At a time when developments can be weighed down by a variety of concerns—limited workforce, material cost escalations and financing to name a few—Post Brothers has found ways to lighten the load on its One Thousand One mixed-use project in Philadelphia. When completed, the structure is expected to include nearly 1,500 residences, making it one of the largest residential projects underway in the U. S., according to Post Brothers. The development is split into three phases totaling 1.9-million-sq-ft, including the more than 828,000-sq-ft first phase. To deliver that massive phase, Post Brothers, which serves as both the developer and builder, faced potential labor shortages and significant costs related to conventional concrete construction.
Working with designer BKV Group, the team devised a solution that allowed it to use a cold-formed, panelized building system with cross-braced bearing walls rather than a conventional concrete structure to meet its needs. By using that system, the team claims that it was able to save potential costs by lightening the structure while reducing labor demands on site through the use of panels that are fabricated off site. Post Brothers says it is the largest project under construction in the country to use this system.
“When you pick a structure, you pick one that is complementary to the workforce at hand,” says Sarina Rose, senior vice president of development at Post Brothers. “You reduce the bidding field significantly if the labor pool isn’t there for the specific type of construction that you’re doing.”
The first phase broke ground in 2022 and was initially scheduled to be completed this year. Post Brothers declined to provide an updated completion date, but the final tower topped out this month. The project ranked at the top of ENR MidAtlantic’s Top Starts list for 2022.
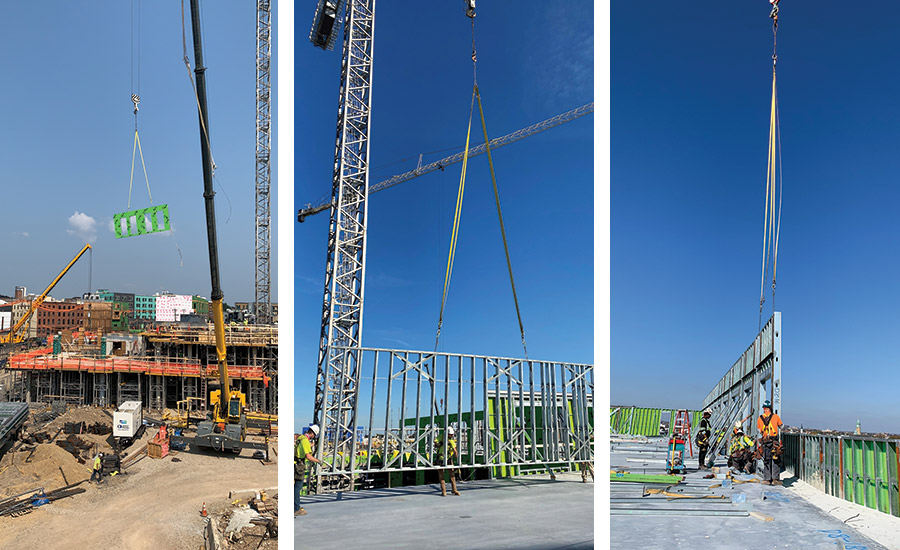
To build the towers, 202 tractor trailers delivered 3,134 panels manufactured locally from coil stock by Klover Contracting. Just-in-time delivery was used and panels were picked directly from the trucks by tower cranes.
Photos courtesy of Post Brothers
An Assemblage of Buildings
Set on a 3.5-acre site on South Broad Street at the south end of the roadway known as the Avenue of the Arts, the project’s first two phases comprise four L-shaped towers with interior courtyards and other amenity spaces. The towers are built to varying heights—eight, 10 and 12 levels—each with its own aesthetic identity.
“We were able to design an assemblage of buildings that look like they could have been built over time as different buildings in a collective community—not necessarily one megaproject,” says Jack Boarman, senior design leader at BKV Group.
“When you pick a structure, you pick one that is comp-lementary to the workforce at hand.”
—Sarina Rose, Senior Vice President of Development, Post Brothers
Although the towers appear to be separate buildings, they are all interconnected as a single structure.
The combination of the look of the project with the structural design may have helped move the project forward. The development initially had been pursued by Tower Investments as a 20- to 30-story tower, but it received some pushback from the community and the city, according to press reports. Post Brothers teamed with Tower Investments in 2021 and reimagined the project as a series of mid-rise towers that were more in keeping with the context of the neighborhood. In early 2022, the team closed on a $400-million construction loan for the project, according to media reports.
Boarman says that while the project is limited by the heights that can be achieved by using componentized steel wall construction, that limitation ultimately matched up with the mid-rise demands of the community.

