Digging Deeper | Highway/Bridge
New Buck O’Neil Bridge Helps Smooth Kansas City Traffic
Crews navigated Missouri River ebbs and flows, plus extensive third-party coordination, as part of this design-build effort

With the new bridge in place, commuters now have direct access to and from I-35 to U.S. Highway 169 and downtown Kansas City. There is also a better connection to the Charles B. Wheeler Downtown Airport.
Photo courtesy of HNTB
The John Jordan “Buck” O’Neil Memorial Bridge has been a vital pathway in and out of downtown Kansas City, Mo., since 1956, when it opened as the Broadway Bridge. The span was renamed in memory of the former first baseman and manager of the Kansas City Monarchs, who died in 2006 and was later posthumously inducted into the National Baseball Hall of Fame for career achievement that included being the first Black coach in Major League Baseball.
Despite a short-term rehab project in 2018, the iconic triple arch bridge was quickly approaching the end of its lifespan. The Missouri Dept. of Transportation (MoDOT) selected a design-build team of HNTB as lead designer and a joint venture of Massman Construction and Clarkson Construction as contractor in early 2021. Construction began that summer.
“We teamed with Massman and Clarkson two years before the RFP came out,” says Marc Whitmore, HNTB vice president and design-build engineering group director. “We had been pursuing this job for a long time—this isn’t one we just stumbled on.”
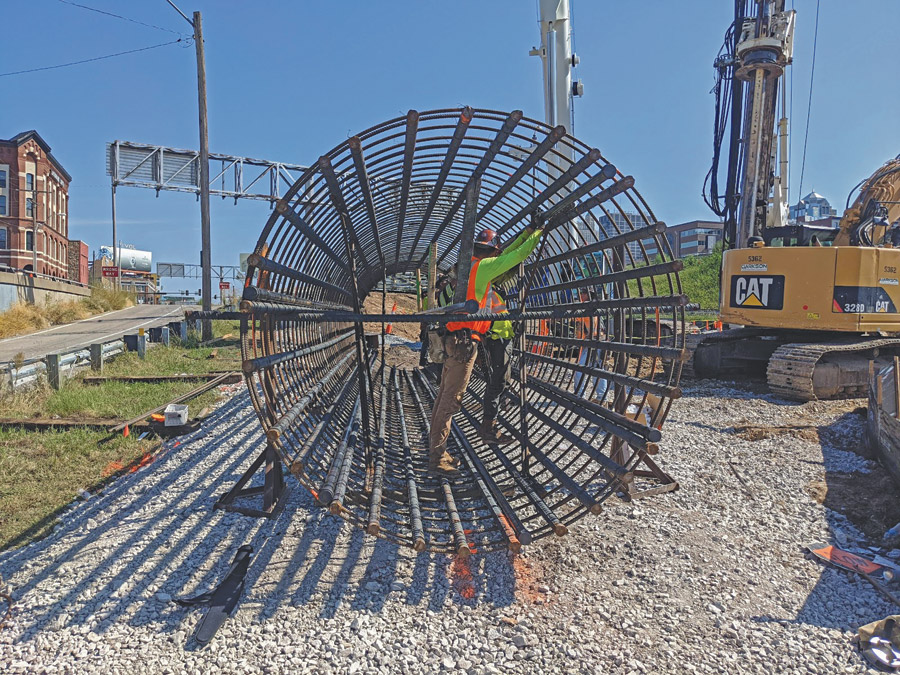
Crews installed 7 million lb of rebar, 21,000 cu yd of concrete and 18 million lb of structural steel across both the northbound and southbound bridges.
Photo courtesy of HNTB
Improving Flow
A ring of highways feeds in and out of the city’s downtown. The project is replacing a vital connection on the loop’s northwest corner. The new bridge—which is technically separate northbound and southbound spans—extends over the Missouri River.
One major feature is the direct connection from Interstate 35, both north and south across the river, to U.S. Highway 169 and dedicated lanes downtown, as well as improved access to the Charles B. Wheeler Downtown Airport.
“The bridge used to funnel everyone through one point and disperse them from there,” says James Pflum,
MoDOT project director. “This new project is really about separating that traffic where it makes sense and getting regional commuters to where they need to go and getting local commuters to downtown.”
Although the new design is less aesthetic in its design than the original Broadway Bridge, which featured three steel-tied through arch main spans, its simplicity has purpose.
“With height restrictions from the [Federal Aviation Administration] and with the railroad right there, we were not able to design a cable-stayed bridge or any real aesthetic bridge,” Whitmore says. “So the bridge is very straightforward and simple.”
About 99% of state DOT projects are design-bid-build, but using design-build for the Buck O’Neil Bridge enablied the contractor and designer to talk directly during design, Pflum says. “We also needed to meet some federal funding obligation requirements, so using design-build allowed us to do that,” he adds.
The $219-million design-build contract is part of an overall project budget of $257 million, which includes additional funding for the state DOT’s internal engineering costs and right-of-way utilities.
