Tech Focus
A Place to Study Eternity: Building the Giant Magellan Telescope
September 11, 2024
Tech Focus
A Place to Study Eternity: Building the Giant Magellan Telescope
September 11, 2024The telescope's massive mirrors will be arrayed on a mount inside an 18-story enclosure that can rotate 360° for the best view of the night sky.
Image courtesy GMTO Corp.
The Giant Magellan Telescope will be built on a mountaintop in Chile’s Atacama Desert, a region that is home to many telescopes thanks to its clear skies, dry air and minimal ambient light pollution.
Image courtesy GMTO Corp.
Situated on a remote mountaintop in the Atacama Desert in Chile, the Giant Magellan Telescope will one day allow astronomers to peer further into the universe with a greater degree of clarity than ever before. But siting a highly sensitive instrument with seven massive, 8.4-meter-dia mirrors on a windy peak in one of the world’s most seismically active regions takes careful engineering, especially since the 12-story upper section of the 22-story telescope enclosure will have to rotate 360° with an extreme degree of precision, multiple times a night.
When built, the GMT’s 65-m-tall, 60-m-wide, 4,800-metric-ton enclosure structure will be one of the largest mechanized buildings in the world, able to complete a full rotation in 4 minutes, with movable vents and windscreens to limit wind disturbances and a pair of expansive retractable doors to shield the telescope’s instruments during the day. The $2.54-billion project began back in 2004 with a roughly 30-year estimated delivery and is expected to be completed in the 2030s.
With the telescope’s structural steel enclosure recently passing its final design review [ENR 7/1/24, p.17], the nonprofit Giant Magellan Telescope Organization (GMTO) is now shifting to procurement planning as it prepares to seek bids to build the telescope. But the multimillion-dollar mirrors and many moving parts provide a complex challenge to move from final design to real construction.
