Digging Deeper | Office/Retail/Mixed-Use
Boston Team Builds $1.5B Tower Over South Station
Project participants contend with poor soil and little laydown space as the 51-story mixed-use structure rises over one of New England’s busiest rail hubs

Moving up toward 690 ft, the tower being built over Boston’s South Station will be one of the tallest buildings in the city.
Photo by Dave Desroches, courtesy Hines
After decades of planning, the construction of Boston’s newest office and residential tower is proving to be one of the more challenging projects the city has seen. The $1.5-billion South Station tower is steadily rising into the skyline, with the construction team, by late January, having erected 36 of its 51 stories. It took years to line up approvals and financing for the 1-million-sq-ft office and luxury condo project, given its adjacent location to an important regional transportation hub, with several government entities involved in the vetting process.
But as tough as it was to get to get to the starting line, those early pains paled in comparison with the construction challenges of building over one of the busiest rail hubs in New England with little space for staging equipment and materials in a traffic-clogged and densely developed section of downtown Boston, members of the project team say.
Even the Boston soil and bedrock proved to be balkier to work with compared ro other major cities, they note.
Yet despite all these challenges—and a temporary shutdown due to the COVID-19 pandemic shortly after work kicked off—Texas developer Hines and the construction team, led by Suffolk Construction, remain on track to deliver the tower in 2025.
The project finalized early on the purchases of critical materials such as structural steel that have long lead times as a hedge against the post-COVID surge in construction prices. Some of the construction work sequence was also reshuffled to allow key parts of the project to move ahead more quickly than initially planned.
When complete, South Station tower will feature 166 luxury condos, 685,000 sq ft of office space and 520 parking spaces. The Ritz-Carlton brand will help oversee units and related building amenities, while residential units will feature floor to ceiling windows.
“One of the greatest challenges is obviously constructing a project of this scale and complexity within a major bustling transportation hub,” says Jim Gutmann, vice president of construction at Hines. “Detailed logistical planning allowed the project to communicate our every move around the station to be coordinated with all of the railroad entities to limit disruption to the public and the operation of the station.”

When completed next year, the tower will include 166 condos and 670,000 sq ft of office space.
Rendering courtesy of Hines
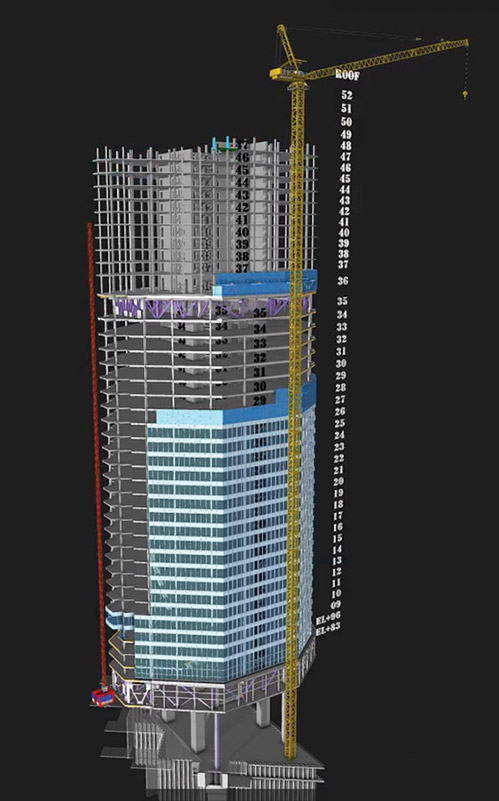
A six-story podium was built first, providing a base for the tower and crucial staging area.
Image by Viatechnik, courtesy Hines
Overcoming Early Hurdles
Work initially began in March 2020, only to be shut down for three months due to COVID-19 and the temporary closure of construction sites across Boston.
Despite that early delay, the project team has been able to keep up with the original construction schedule. “We were fighting and clawing to get back to where we were,” says Ronald Thomson, senior superintendent at Suffolk.
During the first two years, work focused on a 100,000-sq-ft expansion of the bus terminal at South Station, which the developer was required to complete under its agreements with state officials before starting work on the tower.
“When five or six o'clock came around, we couldn’t be on the [rail] platform with 120,000 people coming by.”
—Richard Pielli, Vice President & Project Executive, Suffolk Construction
The expanded terminal, which will connect with the rail station, has taken shape on foundations that were installed between the tracks in the 1980s, when plans for an expansion first got underway before stalling.
Initially, work had to be done at night to keep rail passengers safe, with a scramble to finish by the early morning arrival of the first wave of the tens of thousands commuters who pass through South Station each day. “It was challenging with the schedule,” says Richard Pielli, Suffolk vice president and project executive. “When five or six o’clock came around, we couldn’t be on the [rail] platform with 120,000 people coming by.”
As the project has moved forward, construction has shifted into the daytime. The logistics were challenging given different city, state and federal agencies that needed to be consulted as well as the challenge of building amid operation of a busy commuter rail station, according to Jeff Gouveia, Suffolk Northeast president and general manager, who spoke to ENR shortly after the team was able to host an official groundbreaking in the fall of 2022.
At that point, the team was also able to shift its focus to constructing the tower itself. An eight-level podium was the first to be built, erected directly above the railyard. It provided a base for the tower—and future expansion—while also serving as a crucial construction staging area.
Set to be a sky park when the project is complete, the 77,000-sq-ft podium roof noe provides a platform for temporary storage and assembly of equipment, as well as structural steel trusses, steel reinforcing cages and other materials before they are hoisted by cranes onto the frame of the skyscraper. “It is a balancing process,” Thomson says. “Weight is a limiting factor, and there is only so much you can lift at one time.”

