ENR Northwest 2024 Best Projects
Best Manufacturing, Award of Merit Safety: 25K ISO 4 Cleanroom Expansion

Photo by Alfonson Diaz/MWH Constructors
25K ISO 4 CLEAN ROOM EXPANSION
Beaverton, Ore.
BEST PROJECT, Award of Merit
Submitted by: MWH Constructors Inc.
OWNER: Analog Devices Inc. (ADI)
LEAD DESIGN FIRM: Corbin Consulting Engineers
GENERAL CONTRACTOR: MWH Constructors Inc.
CIVIL/STRUCTURAL ENGINEER: Mackenzie Inc.
MEP ENGINEER: Corbin Consulting Engineers
ARCHITECT: Advanced Technology Group (ATG)
SUBCONTRACTORS: Pence/Kelly Concrete LLC; EC Electric; Envision Controls Engineering; Streimer Sheet Metal Works Inc.; Apollo Mechanical; Ocean Park Mechanical
As part of a comprehensive $1-billion multiphase expansion of Analog Devices’ semiconductor factory to enhance its manufacturing capabilities, this $115-million project adds 25,000 sq ft of clean room capacity, bringing the client’s total manufacturing space up to 118,000 sq ft.
The clean room minimizes particulates, such as dust, microbes, aerosol particles and chemical vapors to safeguard active manufacturing on the level above.
Scope of work required converting a former warehouse space, placing a new concrete slab and building a mezzanine floor above the planned manufacturing area to support recirculating air handler units, secondary production tool equipment and utility connections for production equipment on both levels.

Photo by Alfonson Diaz/MWH Constructors
Since the original facility was built in 1980 and was not ready to receive tools and equipment, the owner issued $33 million in early release packages to prepare the site.
With an active manufacturing space right above the construction area, the project team implemented advanced measures such as temporary structural supports and sound-dampening materials to prevent disruptions in both areas. Crews monitored structural stability, maintained life safety systems and protected the existing manufacturing space.
During design, the construction team’s feedback was crucial in identifying risks and developing mitigation strategies, allowing for work sequencing without unnecessary shutdowns. When shutdowns were necessary, the team planned for months to create a detailed micro schedule. Hundreds of tasks were planned in 15-minute increments over 12-hour and 36-hour periods to allow for quick assembly, efficient component installation and to minimize disruptions. The project team also had to complete the clean room in just 12 months to accommodate a production tool installation program.
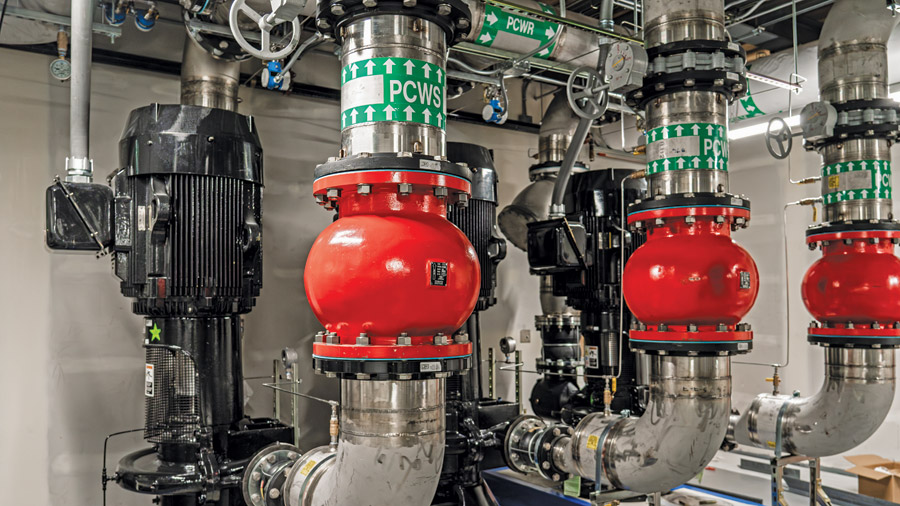
Photo by Alfonson Diaz/MWH Constructors
To relocate existing utilities to make room for the new project, the team mapped them all out before developing a phased relocation plan that minimized downtime and maintained operational continuity. New permanent systems were built to reroute utilities, which ensured uninterrupted service. Then after completing the tie-ins, the old systems were removed.
Across nearly 300,000 worker hours, the project team logged an OSHA recordable incident rate of 1.3 and had zero lost-time accidents. With the implementation of project-specific safety programs, the team conducted in-depth work plan reviews weeks before any scheduled work to identify and mitigate potential hazards ahead of time. Daily safety incident prevention plans were developed for every activity and required thorough review and sign-off from the contractor’s safety department and the client.
Extensive pretask planning and workspace preparation also protected some critical areas. When crews had to work near unprotected hazardous piping systems, engineered controls were used, such as encasing hazardous piping with hard barriers, wrapping with plastic Visqueen and using drip pans to catch potential chemical leaks. Equipment emergency shut-off switches were safeguarded as well.
Delivered in July 2023, the new clean room is double the original capacity and received ISO-4 certification one month ahead of schedule, just six months after the mezzanine structure was finished. The project was completed $3.5 million under the original GMP budget.