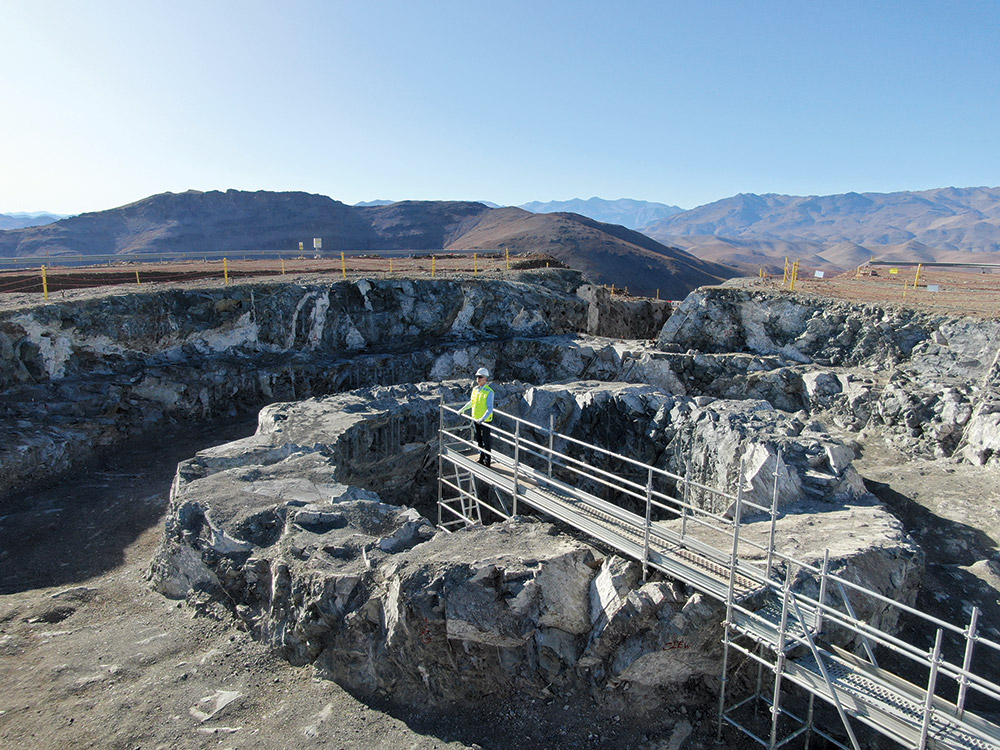
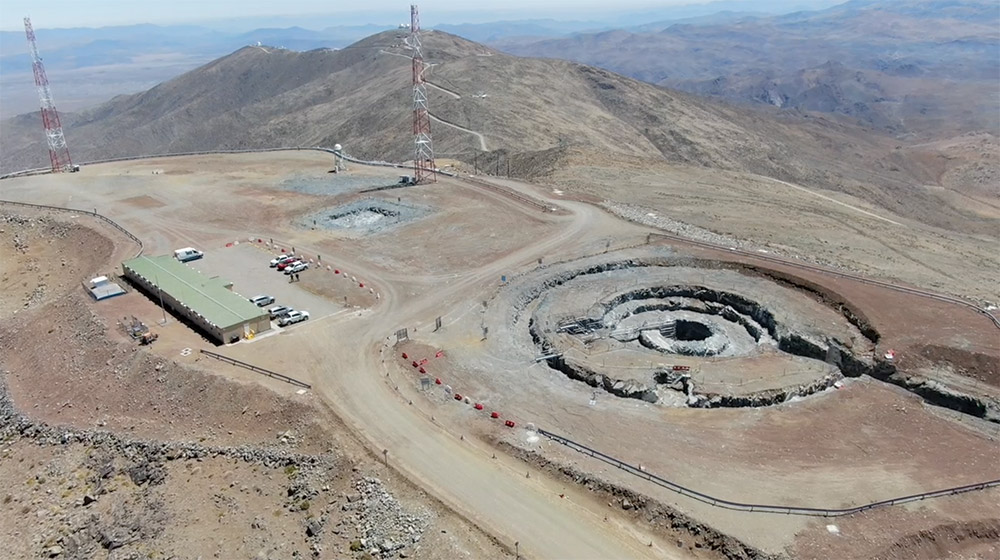
Early work has already begun at the site, including the construction of support structures and some related infrastructure.
Photos courtesy GMTO Corp.
So why build such a massive facility just to gaze at the stars? The functional viewing limitation of any optical telescope is the size of the mirrors collecting the light, explains Dr. Rebecca Bernstein, chief scientist at GMTO. While optical telescopes in orbit around the Earth don’t have to contend with distortions caused by the atmosphere, there is a size limit on how large of a mirror can be sent up. “Right now, the biggest orbiting telescope we can launch is about 6 meters in diameter; it’s hard to get more to space,” she says. “By building bigger on the ground, we can get past that limitation.”
The Giant Magellan Telescope will feature an array of seven mirrors, each 8.4 m in dia for an effective 25.4-m-wide light collection surface, with adaptive optics technology developed in the previous generation of telescopes. Adaptive optics is a relatively new field whereby the focus of the telescope can be minutely adjusted by slightly bending the mirrors themselves. This can correct for atmospheric disturbances, a major limitation of ground-based observation.
When it comes online in the next decade, the Giant Magellan Telescope will be one of a select group of next-generation 30-m-class ground-based optical infrared telescopes, known colloquially in the scientific community as Extremely Large Telescopes (ELT). “Even at this diameter, it is extremely efficient at collecting light. It will have an extremely wide field of view,” says Bernstein. “It can also get incredibly sharp images, about four times the resolution of the James Webb Space Telescope at all times, and for specialty instruments it can be 15 times the resolution. It’s night and day.”


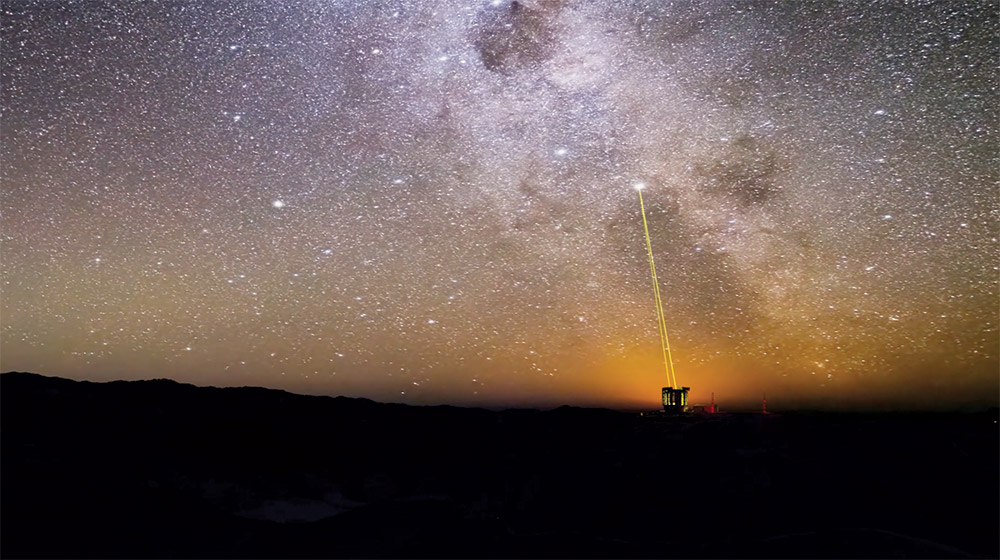
Photos and images courtesy GMTO Corp.
