Chelsea Viaduct Rehabilitation
Chelsea, Mass.
BEST PROJECT
Submitted By: Skanska USA
Owner: Massachusetts Dept. of Transportation
Lead Design Firm/Structural, Civil, MEP, Geotechnical, Lighting & Electrical Engineer: HNTB
General Contractor: Skanska/McCourt Joint Venture
This exceedingly complex and challenging project provided a 75-year design life for the structurally deficient critical link between the city of Chelsea, Mass., its northern suburbs and Boston. The $190-million project took place at night with heavy equipment and posed many risks. It also had significant liquidated damages for late completions and daily fines if the roadway was not restored to two lanes in each direction every morning.
The Chelsea Viaduct, which was built in the 1950s, has 76 spans that cross several city streets and the MBTA commuter rail. It carries 84,000 vehicles per day on U.S. Route 1—a primary route for North shore commuters and the MBTA’s third-largest bus route into Boston—through Chelsea.
The fast-track project in one of the most densely populated communities in the U.S. involved reconstructing on/off ramps, rehabilitating a segment of the Tobin Bridge upper deck and upgrading parking lots and surface streets below the viaduct—along with repairing and retrofitting the substructure.

Photo courtesy of Skanska
Crews used accelerated bridge construction (ABC) to demolish and rehabilitate the bridge, replacing existing spans with a combination of 313 prefabricated bridge units, 198 grid deck panels and 124 paired frames for isolated spans built using standard cast-in-place techniques. This work contributed to the replacement of 15% of structurally deficient bridge decks in Massachusetts.
Finished on budget and on schedule, the project was designed for nighttime construction atop the highway, the team devised an innovative staging design allowing work mostly on the ground in daytime. This cut two years of noisy night work, created a better site experience and generated a 10% savings for MassDOT—$17 million less than the second-place project bidder.

Photo courtesy of Skanska
In early construction, the team detected conflicts in design drawings that impacted steel fabrication. By discovering the problem early using LiDAR survey scans and proprietary BIM/VDC and steel detailer 3D models for the constructibility review, the team caught up through creative staging and project acceleration. The team experienced an additional delay due to pandemic work disruption, added requirements and many new logistics, but a resequencing effort allowed it to finish only five days beyond the original completion date.
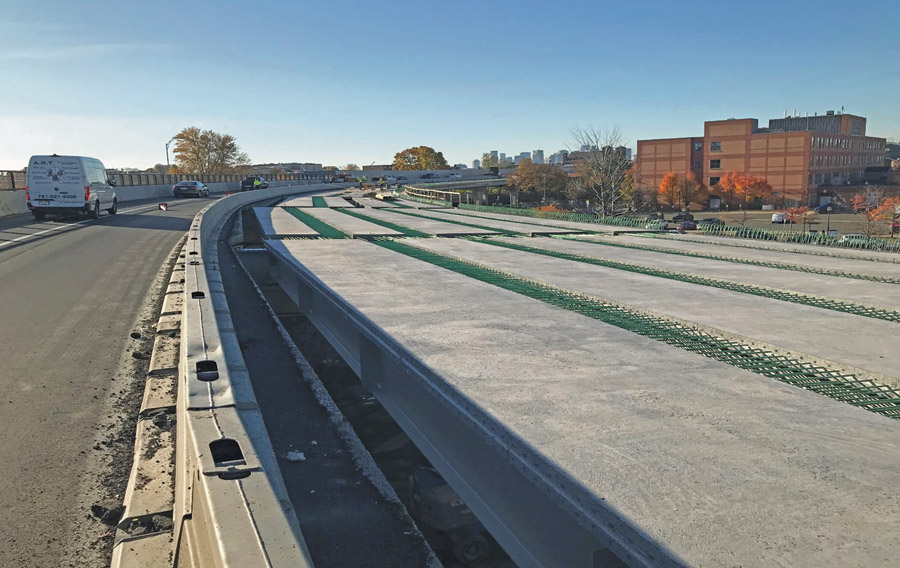
Photo courtesy of Skanska
When the team created a Level 400 Revis and Civil3D model of the aqueduct using in-house VDC technology to analyze the entire structure, it discovered sister beams for 15 bridges that were 6 in. low. While this could have led to the need for substantial steel refabrication and months of delay, early detection of the issue allowed the design engineer to fix the problem and steel was delivered to the site without delay.