Digging Deeper | Cultural
Distinctive Visitor Center And Hotel Finally Take Flight

Located just outside the U.S. Air Force Academy’s North Gate, the Hosmer Visitor Center takes design cues from aircraft in flight.
Rendering courtesy Fentress Architects
A new visitor center and hotel just outside the North Gate of the U.S. Air Force Academy in Colorado Springs are pretty hard to miss. The multi-planed roof design of the former conjures images of fighter jets staggered underneath each other, and the two structures are connected via a pedestrian bridge.
The budgets for construction—$38 million for the Hosmer Visitor Center and $170 million for the 375-room Hotel Polaris—are only about half of the total outlay for the $500-million project, which also includes earthwork and infrastructure. There are also plans for office and retail developments on the 57-acre parcel, branded TrueNorth Commons.
Colorado Springs-based GE Johnson won the design-build RFP along with Fentress Architects of Denver for the visitor center; Atlanta-based BLUR Workshop won the design contract for the hotel. Wichita, Kan.-based Wildcat Cos. spearheaded the $22-million infrastructure project, which included the pedestrian bridge connecting the hotel and visitor center over North Gate Boulevard.

Each of the visitor center’s four roof panels has a different slope, with the same underlying geometry for the sake of manufacturability and installation.
Image courtesy Fentress Architects
The overall project concept originated as one of several of the City of Champions projects that garnered $120.5 million in state tax incentives via the Regional Tourism Act in 2014. Dan Schnepf, president of Blue & Silver Development Partners, has been working on the project for about a decade.
Schnepf started Blue & Silver to pursue the project. “Obviously, blue and silver are the colors of the Air Force Academy,” he says. “I’m a 1983 graduate of [the academy], and I wanted to do something to give back to the institution.”
Schnepf calls the project “a unique private-public partnership” that had two false starts. “The Air Force put out an RFP in 2015 and another one in 2017,” he explains. “They did not allow for the use of public funding in the project—in other words, bonding.” While Schnepf assembled a design-build team and responded to both proposal requests, funding “kept falling off the table in the congressional budgeting process,” he says.
At Schnepf’s urging, the academy’s stance changed with a subsequent RFP in 2019 that allowed for bond financing. “We ended up doing what’s called an enhanced-use lease,” he explains. “It’s basically a barter program. They take a piece of underutilized property, and they end up making it available to the development community for the purposes of developing that property in exchange for the developer building and designing and providing at no cost the visitor center and all of its accouterments, the infrastructure and everything.”
But COVID-19 wreaked havoc on the bond market in March 2020, upending the original deal. About two years later, the project officially got underway. “After carrying the project at great cost until 2022, the bond market opened up, and we got the same bond buyers to purchase the bonds, and we were able to raise $422 million for the project,” Schnepf says.
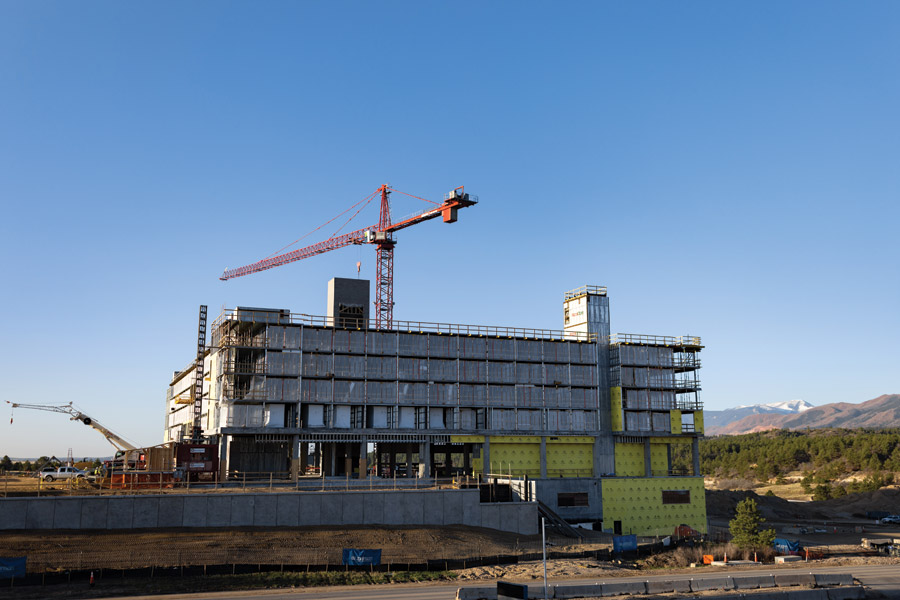
With 375 rooms, Hotel Polaris will be the second-largest hotel in Colorado Springs when it opens in late 2024.