The GMT is designed to meet the next great challenge in astronomy: detecting and mapping planets orbiting other stars, known as exoplanets. “You need extreme adaptive optics to let you see a tiny planet separate from a parent star in its field of view,” Bernstein says. Based on the current pace of developments in the field, she expects the GMT will have the most advanced ability to image exoplanets for at least the first decade of its operation. “In order to understand how our Earth probably formed, you have to understand how other planets have formed. It’s extremely exciting. We have never been able to directly image an [Earth-like planet] before: it’s completely revolutionary science.”
Just because this is uncharted territory for telescope assembly and construction doesn’t mean the team at GMTO has spent the last two decades working from a blank slate. Everything learned from previous generations of telescopes and observatories has been brought in to this project, and that is particularly true with the specific challenges of the GMT’s enclosure structure.

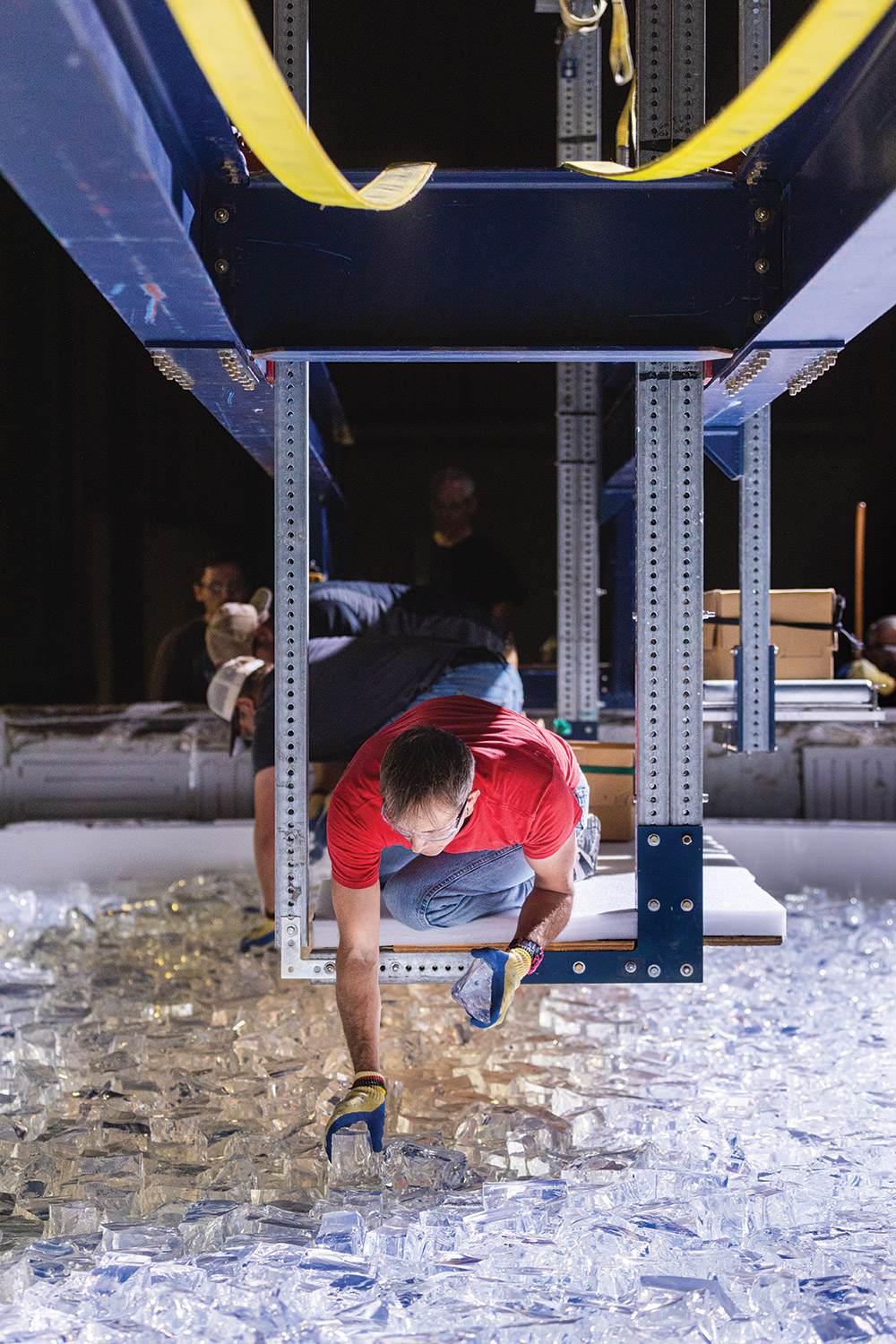
Technicians and scientists at the Richard F. Caris Mirror Lab at the University of Arizona take years to cast and polish each of the seven 8.4-m-dia mirrors that will be mounted in the Giant Magellan Telescope. Work begins with placement of glass chunks on a honeycomb mold in a large, rotating furnace at the lab.
