2023 MidAtlantic Best Projects
Best Project Manufacturing: PDC Machines Manufacturing Facility

Photo courtesy of Gilbane Building Co.
PDC Machines Manufacturing Facility
Souderton, Pa.
BEST PROJECT
Submitted By: Gilbane Building Co.
Owner: CBRE Real Estate Services Inc.
Lead Design Firm: D2 Architects LLC
General Contractor: Gilbane Building Co.
Structural Engineer: O’Donnell & Naccarato
Subcontractors: Pusey Electric; PDM Constructors; Component Assembly Systems Inc.; AT Chadwich; Central Metals; Berlin Steel; Paul Rabinowitz Glass Co.
For the fit-out of PDC Machines’ 150,000-sq-ft manufacturing facility, the project team consolidated three buildings into one with the goal of creating a facility and office space that overlooks the client’s operations. The building was designed to support the operation of cutting-edge technology that uses hydrogen gas compression to produce zero-emission fuel cells.
Because the facility originally lacked natural light, the design team cut in 65 additional windows and designed a grand main lobby—including a monumental staircase—with a mix of materials and textures that blend industrial elements with modernity. The additional windows brought in an ample supply of natural daylight, which also served to cut electric costs.

Photo courtesy of Gilbane Building Co.
With an occupied site, the contractor maintained the safe separation of construction activities by building a temporary 40-ft-high barrier between owner-occupied spaces and project construction spaces. The team also included air scrubbers throughout the facility to maintain safe working conditions.
During the first of two phases, Gilbane worked in tandem with the core and shell contractor, although having both teams in a constrained space created a challenging environment. To facilitate the process, the contractor communicated continuously with all teams involved and synchronized certain tasks such as concrete placements to save time.
At the project’s start, the client noted an interest in expediting the schedule but did not yet define dates. As a precaution, Gilbane made an allowance in the GMP, which ended up totaling $450,000.
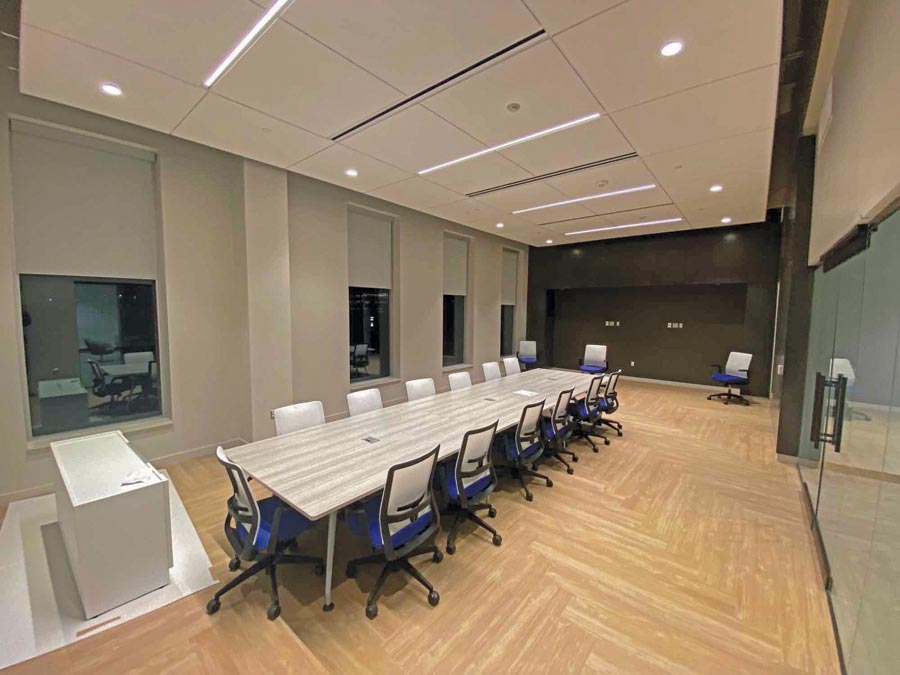
Photo courtesy of Gilbane Building Co.
The second phase was originally set at 25 weeks. With 18 weeks left on the schedule, the client requested an adjustment, seeking to move into the space in 10 weeks. To meet this challenge, the contractor expedited finish trades, which allowed the client to move into a safe environment. While waiting for finishes, the team developed other solutions. To mitigate a delay on the project’s oak stair treads, which were critical to the monumental staircase as a life safety egress, the team put in temporary treads that had a similar aesthetic. When the finished stair treads arrived, the team installed them during off-hours, careful not to impede normal work and operations of the business.
When parts were delayed for motor starters in the facility’s testing area, the owner’s electrical engineering group provided spare parts so the team could install electrical equipment ahead of schedule because supply chain delays would have extended work past milestone turnover dates. When the permanent parts came in, the electrician installed them during the client’s off-hours.
The GMP allowance was a key factor in keeping the 11-month project on budget during the schedule change in the second phase, enabling work to finish within budget and ahead of the contract schedule.
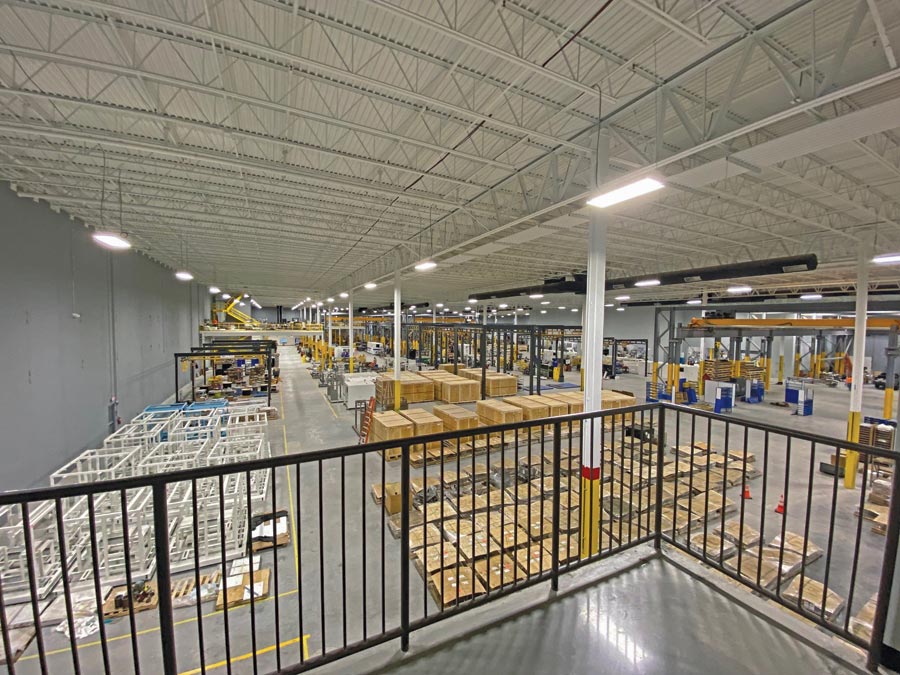
Photo courtesy of Gilbane Building Co.