology, says the firm spent the last few years building and investing in their cloud-based infrastructure.
“With improved data quality and accessibility, we’ve uncovered valuable insights using project data found across all our platforms,” she says. In addition to minimizing risk and safety hazards, the infrastructure “creates more efficient ways of working, and drives performance certainty for teams, subcontractors, and clients.”
Planning for the future, Faulkner says the investment in the firm’s data infrastructure will allow it to leverage AI advancements, natural language processing and machine learning to “quickly share knowledge across the company and predict and anticipate project risks.”
Considering the construction industry’s ongoing labor shortages, MYCON General Contractors partner and vice president Ryan Stoll says advances in technology shows potential to increase “efficiency immensely.”
“We are patiently waiting to see how the recent surges in artificial intelligence will affect our industry,” adds Stoll, who describes MYCON as a “data-driven construction firm that leans heavily on using technology and data” to drive business decisions.
“Instead of just tracking budgets, costs and projected costs, we are tracking and analyzing cost data from multiple perspectives,” says Stoll. The strategy has helped the firm streamline operations and pinpoint optimal project types.
Natural Gas | By Jonathan Keller

Photo Courtesy of Zachry Group
Zachry Group (No. 33), along with its partners, Chiyoda International Corp. and McDermott International Inc., are providing engineering, procurement, construction and commissioning for the Golden Pass LNG project in Texas. It will add liquefaction and export capabilities to an existing import facility. When completed, the facility’s three liquefaction process trains are expected to produce 16 million tons of liquefied natural gas (LNG) per year. The project will also upgrade an existing pipeline, including installation of three miles of 24-in. pipeline to facilitate bi-directional flow capability.
Hot Markets
Revenue in all markets that ENR tracks rose between 2021 and 2022 except for the transportation, which was down for the second consecutive year. The sector with the biggest gains was manufacturing, up 72.32% to $25.3 billion dollars. More firms seem to be entering the market, with 130 firms listing manufacturing revenue in 2022, up from 115 in 2021. Last year 35 firms made more than $100 million in the market; this year 45 did.
With the passage of the CHIPS Act, Gilbane Building Co. President and CEO Tom Laird says the company is seeing great opportunities in the advanced electronics sector as well as in life sciences and food and beverage manufacturing—in addition to a renewed vigor for onshore manufacturing.
“These are priority investment areas for the company. Fortunately, we are well-positioned for these opportunities,” says Laird, naming the Intel Ohio Fabs project and Constellation Brands Brewery Expansion projects among opportunities for the firm.
CFO Michael Williams of No. 42-ranked Black & Veatch shares that “economic uncertainty” and industry challenges such as inflation and supply chain constraints are indeed having an impact on the firm's clients decision-making process. However, “demand for services stemming from the decarbonization, electrification, water scarcity and energy transition megatrends facing humanity continue to build solid pipelines and backlog,” he says.
Williams says the firm remains disciplined in “our contractual arrangements ensuring we are not taking on risk that cannot realistically be managed or mitigated in the current environment.”

“We are patiently waiting to see how the recent surges in artificial intelligence will affect our industry. ”
Ryan Stoll, Partner, VP, MYCON
Speaking on projects connected to the energy transition, a Bechtel spokesperson says meeting environmental sustainability goals will require a “more everything” approach from a project perspective.
“We need to continue building more renewables, introduce more technologies and innovations, but we also need to utilize mature scalable technologies we have, like LNG, nuclear and hydro,” says Bechtel. “Improving efficiency and targeting emissions elimination in existing infrastructure all have near-term positive impacts that are largely self-funding and should not be ignored.”
No. 104-ranked Blue Ridge Power is constructing a 305-MW solar project in Texas, with another 1.8 GW of projects in the pipeline from that state alone, says senior marketing manager Casey Hulme.
“Texas and California continue to lead in the utility-scale solar installation market,” she says, citing a 2022 American Clean Power Q4 report that found Texas installed 3.9 GW last year—the most in the U.S.
Russell Group President Caitlin Russell says an uptick in the firm’s multifamily housing construction is being driven by a demand in the “smile,” or Sun Belt, states of the country. “There also continues to be a driving need for affordable housing, including government assisted, senior, student, low-income and workforce,” she says. “The health care and manufacturing markets are also seeing some growth, with a focus from just-in-time to the readily available.”
Overall, revenue is up for the strong majority of Top 400 firms. Of the 378 firms who filed both this year and last, 78.0% saw an increase in revenue in 2022. On last year’s survey, the equivalent number was only 58.6%. Median firm revenue is also up, rising 15.3% to $567.9 million.
Moreover, international contracting revenue is up 12.8% to $29 billion, its highest total since 2019. However, the majority of the gains are concentrated among larger international players. Of the firms that made more than $100 million in international revenue this year, 73% had more international revenue than last year. For those firms below $100 million, that number was only 39.4%. Median international revenue actually fell 9.4%, to $67.5 million.