Image courtesy the Unfound Door
Rethinking the Visitor Center
In the wake of 9/11, stringent security measures impacted the original visitor center on the AFA campus. Annual attendance waned from more than 1 million to about 250,000. The post-9/11 dynamic led to the idea of moving the visitor center outside of the academy’s North Gate.
Situated on a bluff just west of I-25, the 34,000-sq-ft center is nearing completion after the project broke ground in late 2022. Featuring a mezzanine on the first level and core and shell on the second level, the steel structure supports a metal wall panel, curtain wall and three metal panel roof systems. Schnepf says the new facility could return attendance to the pre-9/11 levels when it opens in late 2025. The exterior and structure are due for completion this spring, then the AFA will build out the interior.
“Because the roofs are so important, we didn’t want any penetrations.”
—Kendall Dietzius, Project Manager, GE Johnson
Martin Eiss, associate principal with Fentress, says the design took cues from the iconic Cadet Chapel, which is currently under renovation, and other existing structures on the academy’s grounds. “The other inspiration was really the idea of flight,” he says. “The idea was really to take that and turn it into the idea of an airplane taking off.”
Curtis Fentress, the firm’s namesake founder and principal in charge of design, says bringing the project’s unique design to reality has been no small task. “[Eiss] had a big idea about making this roof to represent aircraft wings,” says Kahyun Lee, Fentress associate principal. “The challenge was how to make it more manufacturable.”
Lee’s 3D modeling work was a critical step in route to construction. “All the roofs have different slopes, but they have the same geometry,” she says. “It appears that everything is unique, but it’s not. So when it comes to the manufacturing and installing, they all have the same kind of metal panel shape and soffit curvature underneath of it.”
After the original manufacturer went out of business last year, the team enlisted Kansas City, Mo.-based Zahner to build the roof panels, a decision that impacted the budget and necessitated design changes.
Kendall Dietzius, project manager with GE Johnson, says the 43-degree angle of the steepest roof “was crazy from an installation standpoint.”
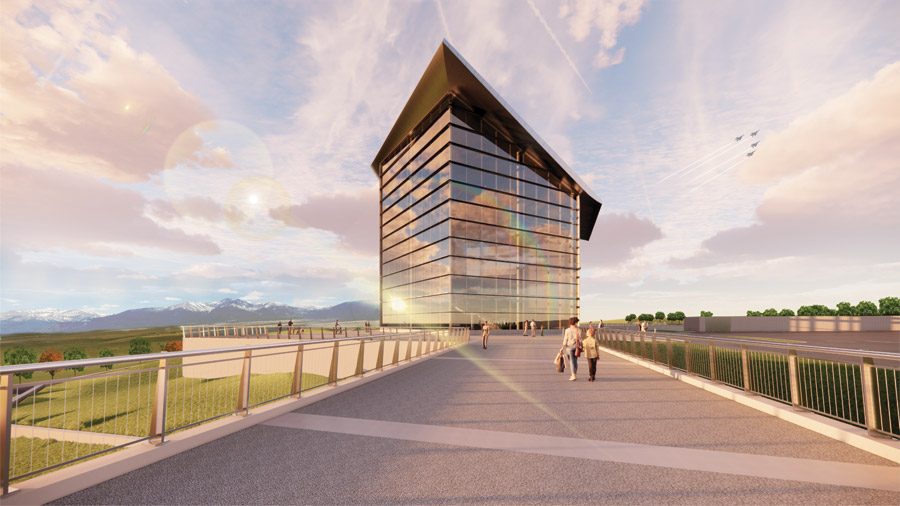
A pedestrian bridge spanning North Gate Boulevard links the visitor center to the hotel.
Image courtesy Fentress Architects
Aesthetics are critical, but so is functionality and drainage. “Because the roofs are so important, we didn’t want any penetrations through the roofs, which typically would have vents and mechanical and things like that,” says Eiss. “Everything mechanical has to go out through the side of the building, so we’ve got louvers and we’ve got vents that are all organized to allow all of the mechanical intake and exhaust to go through the side of the building and up through the roof.”
Dietzius says “integration of all of the different design elements” was the primary challenge. “We worked through issues with tolerances down to our foundations up to the metal deck before we got into roofing elements,” she explains. “There was no tolerance buildup in the system, so we had to work through a lot of those issues and figure out design changes that worked from a construction standpoint.”
Kellen Starr, GE Johnson senior superintendent, says the wet summer in 2023 was another challenge, but construction of the roofs and the exterior skins had the biggest logistical issues. “We probably had eight boom lifts on site at one time working in very close proximity,” he says. “You had ICI doing the framing and sheathing, Gen3 was doing the air and water barrier and other panels, El Paso Glass was doing the curtain wall and the clear story. All of that work trying to happen in sequence behind each other was difficult.”
Eiss says research and help from Duane Boyle, the academy’s architect, led to a design based on the same 7-ft grid that’s omnipresent in AFA architecture. “We began to notice that the academy has a seven foot by seven foot module. It actually can be seven inches, seven feet, 14 feet, 28 feet. That was important to replicate in this building.”
