Best of the Best Winners
Best Manufacturing: United Therapeutics cGMP Warehouse

The logistics facility uses a combination of onsite solar and geothermal power with battery backup for its energy needs.
Photo courtesy DPR Construction
United Therapeutics cGMP Warehouse
Durham, N.C.
Manufacturing
Region: ENR Southeast
Submitted by: DPR Construction
Owner: United Therapeutics
Lead Design Firm: Hanbury
General Contractor: DPR Construction
Civil & Structural Engineer: NV5
MEP Engineer: Affiliated Engineers Inc. (AEI)
Landscape Architect: Surface 678
Building a climate-controlled warehouse and logistics facility for United Therapeutics in North Carolina’s Research Triangle was a matter of power management and careful planning. The facility is powered by onsite geothermal wells and solar panels, with Tesla battery Megapacks serving as a self-contained backup microgrid. As a production facility for pharmaceutical products, consistent power was a must for 24/7 temperature control, a hard target for the project’s ambitious zero-carbon goals.
The design-build project team was tasked with ensuring every watt used by the facility is offset by onsite generation, with no carbon credit purchases to meet the zero carbon goal. “From the earliest site planning and selection to the energy modeling, to passive strategies of insulation, glazing and everything under the sun, we utilized all the tools available to reduce the energy consumption,” says Chris Smalls, principal and science market leader at design firm Hanbury, who led the design team.
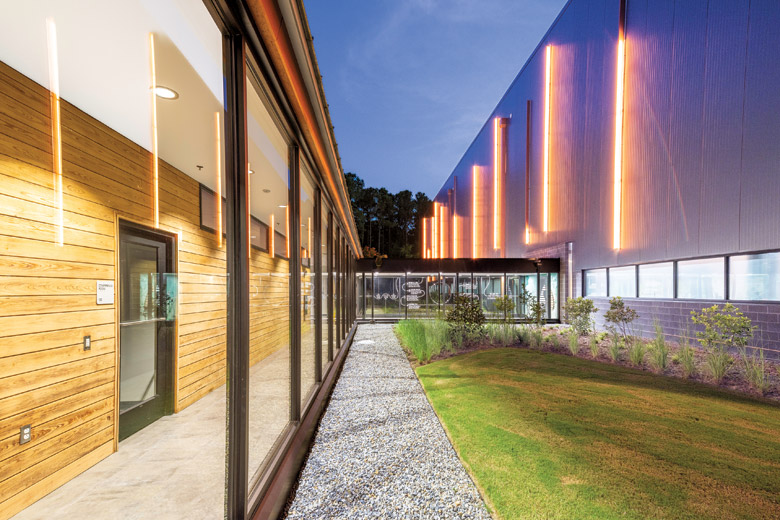
Photo courtesy DPR Construction
The site’s solar installation comprises 1,186 475-W panels tied into seven 62-kW inverters, expected to generate a combined 767 MWh per year. The geothermal installation called for 40 vertical bores, 6 in. in dia and 100 ft deep. Tesla Megapacks provide 6.2 MWh of onsite storage, allowing for two days of off-utility power as needed.
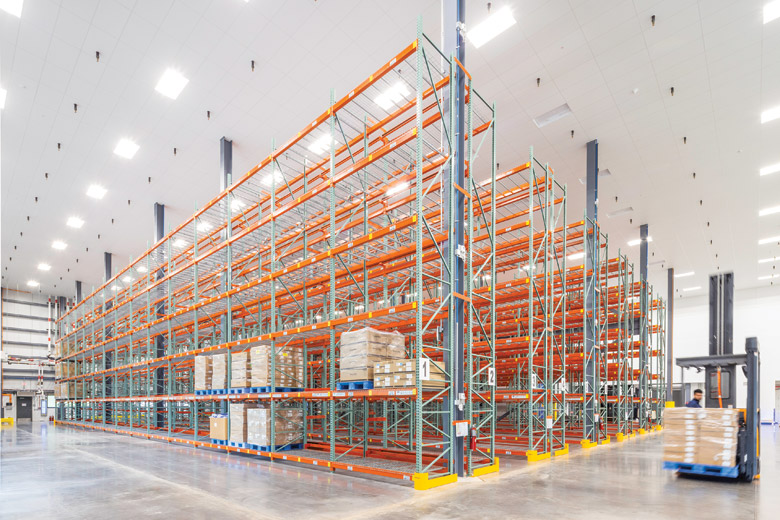
Photo courtesy DPR Construction
All of this is in service of keeping the facility to the stringent requirements of the U.S. Food and Drug Administration’s Current Good Manufacturing Practice regulations, which sets strict climate control standards for the interior spaces, especially in the cold storage room, where pharmaceutical products must be kept at a near-constant temperature. Smalls says the facility has outperformed these requirements, and all without compromising the owner’s zero-carbon goals. “Everything is performing close to design, even better in some cases.”
The facility is now on track to receive LEED Gold, LEED Zero Carbon and EnergyStar certifications.