A structural steel podium over the active train yard enlarges the bus terminal, connects it to the train station and will eventually serve as a landscaped roof garden for tower residents.
Photo by Dave Desroches, courtesy Hines
When completed, the sky park will feature a dining terrace, meeting spaces, walking paths, contemplative gardens and activity lawns. The first 35 floors of the tower will include office space that will occupy wide floors of 29,000 sq ft. The tower then slims down for its final ascent, topped by 16 stories of condos on smaller floor plates.
There also is innovative structural steel work on display on the 35th floor. It marks the dividing line between the office space below and condos above, with large steel trusses providing support for the floors of residential space.
“The technology really helped with the process and making everything fit in very tight quarters.”
—Ronald Thomson, Senior Superintendent, Suffolk Construction
Banker Steel Co., working with McNamara Salvia Structural Engineers, made use of zipper trusses, which allow extremely heavy trusses to be put into place in more manageable sections. The sections, in turn, allowed for more bolts and less welding, saving money and time.
The latest 3D modeling technology was also used to help plan out each step in steel erection. “The technology really helped with the process and making everything fit in very tight quarters,” Thomson says, adding that it has also been a useful tool in presentations detailing the project and its various phases.
Along with using the podium for staging, Suffolk coordinated all deliveries with a software program. Drivers are required to sign up for a time slot and face being turned away if they arrive without one. The close coordination became more important as the tower began to rise, according to project managers, with five trucks per day delivering steel and another 15 delivering concrete.
Soil conditions at the development site in Boston were also more challenging than what is typically found in some other major cities. according to the team. In New York, crews might hit bedrock after 15 ft, but at the South Station site, the construction team had to excavate down to 150 ft. “It’s strong,” says Adam McCarthy, a McNamara/Salvia principal, referring to soil and bedrock conditions in Boston, “but not like building in New York or Chicago.”
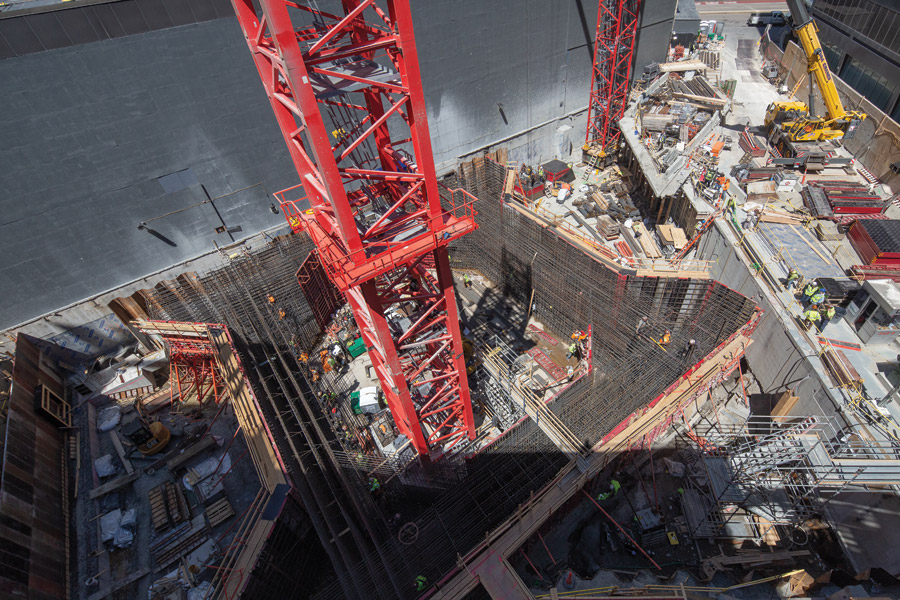
Crews construct the tower cap beam foundation, which transfers tower loads above to the deep foundation elements.
Photo by Dave Desroches, courtesy Hines
Eight supercolumns—divided between four 10-ft by 10-ft solid reinforced concrete columns and four built-up structural steel columns—support the core of the tower. These columns posed a challenge when it came to potential overheating internally given the depth of the structures.
“This is some of the strongest concrete ever seen in Boston,” says Thomson. However, he adds that the “more cement you have, the greater the strength but also the more heat involved.”
Also posing a potential overheating problem was a massive 20-ft-deep cap beam—which distributes the tower loads into the deep foundation system—as well as the arch-shaped base underneath the tower’s core.
The project team drew up a plan to simulate the temperature distribution within the extremely high-strength (12,000 psi) concrete and found ways to mitigate it by controlling within the concrete the maximum temperatures and thermal gradients. Attention was also paid to fine-tuning the admixture of the concrete.