Boyle says Walter Netsch Jr., chief architect of the AFA campus in the 1950s, based the 7-ft grid on the dorm beds when seeking to streamline the project. “[Netsch] asked himself what was the most repetitive thing there was going to be designed and constructed at the academy, and that was the dorm rooms,” explains Boyle. “And the most important thing in that dorm room is the bed, and an American bed from the toe of the bed to the wall was approximately seven feet long.”
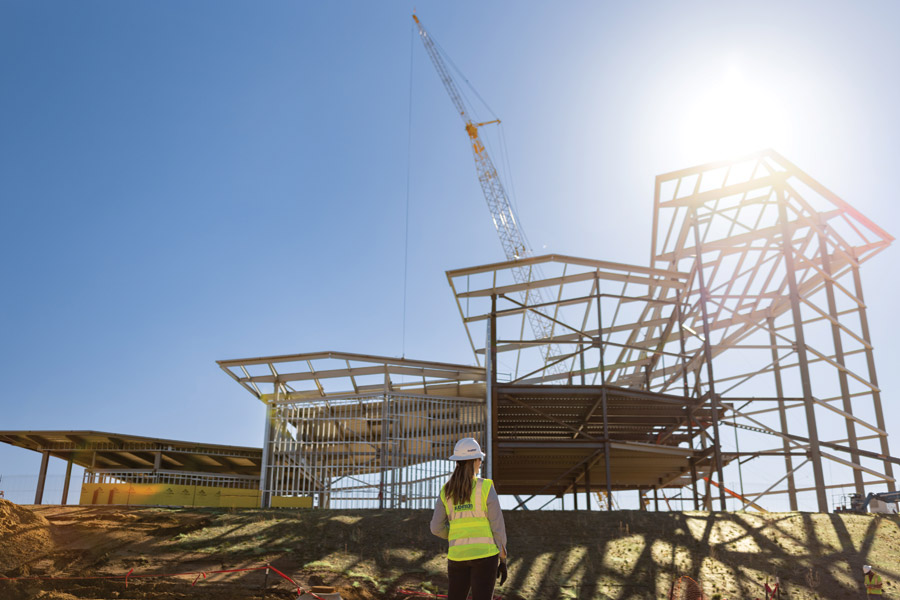
Construction scheduling of the visitor center’s roofs and exteriors has been a logistical challenge.
Photo courtesy the Unfound Door
Ticket to Ride
Stakeholders envision Hotel Polaris filling a void near the AFA. “There’s a definite need ... there in Colorado Springs for some new product, especially product that could handle large business,” says Jerret Click, vice president of construction and design for Dallas-based Matthews Southwest, the firm that has managed the project for the owner, Baton Rouge, La.-based Provident Resources Group, since the groundbreaking in summer 2022.
With 375 rooms and 26,000 sq ft of event space, the 356,871-sq-ft hotel is positioned to handle any increase in demand when it opens in late 2024. The building incorporates a structural slab on void, slab on metal deck, post-tensioned slab, concrete column construction and structural steel. It is the first project in Colorado Springs to use Redicor, a modular steel building system.
In a nod to the location, F-16 and 737 simulators will be available to guests when the hotel opens. “These are not toys or games,” says Schnepf. “These are the real deal.”
The trick has been building a full-service hotel that doesn’t look out of place. “I think the real challenge was trying to be compatible with the historic campus and respectful of what had been done previously without trying to replicate what was there,” says Scott Morris, principal of Atlanta-based BLUR Workshop, the hotel’s architecture firm.
“When you have a project and it’s iconic, and people want to build a reputation behind it, I think they tend to work better together.”
—Dan Schnepf, President, Blue & Silver Development Partners
“We spent a lot of time looking at materials and systems that we thought were a more contemporary version of what they had done, but still a clear nod to some of the mid-century modern stuff that they had done up on the hill,” he says.
Travis Jury, project manager with GE Johnson, says the primary construction challenge, aside from the sheer size of the project, has been “trying to balance the four quadrants of development” on the parcel. “We were bringing dirt from one quadrant to the other,” he says, noting that about 30,000 cu yd from the visitor center site filled in the hotel site.
Jury says a phased permitting approach helped mitigate scheduling issues, with different permits for the foundations, superstructure and finishes.
Prefabrication of the stairwells and bathrooms also helped. SurePods manufactured the latter in Arizona and began delivering them in late 2022. Ben Schlick, GE Johnson senior superintendent, estimates prefabrication saved “at least 27,000 man-hours” on the project.
“Those were really critical, because in a guest room 90% of the work is in the bathroom,” says John Webber, GE Johnson senior project manager.
“I think we were schedule-challenged from Day 1, because we were trying to balance progressing the design with getting released to do construction.… It was a constant overlap of design and sequence and construction way behind it.”