As jobsites become even more connected with broadband and other services, equipment providers are giving their contractor customers more capabilities to take advantage of project data, whether from a 3D model or even take the steps to make materials supply chains more sustainable.
In November, Volvo Construction Equipment signed an agreement with Dublin, Ireland-based CRH, a global provider of construction materials spanning cement, aggregates, asphalt, glass and plastics, to work together on electrification, charging infrastructure, low-CO₂ fuels and renewable energy. Volvo CE is targeting 35% fully electric sales by 2030 and hopes to achieve net-zero greenhouse gas emissions across its entire value chain by 2040. CRH is targeting a 30% reduction in group-wide emissions by 2030 and to become a net-zero business by 2050. Both companies say meeting these goals will likely involve extensive vehicle electrification and charging infrastructure to reduce transport emissions, as well as improved productivity and sustainability services.
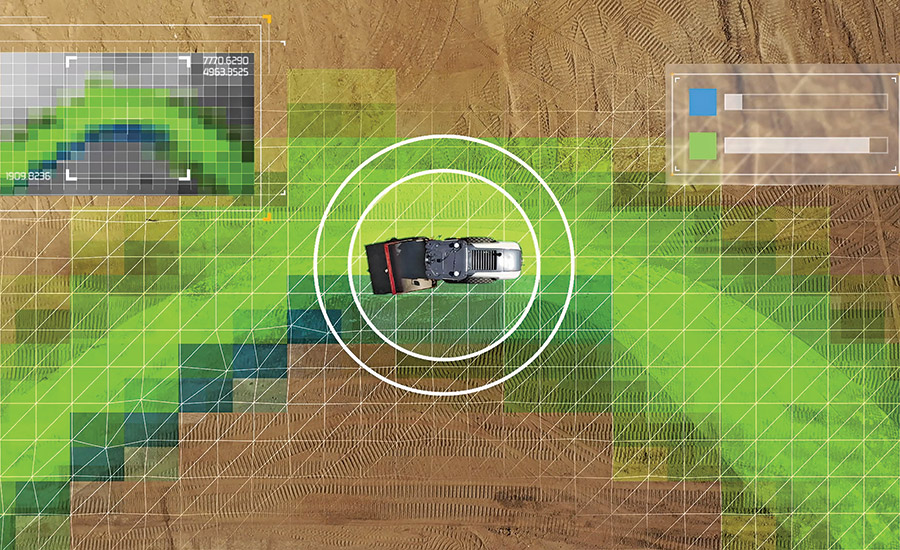
Trimble Earthworks Grade Control Platform offers autonomous operation.
Screenshot courtesy of Trimble, Inc.
Dead Reckoning
Dusty Robotics hard-working layout printing robot draws layout markings directly onto a floor slab with 1⁄16-in. accuracy, taking its position from total stations and the site model. While it was able to navigate around wall and MEP elements, now even I-beams coming up through the floor plate blocking its path aren’t a problem for the Dusty robot.
“One of the things our engineers have developed is the ability to print without line of sight,” says Dusty CEO Tessa Lau. “[A] limitation of all the service station-based systems is as soon as you lose that line of sight, you’re done. But if you look at that I-beam we’ve actually printed all around it without restriction. Our robots capable of actually printing on congested jobsites.”
Dusty’s engineers have added the ability for the printer robot to estimate its direction and distance traveled by dead reckoning alone and not have to rely on a service station for live positional information. When the little robot is finished circumnavigating I-beams and other obstructions, it can go back to navigating off the signal from the nearest station.
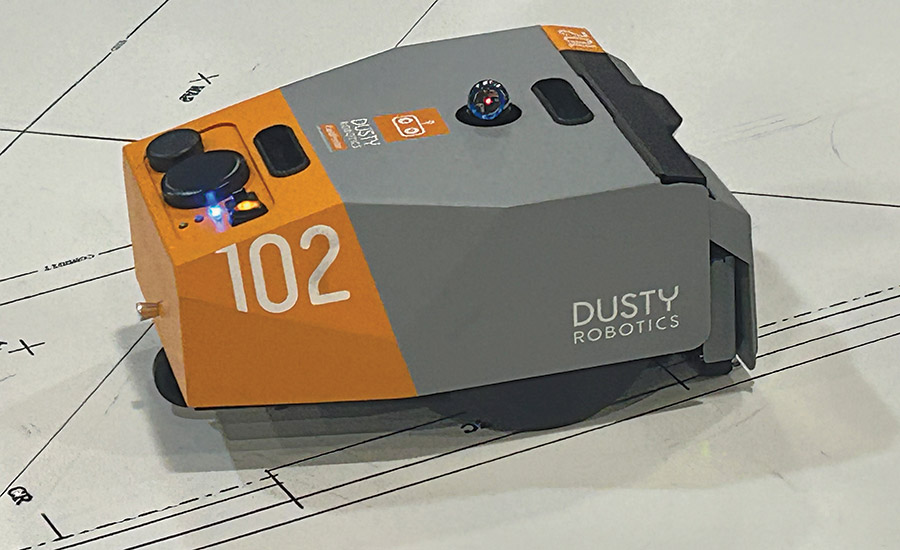
Dusty Robotics’ site layout robot can now rely on dead reckoning.
Photo courtesy of Dusty Robtics
Everyday Autonomy
Trimble completed its first test of a fully autonomous soil compactor on a live site in November. The Trimble Earthworks Grade Control Platform for Autonomous Compactors was mounted on a Dynapac CA 5000 soil compactor and tested at the Site C Clean Energy Project on the Peace River in British Columbia. The massive $11.8-billion hydropower project is expected to deliver 1.1 GW of power when it comes fully online in 2025 [ENR 10/2-9/23 p.18] This trial by Trimble is one of the first public tests of a fully autonomous compactor on a live construction site.
The autonomous machine completed 37 hours of compaction work, operating with a mixed fleet of compactors, the rest of which were running the Trimble CCS900 Compaction Control System. Data from all machines was delivered using Trimble WorksOS Software, which is being used as the system of record for all compaction data on the site. The contractors are ACCIONA Infrastructure Canada Inc. and Samsung C&T Canada Ltd.
“The Site C project was the perfect place to begin live testing of the fully autonomous soil compactor because of the cost and safety benefits that autonomy will bring to large infrastructure projects like this in the future, and because of the willingness of the project owner and contractor to use new technology on their jobsite,” says Cameron Clark, earthmoving industry director of Trimble’s civil infrastructure solutions.