Best Projects
Modoc Medical Center Replacement Facility

Photo by Technical Imagery Studios
Modoc Medical Center Replacement Facility
Alturas, California
Award
KEY PLAYERS
OWNER: Last Frontier Healthcare District, dba Modoc Medical Center
LEAD DESIGN FIRM | STRUCTURAL ENGINEER: Nichols, Melburg & Rossetto
GENERAL CONTRACTOR: Swinerton
CIVIL ENGINEER: Pace Engineering
MEP ENGINEER: Contra Costa Electric
MECHANICAL ENGINEER: Frank M. Booth Inc.
SUBCONTRACTORS: Applied Restoration; Camblin Steel Service Inc.; Coffey Building Group; Cosco Fire Protection; Contra Costa Electric Inc.; J.B. Steel Inc.; Kodiak Union Roofing Services Inc.; Modern Building Inc.; U.S. Glass Inc.
Located in rural northeastern California, the three-building, 28,000-sq-ft hospital complex is a critical access facility serving a 4,500-sq-mile area. The remote location and its harsh climate meant that qualified local craft labor was in short supply. Early outreach to union trades and the offering of incentives led to the formation of a unified, cohesive team eager to contribute to the success of such a major undertaking.
Related link: ENR California Best Projects 2021
(Subscription Required)
An initial cost estimate was significantly higher than the owner’s target cost, driving the team to develop collaborative solutions to meet the budget without compromising the patient experience, staff workflow or efficiency. Because rural hospitals often have to do more with fewer resources than their urban counterparts, Modoc Medical Center’s departments are strategically coordinated. For example, colocating the emergency department with the inpatient care unit accommodates cross support that can be especially important during night shifts when few staff members are on duty. The entryway seamlessly integrates the front lobby space of the acute care hospital with the adjoining rural outpatient health clinic, connecting the two buildings as one contiguous space resulting in a simplified flow for patients.
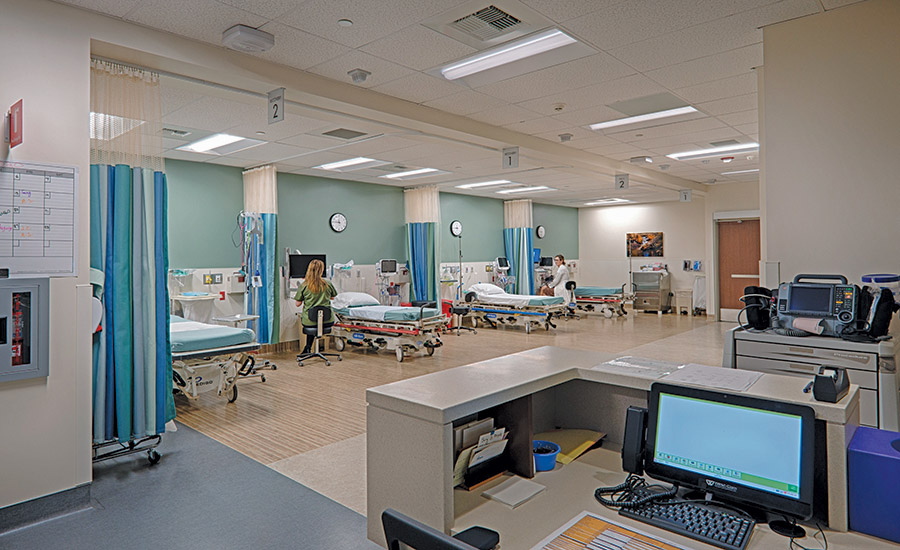
Photo by Technical Imagery Studios
The team also found ways to use the region’s unique features to the project’s advantage, such as tapping a local geothermal hot-water loop as the primary source of hydronic heating. To accommodate the area’s cold climate, the team designed a cost-effective ice melt system for the exterior sidewalks and incorporated protection for outside utilities subject to freezing. Exterior skin and roofing were selected to provide long-term value and energy efficiency.
To ensure quality and craftsmanship, key construction team members joined designers to identify and resolve field issues before they became costly, time-consuming problems. During construction, subcontractors were required to conduct their own quality-control process before requesting inspections.
Preinstallation meetings reviewed each definable feature of work. This process helped the project reach substantial completion with few outstanding issues to be resolved prior to final acceptance by state health regulators.