Digging Deeper | Renovation/Restoration
Super Columns Support NYC Warehouse Renovation

The team renovating the historic Terminal Warehouse in Manhattan retained the existing landmark masonry facade.
Photo Courtesy of New Line, L&L Holding Co. and Columbia Property Trust
All marriages are complicated, but not many involve blending six building systems, adding a six-story “overbuild” and selectively demolishing and rebuilding large chunks of a 133-year-old New York City industrial structure—all while preserving its landmark facade. Those are all part of the project team’s mission on the estimated $2-billion-plus renovation and reconstruction of the historic Terminal Warehouse building in Manhattan’s Chelsea neighborhood.
The hulking full-block structure built in the 19th century to serve as a freight railroad hub next to the Hudson River—and later housed a chic 1980s nightclub—is set to open later this year as Terminal Warehouse, a 1.3-million-sq-ft office and retail development.
The development team topped out the 13-story complex last year and is working on the last of four quadrants it designated to manage the effort—led by the ownership group of Columbia Property Trust, L&L Holding Co. and Cannon Hill Capital Partners; New Line Structures as construction manager; and CookFox Architects and DeSimone Consulting Engineers on the design team.
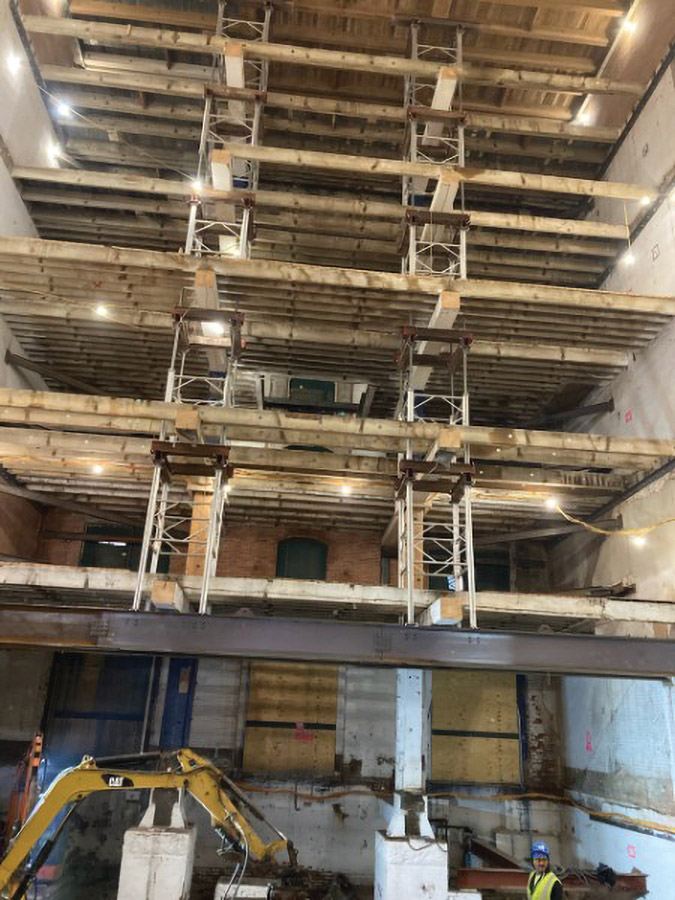
The project’s historic facade needed bracing before full demolition of the interior could begin.
Photo courtesy of New Line, L&L Holding Co. and Columbia Property Trust
Replace, Build, Rebuild
From the start, the team knew it had to figure out what elements it could retain from the original 1891 structure, what it had to replace, what needed to be newly built and what had to be rebuilt—and how to blend these, says Rodolfo Medina Jr., senior associate at DeSimone. “It’s a combination of almost every imaginable building system you have from a structural perspective,” he says, citing the mix of existing timber, steel, masonry and iron with new concrete, steel, glass, metal and planted matter.
Each quadrant, separated by masonry bearing walls, featured unique conditions and materials, says Glen Diorio, executive vice president at New Line Structures. Within the quadrants were another 25 distinct building segments, further stratifying the task, he says. “There was a lot of commingled construction due to fires over the years, so there were areas that were rebuilt in different formats,” Diorio adds.
The first section of the 711-ft-long building—known as Block A and located next to the Hudson River on 12th Avenue—largely had original timber, which the team determined had to be removed and replaced with a concrete superstructure.
