2024 Southwest Best Projects
Best Manufacturing — Kohler Vikrell Manufacturing Facility
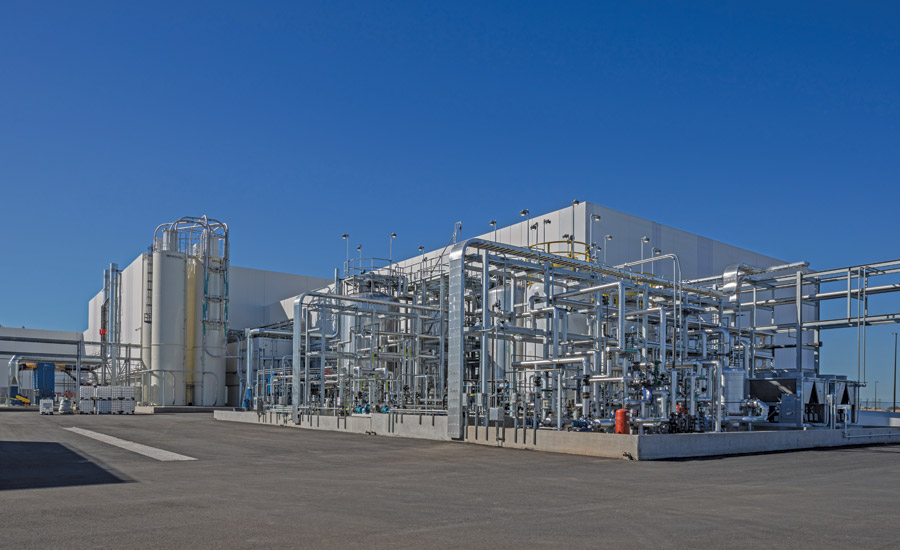
Photo courtesy Mortenson
Kohler Vikrell Manufacturing Facility
Casa Grande, Ariz.
BEST PROJECT
Submitted by: M.A. Mortenson Co.
Owner: Kohler Co.
Lead Design Firm/Civil: Ware Malcomb
General Contractor: M.A. Mortenson Co.
Structural Engineer: TLCP Structural Inc.
MEP Engineer: Piping System Engineering
Mechanical/Electrical Engineer: Kraemer Consulting Engineers PLLC
Process Engineer: Barry-Wehmiller Design Group
Steel Erection Subcontractor: BZI Steel
At 1 million sq ft, this manufacturing facility was designed and built to produce and distribute the owner’s Sterling Vikrell bath and shower fixture lines. The project also represents one of Kohler’s largest capital investments in its history.
But delivering such a project on an undeveloped desert site required innovation, teamwork and trust. Scope of work included advanced manufacturing facilities, an ancillary warehouse and supporting office space.
Contractor M.A. Mortenson Co. broke ground on construction in early 2021, and the plant reached substantial completion in December 2023, on time and within budget.
To lessen the impacts of supply chain shortages during the early portions of the project, the design-build team decided to flip the traditional design/procurement processes, moving procurement of certain long-lead products to before the design was finished.

Photo courtesy Mortenson
Roof joists, for example, had a lead time of one and a half years at the time. In response, the design-build team ordered the facility’s roof joists as soon as possible, even before the project’s structural design had been completed. Then, the rest of the structure was designed around those joists.
Manufacturing facilities like this would typically require a significant amount of aerial work during steel erection, but instead, steel erection subcontractor BZI Steel’s process involved assembling roof decking and trusses on the ground.
The prefabricated assemblies were then hoisted into place using BZI’s MezzMaster, a specialized forklift. The Kohler project was the first to utilize the MezzMaster.
To ensure delivery of a modern, industry-leading facility, Kohler collaborated with contractor M.A. Mortenson Co., lead designer Ware Malcomb and process engineer Barry-Wehmiller Design Group to design the facility’s process components with the goal of creating more efficient systems.

Photo courtesy Mortenson
The team worked with Kohler’s engineering, construction, design, robotics and automation departments to evaluate current processes and identify avenues for process evolution. In all, this effort actually took longer to complete than the building’s overall design.
Mortenson team members also studied the company’s current Huntsville, Ala., manufacturing facility for inspiration.
One of the innovations to come out of that effort was an optimized dust control system. Shower and bathtub production generates dust, and if not well-controlled, the dust can clog and damage machinery and affect air quality for workers. The dust collection system was integrated throughout the production areas, constantly collecting dust so that it didn’t settle in or on machinery or on the floors.
Another process innovation delivered by the project team was a flash conveyor that runs below all presses and collects flash, or the excess material trimmed off of tubs and shower surrounds, and then carries it out of the production area. The conveyor was designed to run through a 12-ft-high tunnel below the presses, enabling easy access for repairs and maintenance.