Photos by Damien Jemison, GMTO Corp.
Seismic Shocks and Bitter Winds
While there are large telescopes in seismically active regions such as Chile and Hawaii, use of seismic isolation on the structures is relatively uncommon. But as the telescopes get larger and more elaborate, it’s a concern, says Tom Lorentz, president of North American operations for Spain-based IDOM. The firm is the designer for the telescope enclosure, and applied many lessons it learned from work on earlier telescopes.
“We went through a very competitive process two-and-a-half years ago to select IDOM as final designer for the enclosure,” says Bruce Bigelow, element manager for Giant Magellan Telescope enclosure facilities and site infrastructure. “Part of their portfolio was designs they did for a 4-meter solar telescope in Hawaii, and they had also completed a preliminary design for the European Extremely Large Telescope.” The GMTO is led by an international consortium of 14 universities and research institutions spread across seven countries, most based in the U.S. But the European-led EELT is also being constructed in Chile at the same time in a separate effort. Bigelow says the community of design firms in the telescope community is close knit, and there is a real incentive to share knowledge to advance the science as a whole.
“I don’t know how many ELTs will be built, but there are millions of dollars of glass and instruments in these things—not something they can just replace in six months,” says Lorentz. “If a telescope this size is in a seismic zone, it’s likely to need protection.”
“It’s completely revolutionary science.”
Dr. Rebecca Bernstein, Chief Scientist, Giant Magellan Telescope Organization
In order to meet GMTO’s seismic requirements, IDOM settled on a series of seismic fuses which if set off will allow the telescope mount to sway freely both horizontally and vertically during an earthquake.
“The isolation system is 24 fixed pendulums [which] provide the movement require in a seismic event,” says Nerea Castro, IDOM deputy project manager for the GMT enclosure design. “These components need be very stiff when the telescope is in operation and very flexible when a seismic event occurs.” When the fuses are tripped by vibrations, the pendulums will allow the telescope to move freely up to 700 mm. This base isolation system prioritizes protecting the telescope mount and its mirrors. The enclosure structure itself is not base-isolated, but finite element analysis performed by IDOM on seismic risks did lead the team to stiffen up the enclosure, Lorentz says.
Earthquakes are not the only threat. The mountaintop site was chosen for the thin, dry air of the region, but winds can cause turbulence over the telescope, distorting the images it captures or even damaging the mirrors. During the day, the telescope is protected by a giant pair of retractable doors, similar to those used in stadiums. During operation at night, the interior of the enclosure has to be close to the same temperature and humidity of the outside air for the best image quality, but it must also have some way to mitigate wind.