“The intent [of the overbuild] was to add additional floorplate on the 12th Avenue side where you could overlook the waterfront.”
—Rodolfo Medina Jr., Senior Associate, DeSimone Consulting Engineers
The next quadrant heading east—as the building stretches from 12th to 11th avenues between 27th and 28th streets—is Block B, which had reconstructed steel and concrete sections. The next, Block C, kept its timber frame but with significant modifications to create an atrium-topped central courtyard and a 2.5-acre interior green space bordered by 29 setbacks and terraces.
The team also wove in another major feature—the 200,000-sq-ft overbuild comprised of six new office floors with floor-to-ceiling windows above the westernmost A and B blocks. “The intent was to add additional floorplate on the 12th Avenue side where you could overlook the waterfront,” Medina says.
The overbuild called for new foundation supports and columns to carry the load of the added floors without compromising the historic structure while also ensuring the varied building systems lined up through the quadrants, Diorio says.
Looming over all of that coordination was the central task—maintaining the landmark structure’s look outside.
“Preserving the historic facade of Terminal Warehouse during structural demolition was a remarkable achievement that demanded innovative problem-solving and precise execution,” says Adam Boggia, vice president at L&L. “Our team implemented a solution involving the installation of more than 350 tons of facade bracing steel before initiating significant demolition work.”
That shoring structure not only braced the facade—which was freestanding during wholesale demolition and rebuilding of Block A—but also gave crews access to repoint and restore the brickwork. “It served double duty,” Diorio says.
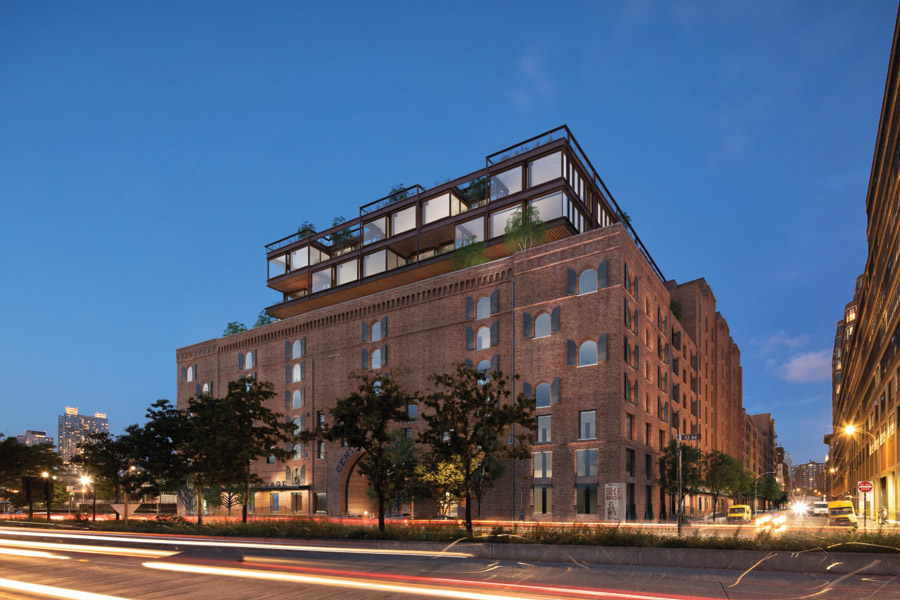
The NYC Landmarks Preservation Commission pushed to preserve the building's original industrial character to fit in with the surrounding historic district.
Rendering courtesy CookFox Architects
Landmark and Tunnel
The original development team—L&L with different investment partners—acquired the complex overlooking the High Line and river for $880 million in 2018, and the design team began work soon after. The project also won unanimous approval from the city Landmarks Preservation Commission in 2020, a critical step.
The commission “stressed the need to preserve the original industrial character and the building’s harmony with the surrounding historic district,” says Darin Reynolds, CookFox partner. “We maintained the proportions and details of the original wood and divided-lite double-hung windows while upgrading them with new high-performance aluminum and glass.” Reclaiming and showcasing interior timber—some dated to trees that grew 500 years ago—was also a key preservation goal, he says.
The design team produced final documents just as COVID-19 hit. Construction started in summer 2020, primarily with demolition, heavy excavation and foundation work on Block A, which continued through the following spring, Diorio says.
