Riverbend Meats Processing Plant
Idaho Falls, Idaho
Best Project
Submitted by: Big-D Construction
Owner: Riverbend Management
Lead Design Firm: Babcock Design Group
General Contractor: Big-D Construction
Processing Designer: E.A. Bonelli & Associates Inc.
Civil Engineer: Connect Engineering
Structural Engineer: Dunn Associates Inc.
Mechanical/Electrical Engineer: Angus-Young
Refrigeration Consultant: Innovative Refrigeration Systems
Mechanical Contractor: RM Mechanical
Electrical Contractor: Interstates Construction Services
Located just outside Idaho Falls, this ground-up facility will process Angus beef from harvest to finished packaged product.
Completed in December 2022, the facility features three primary areas, including an animal harvest and processing space, fulfillment areas with freezers, coolers and insulated metal panels for appropriate climate control as well as a corporate office area. There are seven different temperature zones throughout the plant and large fabrication areas that feature state-of-the-art equipment.
The site’s location on top of a more than 4,000-year-old basaltic lava field known as Hell’s Half Acre made for complex excavation. Crews used more than 44,250 lb of explosives to remove basalt material. With the relatively remote site, there were no existing utilities, so electric power lines were brought in from two and a half miles away, as were nine miles of gas line, with the help of diamond blade-equipped trenchers. Establishing a new water well required blasting through volcanic rock down 500 ft to reach the water table.
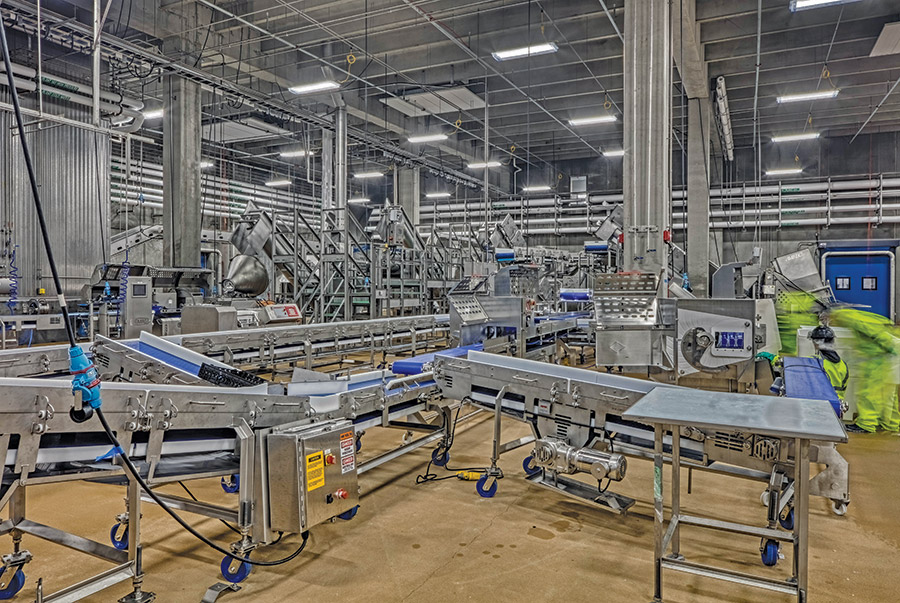
Photo courtesy of Big-D Construction
To minimize the facility’s environmental impacts, a covered 5.1-million-gallon anaerobic lagoon captures and pretreats animal waste, a small wastewater treatment building finishes the process and an onsite biogas and reuse building transforms processed waste into solid fuel to heat the building. This biogas renewable energy source fuels about 10% of the plant’s total steam demand. The treated effluent from the covered anaerobic lagoon is delivered to a 20-million-gallon storage pond where it is reused for agricultural irrigation. Nutrients in the effluent delivered to crops reduce the amount of supplemental fertilizer used on the fields.
In addition to the typical clash detection reviews, the project’s 3D model saw extensive use in helping the client visualize the plant and conduct virtual walkthroughs during design. It also enabled the design team to modify equipment placement that improved the facility’s layout.
The mechanical subcontractor used BIM extensively to model long and complex pipe run sections, which made it possible to prefabricate significant portions of work off site, including a 300-ft-long run that included 15 systems.