2023 MidAtlantic Best Projects
Best Project Sports/Entertainment: CFG Bank Arena
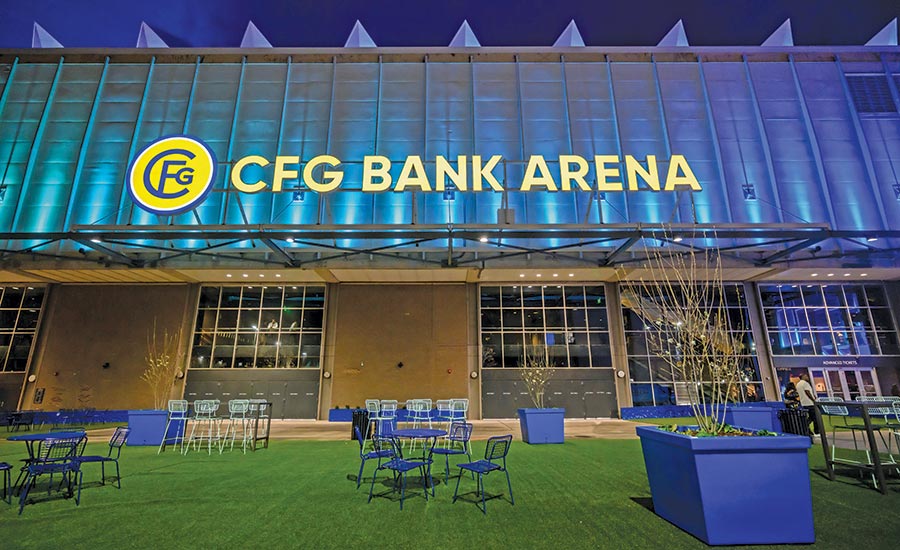
Photo courtesy Clark Construction
CFG Bank Arena
Baltimore
BEST PROJECT
Submitted By: Clark Construction
Owner: Oak View Group
Lead Design Firm: SCI Architects
General Contractor: Clark Construction
Civil Engineer: Morris & Ritchie Associates Inc.
Structural Engineer: Severud Associates Consulting Engineers P.C.
MEP Engineer: ME Engineers (Baltimore)
Environmental Engineer: McLennan Design
Geotechnical Engineer: Foundation Test Group Inc.
Subcontractors: Commercial Interiors; Freestate Electrical; JCM Associates; Berlin Steel
The $160-million renovation of what originally was the Baltimore Civic Center increased seating capacity to 13,000 seats. The 12-month project included structural improvements, upgraded concourses with new concession areas, improved acoustics, LED lighting and a makeover to the building’s exterior. The building was upgraded with modern components while still preserving the architectural and historic value of the 60-year-old building.
A new facade integrates the existing folded roof with additional sails and terrace views that celebrate Baltimore’s harbor and maritime history while paying respect to the arena’s original design. With a hard deadline for hosting a college basketball tournament, the team reached that goal by collaborating to tackle challenges and supply chain issues. When construction was scheduled to begin, design had reached only 60%, so the team began construction despite the risk of needing rework. Despite these obstacles, the team finished at budget and on schedule.
Since the schedule was tight, the project team simultaneously made decisions on critical design, constructibility and procurement to streamline the process. The team relied heavily on its subcontractors to help with coordinating among trades and managing workforce issues to boost productivity. When manufacturers quoted lead times exceeding one year for sourcing electrical switchgear, the team located gear in Maryland that could be manufactured 15 miles from the jobsite and delivered in seven months. With materials in hand, the design team was able to integrate the components into the drawings to meet design and scheduling goals.

Photo courtesy Clark Construction
One of the project’s most prominent drywall features is a roughly 86-ft-long by 100-ft-tall Tectum-lined drywall partition that flanks the event stage. Constructing the partition required an innovative approach. To build from the ground floor required subcontractor Commercial Interiors to work off boom lifts and scaffolding to hoist the partition close to the arena’s roof.
After reaching the fifth floor, Commercial Interiors had to build a false deck to accommodate the existing structure before it could continue building up.