The developers then secured a well-publicized $1.3-billion construction loan package in 2021. The team completed the Block A superstructure in spring 2022 and topped off the overbuild floors one year later, with six floors above Block A and four above Block B. Work on Block D, which largely houses back office and other support features, began in January 2023 and continues this year, Diorio says.
The rail-and-river freight hub’s origin endowed it with quirky elements the team has integrated and also influenced renovation and construction. One element is a 689-ft-long tube in the structure’s bottom level. That basement still has two rail beds, which originally brought trains inside for loading and unloading alongside the docks, but later it housed the trendy Tunnel club for 15 years starting in the mid-1980s. Now it will be a double-height main artery for 75,000 sq ft of retail space.
The team also added features—from roof decks and cascading terraces to the glass-encased upper office floors—to create a modern desirable location. “Collaborating with consultants and leasing experts, we identified key building enhancements tailored to attract Class A tenants,” says Vincent Rende, Columbia vice president for development.

Crews have been working in the project tunnel that once brought trains inside for dockside loading and unloading.
Photo Courtesy of New Line, L&L Holding Co. and Columbia Property Trust
Super Columns
A key decision the team faced was whether to support the new overbuild floors with the existing structural system. Although the original warehouse was a high-capacity facility, BIM modeling, site surveys and engineering studies showed the condition of the foundations and superstructure—as well as the need to prevent facade stress, cracking or failure—would require more support and load modifications for the new section, Medina says.
The studies included below-ground testing of original piles driven into historic fill that makes up much of Manhattan’s West Side, says Steve Trapp, executive vice president at Columbia. “During the design phase, exploratory foundation probes were completed to load test the existing foundations and piles,” he says.
“The Landmarks Preservation Commission stressed the need to preserve the original industrial character ... with the surrounding historic district.”
—Darin Reynolds, Partner, CookFox
The design ultimately called for various alterations to Blocks A and B under the new floors. “We had a lot of challenges with the existing building foundations,” Medina says. “Those two quadrants had new foundations, new pile caps and new caissons drilled.”
The drilling was complicated given the tight spacing and logistics. “We needed a rig that was large enough to drill the piles and small enough to fit in the existing space,” Diorio says. “The drilling locations were inside the existing building and surrounded by structural elements, leaving inches of clearance to the right, left and back. The rig needed to be backed in to allow the pile material to be fed to the drill rig.” The team also had to selectively demolish floors above to open vertical clearances for the rigs and piles, he says.
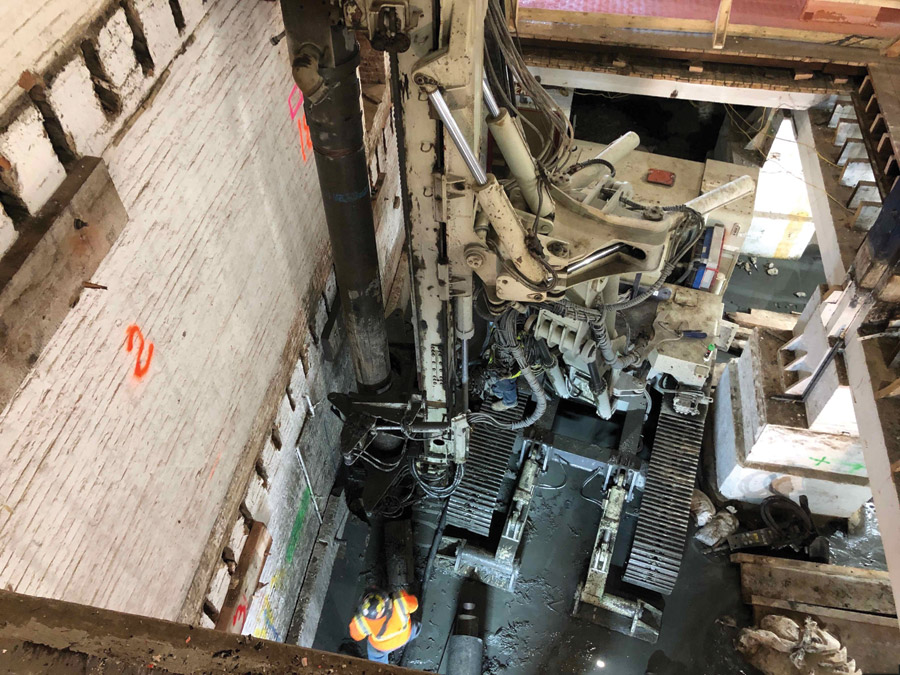
Drill rigs even drove temporary piles to support the bracing structure for the landmark facade beside Block A.
