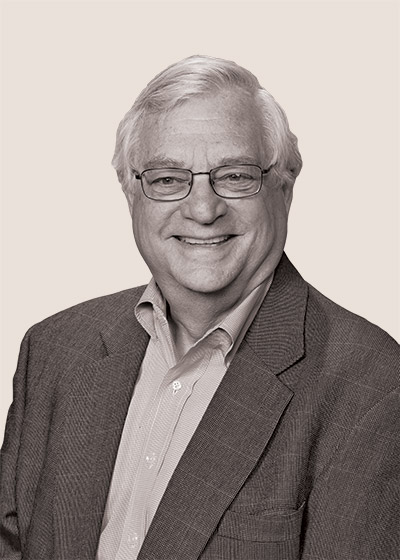
Ken Arnold
Too often, when we investigate safety incidents, we focus on the immediate cause and not the “root cause.” They aren’t the same thing. The U.S. Occupational Safety and Health Administration defines a root cause as a fundamental, underlying, system-related reason an incident occurred that identifies one or more correctable system failures. Finding that cause involves asking tough questions, such as why a
crew did not see the potential danger, or was there inadequate training and discussion of risk by the crew. We also have to ask if the crew was fatigued or hurrying, and if so, why? When we ask those questions, we often find they lead to a discussion of the company or job safety culture.
The National Academy of Construction defines a safety culture as “an all-employee system of shared beliefs, practices and attitudes in an organization that shapes behavior and drives the way in which all work is performed.” It is created by having both a formal safety management system, which addresses key processes and procedures, and a safety climate that defines the employee mindset and behavior.
Here’s one example. It involves a fatal crane accident that occurred because one crane support was too close to a 70° slope and the crane toppled when it swung. The OSHA inspector cited the contractor for not ensuring that ground conditions were firm, drained and graded to adequately support the crane. But was that the root cause? Why did the crew not see the danger? Was there inadequate training? Did the crew prepare for the lift by discussing risks? Were crew members in a hurry, and why?
There is another incident that illustrates my point. It involved refurbishment of facilities on an old offshore oil production platform. On the project, a welder struck an arc to create a new tank nozzle, but connected tanks that had been emptied but had not been de-gassed. The result was an explosion that killed three people.
When the employer was fined for not following welding safety procedures, the CEO said, ‘What do you want? I hired experienced people. They all attended the required OSHA safety courses. I hired a consultant to write a host of safe work practices. I had a construction manager in charge with 20 years of experience. Must I personally watch every worker to make sure they are not violating safety practices?’
The CEO replaced the construction manager and thought he had eliminated the bad apple and the project would be safe. What he did not do was ask the followup questions to understand why the crew acted the way it did, and the answers he would have received would have been illuminating. The workers were in a hurry to finish the job because the job was overbudget, and they knew the CEO did not like such jobs because of how they could limit future work opportunities.
A more detailed investigation revealed other relevant findings. The workers each signed a job safety analysis—the same review they had been using for the past month for many different tasks. The operations manager also signed a required document called a “permit to work” that called for inspecting the area to make sure potential sources of gas were isolated properly—but no one did the inspection.
Also, a fire-watch person was assigned with a gas detector to check at key points in the task as required by the company’s “safe work” practices. But the detector wasn’t functioning and the same fire watch individual was assigned to oversee the work being performed simultaneously in three widely separated geographical areas.
In short, the safety climate on the job was: ‘We need to follow procedures, but we know what we are doing, and these procedures just get in the way of our ability to get the job done. The boss wants us to hurry up and finish.’
Is it a surprise to anyone that on some construction projects we allow this “macho” attitude to prevail? The CEO never realized his actions were a major contributor to the root cause of three deaths and that he failed in his job to establish and maintain a proper safety culture.
Unfortunately, there remain many more leaders in our industry who believe safety begins and ends with OSHA compliance and training, have never been exposed to safety culture concepts and don’t know how to develop and maintain them.
For those interested in gaining a basic understanding of establishing a strong safety culture in construction, see the National Academy of Construction Executive Insight "Safety Culture" series.