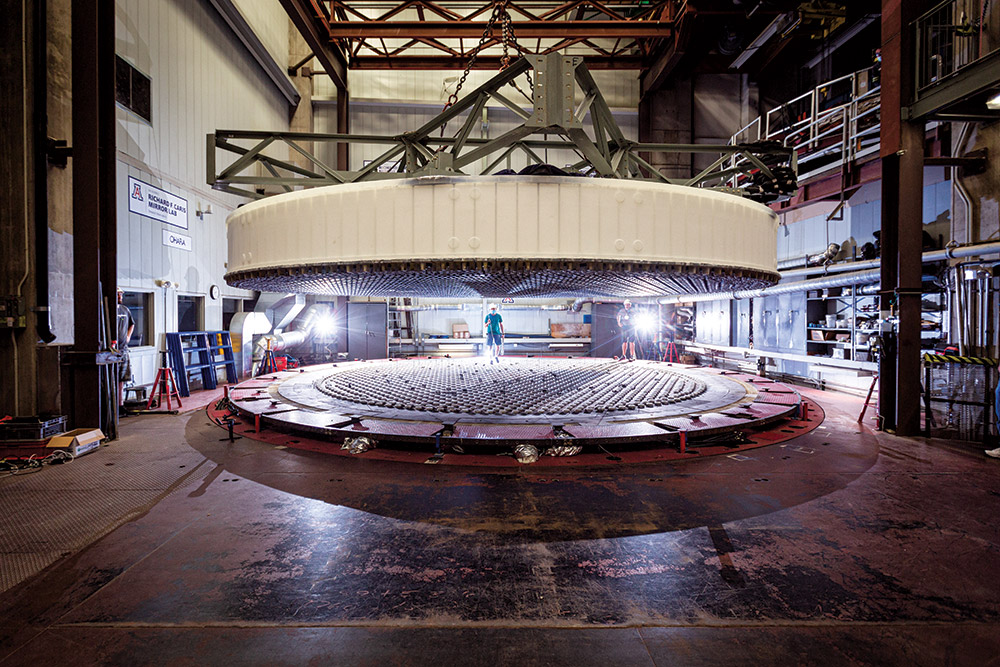
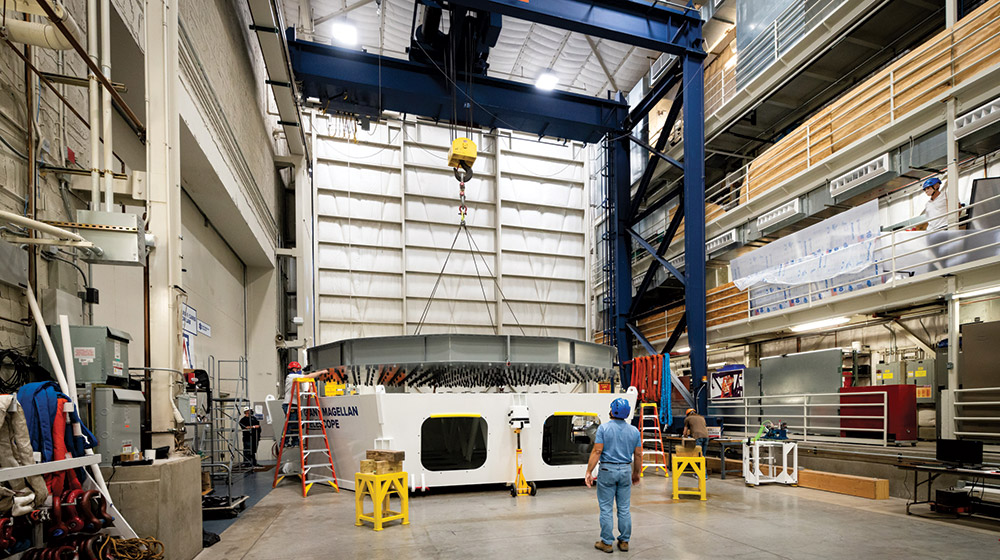


A rapidly spinning furnace forces the heated glass to cast in the exact parabolic shape necessary for the telescope’s optics. The heating and cooling process for each mirror takes more than a year.
Photos by Damien Jemison, GMTO Corp
“For the Giant Magellan Telescope, we did some preliminary design with arrangement of the shutters and analyzed the best positions for wind vents to minimize turbulence,” says Castro. A preliminary design called for roughly 30% of the enclosure’s surface to be open during operation. This was further refined by IDOM, which switched to more standardized vent designs, eventually settling on 92 vents on the upper enclosure to minimize the effects of wind.
“We wanted 30% of the wall area of the upper enclosure to be able to be opened, but we also want to decide how much to open those wind vents based on current wind direction and speed,” says Bigelow. In addition to finite element analysis conducted by IDOM using OpenSees, fluid dynamic modeling of wind performance was done by engineers at aerospace giant Boeing as well as at Canada-based engineer RWDI. “By having two different analysts running two different computational fluid dynamic tools on the same models, we were able to compare the results,” explains Bigelow. In addition to leading to the publication of several technical papers, Bigelow says that the models showed the site originally selected for the telescope was not the optimal location on the mountaintop to minimize wind loads. This in turn led to a slight relocation of the telescope before foundation excavation work began.
“The dominating cost of ground-based telescope is not mirrors or instruments—it’s the enclosure.”
Buell T. Jannuzi, Director, Steward Observatory
The fluid dynamics modeling also confirmed that it was worth the extra effort to fully enclose the lower portion of the telescope enclosure. Early designs had the area around the pier beneath the telescope mount open to the outside air, as in done with smaller telescopes. But Bigelow says calculations on wind loads showed this provided no benefit when scaled up to the size of the GMT, allowing the team to justify enclosing the lower section of the enclosure for structural and seismic reasons. “Before we did the fluid dynamic modeling, we didn’t have any way to demonstrate that the enclosed lower structure was superior from a design perspective,” he explains.