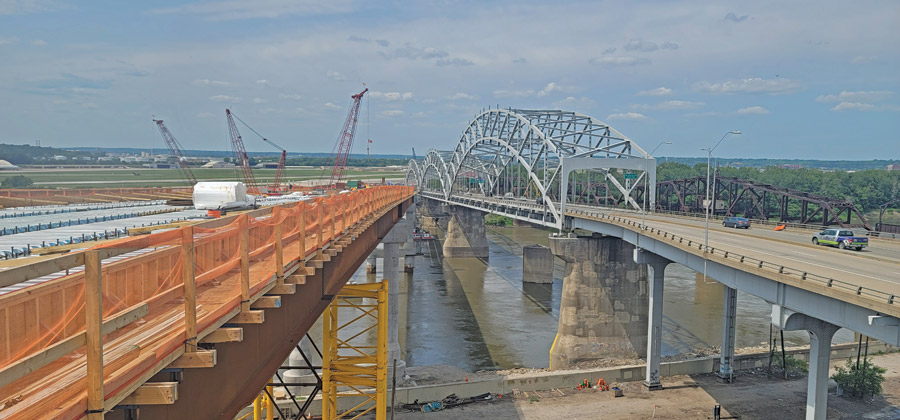
The old bridge was kept in use as long as possible to maintain traffic flow thoughout construction.
Photo courtesy of HNTB
Problem-solving
Navigating existing infrastructure and coordinating with multiple third parties required extensive collaboration.
“This project is right in the middle of Kansas City, so the [Wheeler] airport is right there, the river is right there, [and] with Kansas City being the second-largest rail hub in the nation, we have a lot of railroads right there that we have to coordinate and make sure we’re not impacting utilities,” Pflum says. “It felt like every day we were coordinating and trying to figure out how we get our project done and not impact those around us.”
“It felt like every day we were coordinating and trying to figure out how we get our project done and not impact those around us.”
—James Pflum, Project Director, Missouri Dept. of Transportation
On the north side of the river, a railroad runs adjacent to I-69, so finding a solution that did not impact rail operations was critical. Pflum added that a left-hand exit on the north end of the existing bridge had a “really nasty curve” that made the roadway prone to accidents. “One of our main goals was how do we clean up that exit to the airport on the north end ... without impacting the railroad,” Whitmore says.
Originally, the owner’s concept included significant impacts to the railroad and modifying the exit for the airport to a standard right-side exit.
“We flipped it around and provided a left-hand exit,” Whitmore says. That “is not what [the Federal Highway Administration] would call a standard access point, so to do that we had to provide a nice long turn lane and make sure our signage was appropriate.” He also notes the addition of “some extra safety precautions to provide assurance to [state and federal agencies] that we were providing a safe route the traveling public could understand.”
This solution completely avoided impacting the railroad, saving time and risk, and ultimately more than $10 million in project cost, Whitmore says. Had the team chosen to use a right-hand exit, it would have cost far more to change the existing road alignment and would have required a significant retaining wall to protect the railroad, says T.J. Colombatto, project manager at Massman-Clarkson.
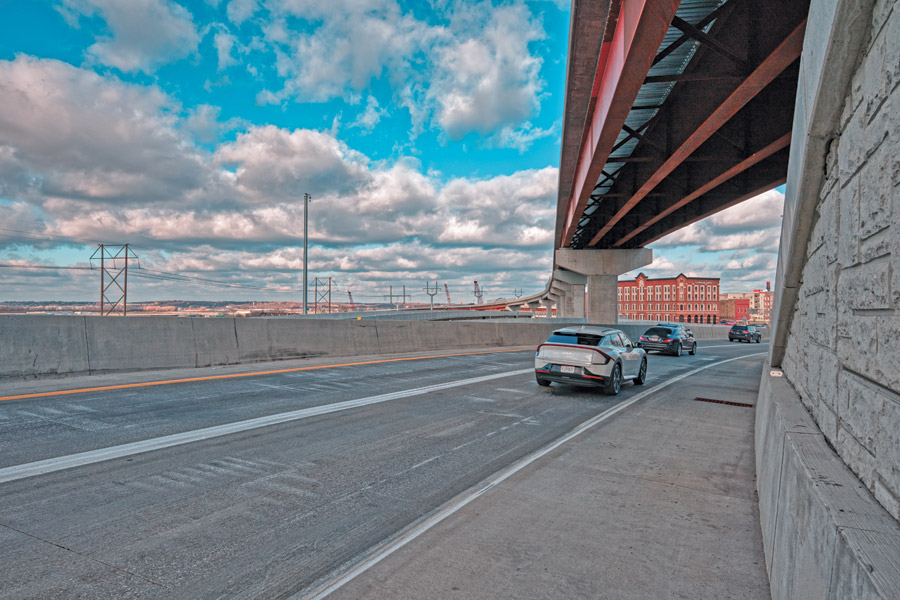
The northwest corner of Kansas City’s downtown loop will see improved traffic flow with the new bridge.
Photo courtesy of HNTB
Ups and Downs
Contending with the fickle Missouri River created added hurdles. The river’s water level hit historic lows and five-year highs during construction, not always coinciding with the water levels needed for certain work.