Safety | By Jonathan Keller
GCs Revamp Safety Training
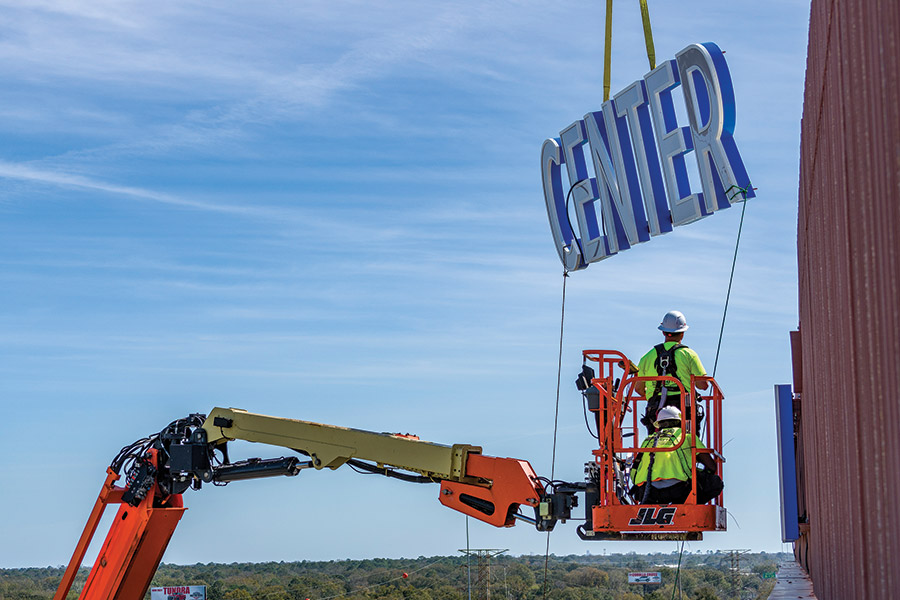
Photo Courtesy of Brasfield & Gorrie
Statistics show that new hires are especially vulnerable to safety incidents. The 2022 Travelers Injury Impact Report showed that about a third of the injury claims in the period it analyzed occurred during an employee’s first year on the job. Data from Birmingham, Ala.-based contractor Brasfield & Gorrie LLC (No. 21) shows that the first 90 days is an even more important timeframe for training and supporting new employees, says Troy Ogden, vice president of safety and learning with the firm.
In order to minimize that vulnerability and keep safety top of mind for more experienced workers, Brasfield & Gorrie launched SKILLED, a comprehensive training program combining safety and skill training in 2022. The program is a combination of in-person training and on-demand video, available with captions, in both English and Spanish. “Because our target audience—craft employees—typically doesn’t use computers for their jobs, it was essential to build a mobile-friendly platform,” says Ogden. The firm also created a series of hardhat decals so workers can show off the training they’ve completed.
New hires at Brasfield & Gorrie are provided a blue vest to be easily identifiable on the job site. “In addition, to ensure that someone is consistently watching out for new hires, we assign a mentor to each new employee during that period,” adds Ogden. New hires also have the opportunity to earn a prize for completing the First 90 Days training on SKILLED.
For Landmark Construction LLC (No. 189), the 2022 goal was to take a more granular approach to safety training. “Developing a role-centric HSE training matrix allowed us to concentrate on the essential basic compliance of OSHA 10 and 30, CPR/First Aid/AED, and an additional 25 role-specific training programs,” says Josh Landrum, safety manager at Landmark.
In January, KBE Building Corp. (No. 333). rolled out a 10-hour safety program to complement and exceed the standard OSHA 10. “We’ve looked over the history of subcontractor safety performance on our projects, identified the core safety issues that we see time and again, and put together a program focused on those key trouble areas,” says executive vice president Jim Culkin.
The program includes 14 breakout sessions that cover very project-specific safety topics. “For example, we cover fall protection in detail, but we focus on making sure that the trade employees using the fall protection system have the right equipment and are properly trained in how to use it,” says Culkin. The program is provided during the first 30 days of employment and as a required annual refresher course.
Firms Invest in Employees
In addition to tackling industry challenges and changes, Top 400 firms also celebrated myriad levels of company successes.
At Granite Construction, President and CEO Kyle Larkin says the company is proud to have “de-risked our portfolio away from large design-build projects.” The firm is now moving toward “collaborative contracting methods such as construction manager/general contractor (CM/GC) and progressive design-build (PDB),” says Larkin.
When it comes to labor recruitment and retention, many firms say they have added enrichment programs and stepped up their safety programs to greater cultivate and protect its trade partners and in-house teams.
“Internally, our team has taken formal steps to better support the quality craftsmanship of our employee owners and to foster a strong and diverse workforce for years to come,” says MW Builders COO Jason Evelyn. Last summer marked the inaugural class of the firm’s Emerging Leaders Program—a multiyear continued learning and development program for recent project engineering grads.
“Being able to provide continued education and the opportunity to explore multiple career paths within the
organization has proven to be an invaluable tool in recruiting and retaining world-class talent nationwide,” says Evelyn.
Sundt vice president and corporate director of health, safety and environment Paul Levin says Sundt’s biggest success in the last year has been the company-wide rollout “Stop the STCKY,” (which stands for stop the Sh*T That Can Kill You).
“Over the past decade, the industry’s average recordable injury rate (RIR) has gone down, but its fatalities have remained steady,” says Levin, explaining that it is this gap that the company is looking to close in on by implementing the program on its job sites.
The program focuses on eight areas of high-risk work and the identification and implementation of adequate controls needed to complete the work safely, Levin explains. “Data is collected during STCKY Walks (high-energy control assessments) and analyzed to help us effectively review, manage and implement improvements, trainings, coaching and best practices to continue our effort to stop the STCKY,” he says.
McShane adds that implementing programs that reinforce company culture and values are just as important as addressing industry challenges.
There is no value engineering needed to simply ask, “What can I do to help?” explains McShane.
“We’ve been able to respond to the outside pressures by calling on our culture. We’ve seen a fair amount of challenges over the last few years, but our people have shown their dedication and commitment to our team,” she says. “Character is revealed during times like these, and I couldn’t be more proud.”