When the retractable doors are open, IDOM saw a further need to shield the mirror array from sudden gusts of wind. The solution is a custom-design, retractable windscreen devised by Castro, since a potential supplier said it wouldn’t be able to meet the requirements with its own off-the-shelf windscreen. “We ended up with a system composed of composite panels, about 25 meters in span, and they need to be able to follow the telescope’s elevation angle, so when its fully deployed its like 25 meters high,” says Castro. The supplier’s system could not contend with the seismic requirements or deformation due to wind, so Castro’s innovative windscreen is now in the specification.
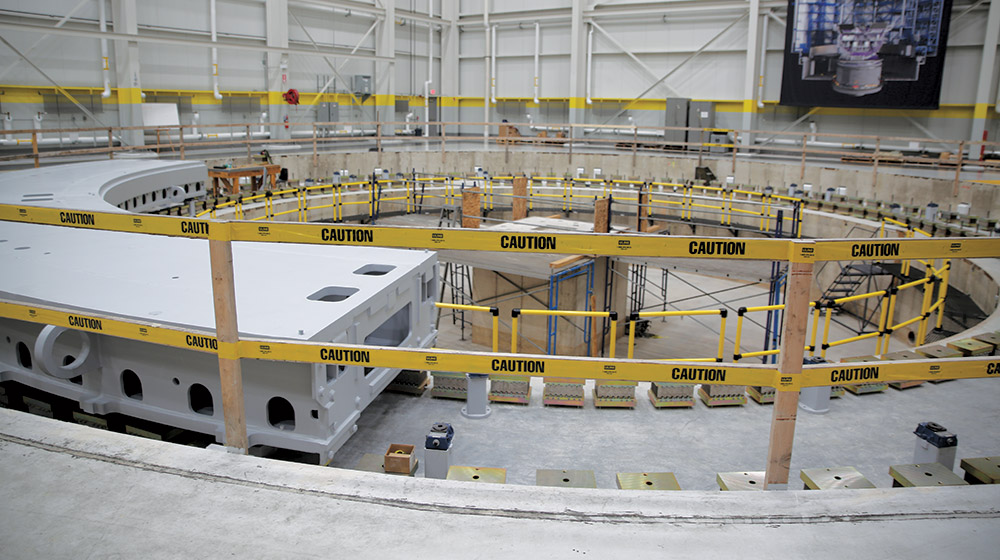

The telescope mount test facility at Ingersoll Machine Tools’ Rockford, Ill., facility will include some of the leaf-spring shock absorbers that form part of the seismic dampening system intended to protect the telescope in an earthquake.
Photos by Jeff Rubenstone/ENR
Mirror, Mirror
Fabricated at the Richard F. Caris Mirror Lab at the University of Arizona, the GMT’s mirrors are cast from melted glass and are coated with an extremely thin layer of aluminum once polished. It’s crucial for the mirrors to be as smooth and uniform as possible to avoid distortions in imaging, a tricky goal, given that they are not symmetrical, explains Buell T. Jannuzi, head of the department of astronomy and director of the Steward Observatory at the University of Arizona. The mirrors are cast from glass bricks over a honeycombed backing structure. This method has been used and refined by the lab over several decades of mirror manufacture. A rapidly spinning furnace allows for the glass to be evenly distributed over the mold in the desired parabola shape as it melts. The honeycomb structure also drastically reduces the weight of a mirror.