Photo Courtesy of New Line, L&L Holding Co. and Columbia Property Trust
Indoor Pile-Driving
Another task was to drive piles supporting new super columns that would be in both Blocks A and B—the supports that designers chose to hold up the overbuild floors. The rigs even drove temporary piles to support the bracing structure that held up the landmarked facade next to Block A, Diorio says. The design incorporated super columns not only into the rebuilt Block A but also in the existing superstructure of Block B, threading them through floors, Trapp says. “This construction required careful sequenced work with heavy equipment strategically located within the existing structure as piles and concrete were installed,” he says.
Strategically locating the columns was a demanding chore to ensure Block B still had desirable open spans. “One of the challenges was we didn’t want to create a forest of columns,” Medina says. “With the architect, we found locations close to those bearing walls.”
Minimizing the weight of the newly built floors was another key strategy, with the team opting to use a Cobiax floor forming system, a cast-in-place voided concrete slab with plastic hollows built in that help to lighten the overall load. “It’s a thicker slab, but it’s less weight in concrete,” Diorio notes.

Pile-driving within the existing building was required to support super columns to hold up the overbuild floors.
Photo Courtesy of New Line, L&L Holding Co. and Columbia Property Trust
New Light
The design sculpted a different challenge for Block C—asking the team to “carve out the center of the massive historic structure to form a monumental central courtyard to bring sunlight to the depths of the building,” says Ted Koltis, executive vice president and head of real estate at Columbia.
The retail tunnel also runs through the new central courtyard. “We are looking to create and cultivate what will be an interior street-like destination animated by shops and restaurants,” he says, adding there will also be spaces for fashion shows, live music and art installations. The multiple landscaped terraces, some penthouse-style, will overlook the courtyard as well.
Creating that central public area was a challenge given the “cavernous” original space, Medina notes. It involved selected, often asymmetrical demolition of the timber superstructure to create the setbacks and the need for new columns to adequately reinforce the structure, he adds.
“We needed a rig that was large enough to drill the piles and small enough to fit in the existing space.”
—Glen Diorio, Executive Vice President, New Line Structures
Another key Block C task was increasing the space between the wood floors to fit mechanical, electrical and plumbing systems, Diorio says. That entailed removing about half of the original wood joists no longer needed to support the building’s original storage load capacity. The team first lifted two floor levels, removed unneeded joists and then “sistered,” or bound together, the remaining joists before replacing the floors again. “That was a huge effort,” Diorio says.
Current work on Block D involves building systems—including modifications for elevator shafts, stairs and mechanical floorplates, Medina says.
That section also features work to restore and reinforce a massive brick archway that serves as a primary entrance to the building—and which in reality is a circular structure that continues below grade, he says.
The arch had been modified below grade by prior tenants and in places needed additional reinforcement, Medina says. Block D—which was not part of the original design plans but added later—also entails ongoing work on MEP systems this year along with roofwork, facade restoration and structural and bulkhead tasks, Diorio points out.
Sustainable Status
The completed project is targeting LEED Gold and WELL certifications, in part thanks to its reduced embodied emissions through extensive retention of masonry and timber, with the project estimated to save 54,000 metric tons of carbon, Reynolds says.
Along with natural light, fresh air in outdoor spaces and advanced air filtration, another sustainable feature is a strategic flood mitigation system. The riverside property flooded, like much of the West Side during Superstorm Sandy in 2012, with its foundation slab “popping” with water that burst in through cracks, according to Medina. The team created a watertight zone in one section under Blocks A and B with pile caps, 26-in. to 30-in. pressure slabs and new concrete walls.
However, it also installed features such as vents in the doors in other parts of the basement to let water flow in during flooding, all to create a hydrostatic balance in the area, which can prevent slab popping and normalize water levels outside of the flood proof zone, he says.
That’s an atypical strategy in the New York region, but “given the location it definitely makes sense,” Medina says. “It was a very interesting application.”