Manitowoc Bets Its $30-Million Supercrane On World’s Nuclear-Power Renaissance
Last fall, Manitowoc Inc. was flying high. The 107-year-old fabricator had just wrapped up two years of factory upgrades worth roughly $70 million and was popping out construction cranes for record sales and backlogs worth more than $3 billion. It also had started building its biggest crane ever—the Model 31000—a massive, 2,500-ton rig with a $30-million price tag.


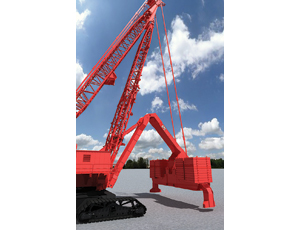
Then came the Lehman Bros. collapse, “the beginning of this complete debacle,” said Glen Tellock, CEO, speaking in his Manitowoc, Wis., office on Sept. 14—exactly one year after the banking crisis. By the start of this year, as new construction dried up, crane owners were canceling orders left and right.
But work on the 31000 crawled ahead. It is the largest mobile crane built from the ground up by a full-line manufacturer, users say, and among a new generation of supercranes built to tackle a renaissance of nuclear power projects around the globe. “There is a strong undercurrent in activity for nuclear plants in the U.S.,” says Alan Ashlock, who bought one of the two 31000s being built. “It is probably two years out, but everybody believes it is coming back.” The U.S. Nuclear Regulatory Commission has received permit applications for 28 new reactors, and 22 are actively under review, reports Platts (like ENR, a unit of McGraw-Hill Cos.). Globally, 53 are under construction—16 in China alone—and 90 are scheduled to come online in 10 years. About 200 more may be built further out.
Today’s powerplants, assembled more in modules rather than fabricated on-site, require heavier lifting than ever before. And while the hard and soft costs of using supercranes like the 31000 are enormous, their sheer musclepower comes with immense economies of scale. The 31000 will ship to the jobsite in about 125 truckloads, and it will take about three weeks to assemble. But it will be able to pick up, carry and place heavy modules hundreds of feet beyond tricky obstacles.
Ashlock, who is president of Orlando-based Crane Rental Corp., says the 31000 also will find work in chemical plants and refineries that need continual maintenance because the 31000’s long arms can hoist bulky, heavy objects above existing piping and out over long distances. With a load-moment rating of 252,000 ft-kips, the 31000’s main boom will reach to 345 ft into the sky. A 335-ft-long luffing and 79-ft fixed jib also are available.
“This particular machine has a lot of advantages,” says Bob Shirey, president of Newberry, S.C.-based Bulldog Erectors, which ordered the first machine at last year’s Conexpo-Con/Agg show (ENR 3/24/08 p. 13). “It also has a manufacturer that is worldwide standing behind it.”
Balancing Act
More than 70% of Manitowoc’s business now goes to rental firms, and what sold them on the 31000 is its ease of use. Unique to the rig is a “floating” counterweight that extends from 27.5 ft to 95 ft behind the machine via a giant rack-and- pinion assembly. Controlled by computer, the “stinger” guides articulating arms that balance the rig’s load moment in real time as the load changes on the hook.
This Variable Position Counterweight (VPC) also allows the crane to “walk around” the job while fully loaded. “It is almost as important as what the crane can pick,” says Ashlock. Shirey adds that it can lift 200-ton modules at a 340-ft radius—longer than the length of a football field.
Manitowoc designers did not use hydraulic rams to actuate the VPC because of the rams’ sensitivity to heat, which could throw off the crane’s balance. They are looking at using the VPC on other cranes. Tellock says, “I think it could be something that really has a future.”
Previous counterweight designs, such as Manitowoc’s Ringer and Max-Er, attached to existing cranes, boosting lifting capacity but restricting mobility. “It was really what could we do to eliminate the [counterweight] wagon,” says John Lanning, chief engineer. Still, the 31000 is a mix of old and new. It rotates on a 40-ft-dia. roller pad like the Ringer but has four tracks that oscillate to keep them flat and off their “toes.” The crane spawned 18 patents. “I think [it] is so innovative, it will sell itself,” says Ashlock.
The 31000 is one of the world’s largest “pick and carry” crawler cranes but not a record-breaker (ENR 10/15/07 p. 10). Manitowoc may build a larger crane, but until construction requirements change, the low volume may not justify the engineering. “If you could sell one a year, you would be fine,” Tellock explains.
Ashlock’s crane will soon undergo months of load testing while Manitowoc builds Shirey’s crane. Why build out of sequence? The parties are sketchy on answers but hint competition may be a factor. “Let’s just say there is an opportunity for manufacturing to make some enhancements,” says Shirey. He expects to receive his rig by the fourth quarter of 2010. Ashlock says his will follow in early 2011.