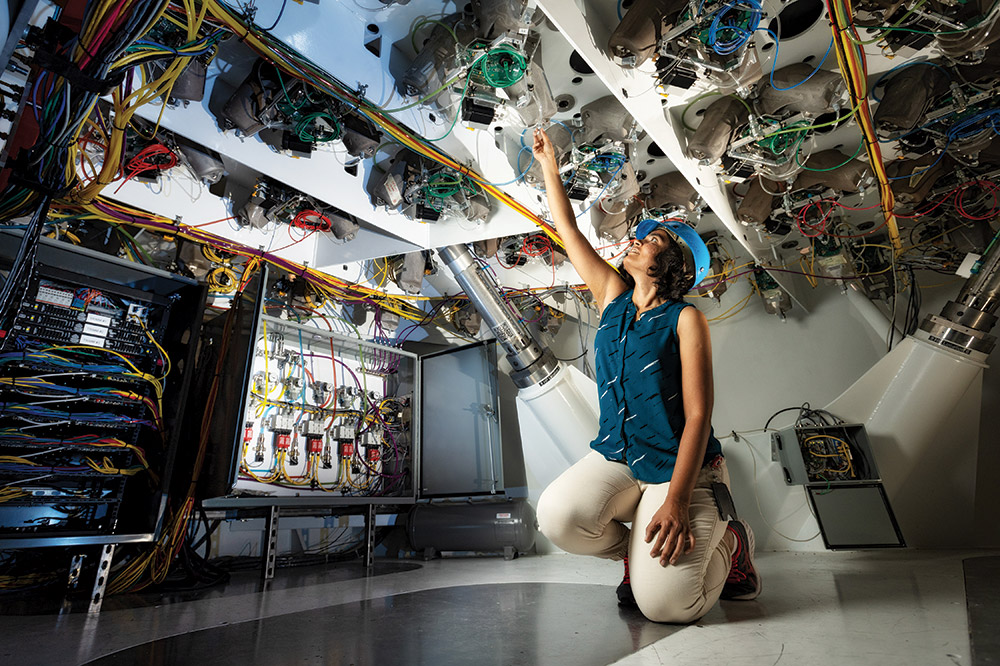
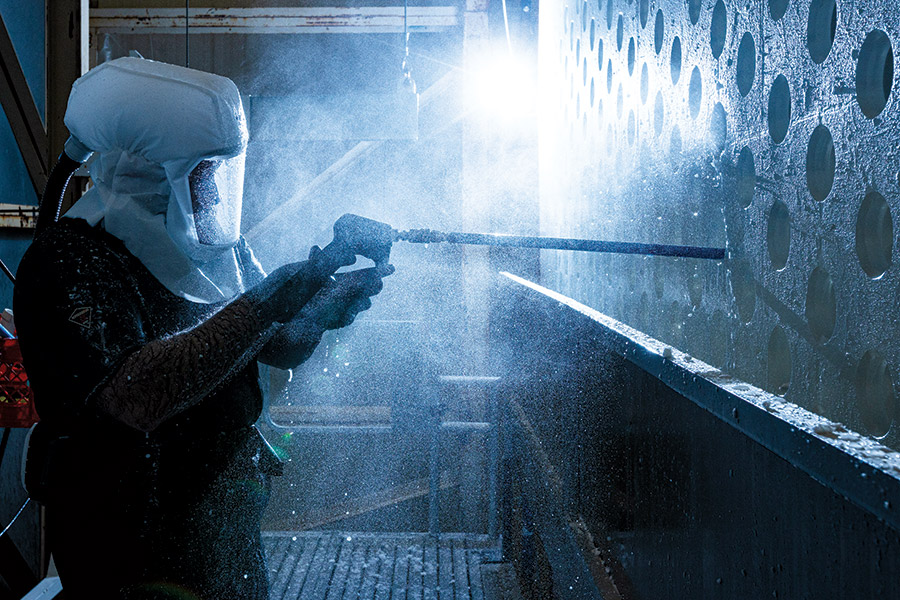
The mirrors are cast against a honeycomb backing structure (right) which makes them lighter than if they were solid glass. Adaptive optics equipment will let scientists subtly bend the mirrors for minor adjustments (above).
Photos by Damien Jemison, GMTO Corp.
“There are currently two ways to collect an aperture as big as a 25-meter or 30-meter telescope, and one way is with a lot of smaller segments,” says Jannuzi. The seven, 8.4-m mirrors of the GMT will be arranged like six flower petals around a central mirror. Each of the mirrors weighs approximately 18 metric tons.
“We are the only place in the world that makes mirrors larger than 4 meters in diameter,” notes Jannuzi. It takes about 14 months to cast one of the mirrors, followed by a polishing process that can take years, he says. “We start off with a coarse slurry or grit, like the texture of sandpaper. We have to be fairly conservative in this process, because if we take too much glass off we can’t put it back on,” he says.
Because they are in an array, each mirror must be polished non-symmetrically to work properly together. “It is a very slow process. We’re going to coat [each mirror] with aluminum, but at a fraction of the thickness of a human hair,” says Jannuzi. “The final surface of each mirror has to be accurate to 20 nanometers.” For comparison, this is equivalent to a surface the size of North America not having a deviation of more than 2 in., explains Jannuzi. The mirror lab finished casting the seventh and final mirror of GMT in October 2023, making it the 24th giant mirror that the mirror lab has produced since it was established in the early 1980s.
“We don’t know if we’ll ever reach the limit of our capacity to learn and improve, but [gmt] Pushes us.”