“Usually we’re battling high water—but we battled low water and shallow water on the north shore throughout most of the project,” Colombatto says. “Then we did have a high water event toward the end of the project during demolition.”
To keep the project moving forward, the team resequenced work where necessary. Crews performed work from four barge-mounted cranes—one with a 350-ton capacity and the others rated at 300 tons, 275 tons and 150 tons—with the largest proving particularly useful.
“In some places, we used steel girders to reduce the weight for construction purposes, such as over the interstate.”
—T.J. Colombatto, Project Manager, Massman-Clarkson
“As water gets lower, the river bank slope pushes you further away” from onshore work, Colombatto says. “We were able to use a larger crane to reach onto the bank and continue working from the water for breach piers that are adjacent to the water’s edge.”
The strategic use of existing roadways ensured that traffic could continue uninterrupted. The old bridge was kept in use as long as possible, and northbound traffic was maintained throughout construction at the request of the airport and city to ensure uninterrupted emergency services, Colombatto says.
Once the new structures were set to overlap, crews shut down southbound traffic on the old bridge and removed the southbound approaches. Northbound traffic then temporarily shifted to the old southbound lanes.
“That allowed us to complete the northbound bridge, which overlapped the old structure the most. Once that was done, we switched northbound onto its final alignment in the new crossing and reopened southbound traffic on the new southbound bridge,” he says.
Once traffic was removed from the old bridge, demolition began on the ends of the structure “to get rid of the overlap and then it progressed toward the middle,” Colombatto says.
Demolition work, begun in early 2024, was still underway as of early December. Once the ends of the old bridge were completed, the team also finished the final tie-ins, with demolition progressing on the old bridge from the ends toward the middle—with just the final two spans left to go.
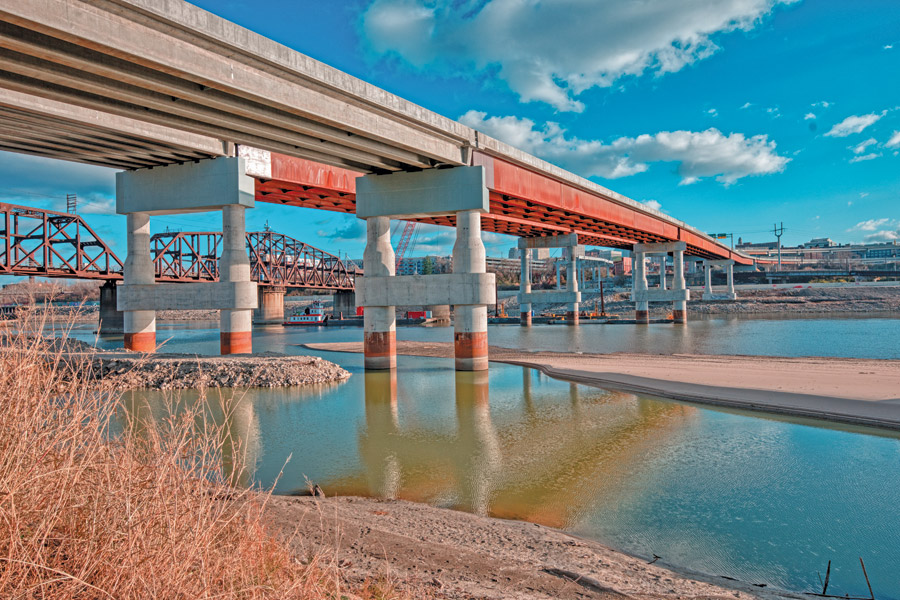
The team had to deal with river levels that fluctuated between historic lows and five-year highs.
Photo courtesy of HNTB
Stronger Stuff
Since the new Buck O’Neil Bridge is designed and built to last a century, there was a focus on reliable design techniques and materials.
The team opted for higher strength materials—such as 10 ksi concrete in the bridge’s prestressed girders and both 5 ksi concrete and 75 ksi reinforcing steel in its substructure elements. Across the entire bridge, crews installed 7 million lb of rebar, 21,000 cu yd of concrete and 18 million lb of structural steel.
“We used weathering steel, a combination of steel plate girder spans and some concrete prestressed girder spans, selecting those based on the most efficient design for the locations on the project,” Colombatto says. “In some places, we used steel girders to reduce the weight for construction purposes, such as over the interstate.”
Some of the 15,200 ft of prestressed girders were precast as well to reduce cost and schedule.
About 73 drilled shafts support the northbound and southbound bridges, each extending to a maximum depth of 122 ft below the river bottom.
“They were 11-ft-dia shafts with 10.5-ft-dia rock sockets,” Colombatto says.
The existing bridge had no pedestrian accommodations—although that did not stop river crossers from using it. The new crossing features a barrier-separated 10-ft shared-use path and a scenic overlook with benches and murals, vastly improving the space for both pedestrians and commuters.
Scope also included nine mechanically stabilized earth walls, a soil nail wall, one cast-in-place concrete wall and a large gravity block wall, which will get an artistic touch in 2025 when murals honoring Buck O’Neil are added.
As of last month, demolition work continues on the old bridge while the northbound and southbound bridges have been fully opened to traffic through a phased opening schedule.