The towers are built to varying heights—eight, 10 and 12 levels—each with its own aesthetic identity.
Rendering courtesy of BKV Group
Second Time Around
Although One Thousand One is the largest such project created by the team, it’s not the first. Before One Thousand One, Post Brothers had joined with BKV on Piazza Alta in Philadelphia—a 1.17-million-sq-ft development with 1,144 residential units. Similarly, the team used light-gauge steel, Type 1 material and componentized steel wall construction methodology to deliver the project.
Boarman says BKV has used this method on 28 developments over the last two decades, although not at this scale. He says that by using prefabricated light-gauge steel bearing walls—including exterior walls, demising walls and corridor walls—buildings can be constructed in 20% less time than a conventional concrete structure because most of the building—up to 60%—is fabricated off site. Boarman adds that though prefabrication can increase the costs of materials, the time savings can still result in a total project savings of 5% to 10%. For example, on a conventional project, Boarman estimates that a 20,000-sq-ft floorplate could require 30 ironworkers and carpenters to build a floor, while a panelized system could require 10 workers and take less time.
“A 20,000-sq-ft floorplate can be erected in 10 to 11 days, plus three days to pour the concrete deck and cure it,” he adds.
At Piazza Alta, the team was able to construct an above-ground parking garage wrapped with residential units. Rose says the team hoped to reduce structural demands with an above-ground parking garage at One Thousand One as well, but the city of Philadelphia would not allow above-grade parking on Broad Street. In response, the team devised a concrete structure with one level of below-ground parking topped with a podium that ranges from two to three levels in height. All of the towers sit atop the podium. The podium is Type 1a construction, while the towers are Type 1b.
The foundation uses caissons, but Rose says that because the structure above is relatively light, the team could avoid the need for deep foundations. By only excavating one level below grade, the team could also avoid potential groundwater issues. Although about 146,000 tons of earth was exported from the site in the excavation, the team did not encounter significant environmental issues, she says.
“It’s a way to move the money from behind the walls to the furniture and the countertops and the amenities that the residents all experience.”
—Jack Boarman, Senior Design Leader, BKV Group
Concrete Core
Before constructing the towers, elevator cores with stairs were built with a combination of concrete and CMU. This both provided structure for the panelized system and allowed elevators to be delivered prior to topping out each tower.
“The stairs and the elevator core perform the shear needs for the structure,” she says. “The prefabricated wall panels are cross-braced. They are quite robust and they tie to the slabs."
To build the towers, 202 tractor trailers delivered 3,134 panels manufactured locally from coil stock by Klover Contracting. Just-in-time delivery was used and panels were picked directly from the trailers by tower cranes. The site features two tower cranes—one 300 ft tall with a reach of 262 ft and the other slightly lower with a reach of 170 ft. For the decking system, the team used Comslab. The building uses 8-in.-deep decks with a maximum span of 25.5 ft.
To help speed construction, the units are stacked vertically by matching floorplans, including two-, three- and four-bedroom units.

Enhanced access into the site will be available between the Phase 1 and Phase 2 portions of the project.
Rendering courtesy of BKV Group
The process moves efficiently in large part thanks to extensive planning and coordination through building information modeling, according to Rose. Through BIM, the team was able to precisely estimate quantities, enabling team members to purchase large quantities of materials, such as coil stock, nearly a year before construction began. The panelizer, Klover Construction, conducted the BIM coordination on the project. The project did not utilize multitrade prefabrication, but Rose says that through BIM coordination and repetitive stacked layouts, systems installation has been efficient.
Aiming to provide distinctive aesthetics to the exterior of each tower, the team used a variety of exterior materials. At the street level, brick and terra-cotta are used extensively. “It truly is a reflection of what should be used for building facades in Philadelphia,” Rose says. “It pays tribute to the Avenue of the Arts and the history of that area.”
At the peak, about 70 masons are on site daily to install the brick and terra-cotta. Rose says that using hand-laid brick not only looks better than precast facade, it is also lighter. “Precast panels would have increased our foundation costs considerably,” she adds.
In addition to the retail and residential units, One Thousand One will feature 185,000 sq ft of indoor and outdoor amenities, including an uninterrupted 169-ft-long central pool flanked by hanging gardens. The pool is located directly above the podium. “The load is about 350 pounds per square foot compared to the buildings, which is loaded to 40 pounds to 60 pounds per square foot,” Rose says. “So there is ample structure [at the podium] to support that.”

The design calls for a large urban facade on Broad Street with lower elevations along other streets.
Rendering courtesy of BKV Group
High-Performance Pumps
In selecting the building systems, Post Brothers took the unusual step of selecting an air-source all-electric heat pump system. Rose notes that because Philadelphia sees so many days of below-freezing temperatures, such systems historically have been avoided in the area. The team, however, selected a new system by ChillMaster that claims to perform down to 5 degrees Fahrenheit. Rooftop units are used to heat water for the towers.
“We wanted something that would be really efficient and easy to maintain over the years,” she says. “So until this technology came out—and it’s quite frankly in its infancy for projects this size—you weren’t able to do it. Now we have an efficient, non-gas-fired electric air source heat pump water plant for the pools, Jacuzzis and the domestic water.
Although the team was able to reduce its need for workers on site through heavy use of prefabrication, Phase 1 still required a peak workforce of about 425. Rose says one of the factors that helped make the project possible was using union and nonunion workers.
“There’s hundreds of workers every day and frankly it being such a large multifamily project, we needed both,” she says. “They are working well together, which has been a great change in Philadelphia over the last five to six years under the new leadership of the local Building Trades Council. Ultimately, they’re getting a lot more residential work from it and we’re able to do much more high-quality projects with a deep bench of contractors.”
With the structure topped out, the team is transitioning to fit-out and finishes. Boarman says that using light-gauge construction is a “self-serving philosophy” for designers because the savings on projects like One Thousand One can be redirected into additional concepts and aesthetics.
“It’s a way to move the money from behind the walls to the furniture and the countertops and the amenities that the residents all experience,” he says.