Jeff Kimberly, COO, Ingersoll Machine Tools
Despite the cost and effort involved in producing the mirrors, Jannuzi says they’re not the biggest expense in a telescope. “The dominating cost of ground-based telescope is not mirrors or instruments—it’s the enclosure. Having a building as small as you can possibly make it is really important,” he says. Since the building has to rotate, using adaptive optics and a creative arrangement of primary and secondary mirrors has reduced the overall size needed for GMT’s enclosure. For all the effort that goes into erecting a 22-story rotating building, the GMT will gather an amount of light that would have required a much larger enclosure in earlier generations of telescopes.
The mirrors aren’t the only parts of the telescope that have entered the fabrication stage. While a contractor has not yet been selected for the enclosure, work is already progressing on fabricating components of the telescope’s mount. These carefully milled segments of steel will form the axial tracks that allow the telescope to spin freely within the structure along multiple axes, tilting and repositioning with microscopic precision to aim at just the right spot of the night sky.
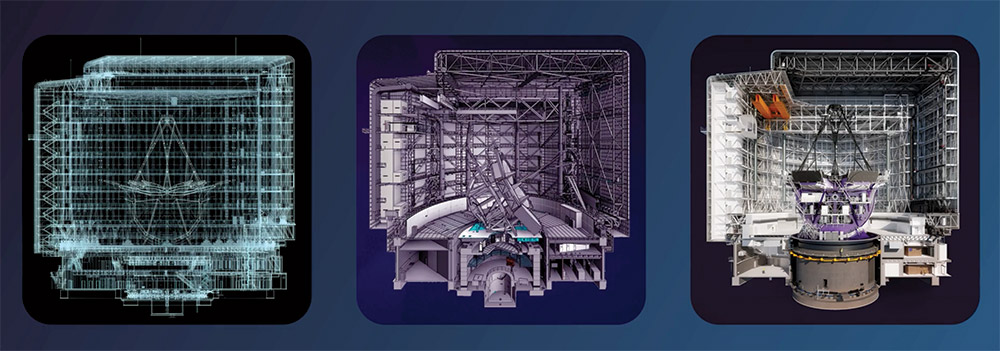


The telescope’s seven mirrors are arrayed like the petals of a flower, directing light up to secondary mirrors and down to an instrument cluster below an opening in the central mirror.
Images courtesy GMTO Corp.
When comparing to other moveable structures such as stadiums, “we’re literally orders of magnitude higher in precision, because the mount has to be this stable platform so the optics can resolve science objects that are billions of light years away,” explains Keath Beifus, senior mechanical engineer with GMTO. Beifus previously worked at fabricators of precision-machined components before joining GMTO. “This is the first project that I’ve ever worked on that has millions of pounds of steel where we talk about micron precision,” he says. “Usually you would be talking thousands or tens of thousands of pounds with millimeter precision. We literally talk in micron precision when we’re talking about the Giant Magellan Telescope.”
Rockford, Ill.-based Ingersoll Machine Tools is leading the effort to produce the 12-story-tall, 2,100-metric-ton telescope mount, in collaboration with German-based design partner OHB Digital Connect. Ingersoll recently expanded its manufacturing facility to house a five-axis milling machine capable of nanometer-accurate milling for GMT. It’s the largest milling machine of its kind in North America.
The machining required for the telescope mount is demanding but doable, says Jeff Kimberly, chief operating officer at Ingersoll Machine Tools and the company’s program manager for the GMT. “The azimuth tracks that make up the starting layer of the telescope mount—eight tracks for a full circle—are precision-machined for one constant flat surface for hydrostatic bearings to run on, with a radial inner way for the mount to roll on to hold in an axial location,” explains Kimberly. This is how the mount can not only rotate, but also can tilt the telescope from 95° to 30° on a 10-m-dia C-shaped steel ring. The entire mount will rotate on hydrostatic bearings, essentially a thin layer of oil.
Kimberly says the requirements of GMTO are driving Ingersoll toward new innovations. “We don’t know if we’ll ever reach the limit of our capacity to learn and improve, but [GMT] pushes us.”

With the final design now complete, GMTO is preparing to seek a contractor to build the telescope’s enclosure sometime next year.
Image courtesy GMTO Corp.
The Final Frontier
The momentum in a 30-year project can be hard to perceive, but GMTO’s Bigelow sees the next milestone in starting conversations with contractors early next year with an eye on issuing a request for proposals for the telescope enclosure sometime later in 2025. And that will begin a yearlong evaluation period to select the right contractor for the job. There are also crucial funding deadlines coming up, including an expected major grant from the National Science Foundation.
All of the design preparation only gets you so far, says Bernstein. “We can test individual parts and simulate how the whole thing works together as much as possible, but it will still be an exciting series of steps to see it all integrated and built on the site.”
The text of this article has been updated to reflect small clarifications and corrected photo credits.